How to Choose a Suitable Substrate for SSD PCB?
Solid State Drive (SSD) PCB is the heart of many computer systems, so it is important to choose the right substrate when manufacturing them. The substrate forms the backbone of the PCB, providing the mechanical support and electrical insulation required for optimal performance. The right substrate ensures the reliability, efficiency, and lifespan of the SSD. In this comprehensive guide, you will find out which substrates are suitable for SSD PCB.
The Role of Substrates in SSD PCB
The substrate is the base material to which all other components are mounted and connected through conductive pathways. It provides the necessary rigidity and strength to support the components mounted on the SSD PCB. This maintains structural integrity and prevents damage during handling and operation. It also ensures that electrical signals are routed correctly without interference or short circuits, which is particularly important in SSD PCBs. The substrate material affects signal propagation and integrity, and choosing a substrate with appropriate dielectric properties ensures minimal signal loss and distortion. It must also be compatible with various manufacturing processes, including soldering, plating, and assembly.
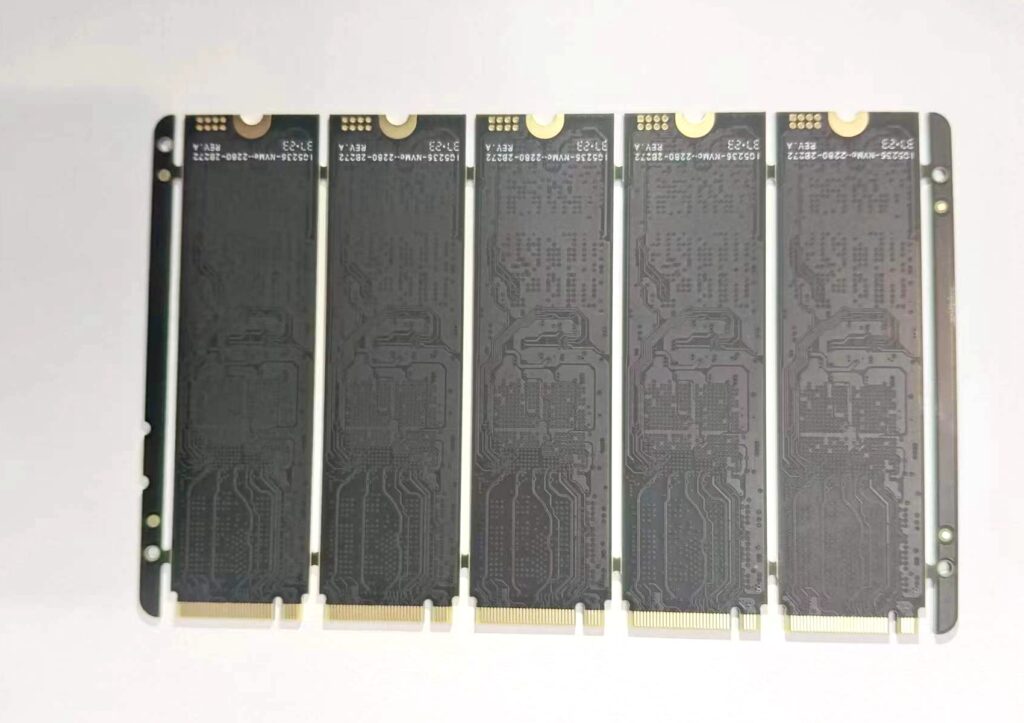
Key Factors to Consider When Selecting an SSD PCB Substrate
When selecting a substrate for an SSD PCB, we consider several factors to ensure that the substrate meets the application’s specific requirements. These include:
Material Properties: The inherent properties of the substrate material, such as thermal conductivity, dielectric constant, and mechanical strength, directly affect the performance of the SSD PCB. Materials commonly used for SSD PCB substrates include FR4, polyimide, and ceramic-filled PTFE. Each material has unique properties that make it suitable for different applications.
Thermal Management: SSD PCBs generate a lot of heat during operation, and effective thermal management is critical to maintaining performance and reliability.
Signal Integrity: High-speed data transmission in SSD PCBs requires a substrate with a low dielectric constant (Dk) and a low dissipation factor (Df) to minimize signal loss and distortion.
Comparison of Common SSD PCB Substrate Materials
SSD PCB substrates typically use various materials, each with its advantages and limitations. Here, we compare some commonly used options:
FR4: This widely used substrate material is known for its balance of cost, performance, and manufacturability. It has good mechanical strength and electrical insulation properties. However, it has relatively low thermal conductivity, which may limit high-power applications.
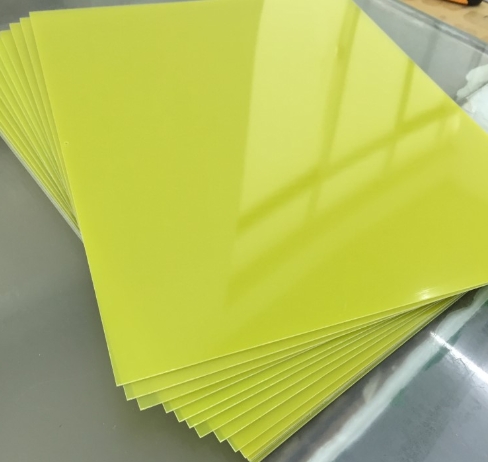
Polyimide: It has excellent thermal stability and flexibility and is suitable for high-temperature environments. It also has good mechanical properties and can withstand repeated thermal cycles.
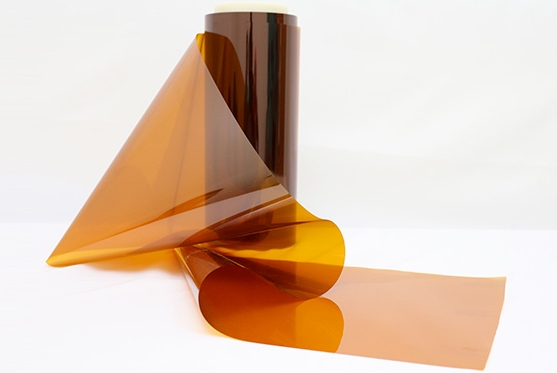
Ceramic-filled PTFE: This type of substrate has a low dielectric constant and low loss factor, which provides excellent high-frequency performance. They have outstanding thermal conductivity and stability.
Metal Core PCB: It uses a metal base (usually aluminum or copper) to enhance thermal management. It is also ideal for applications where heat dissipation is critical.
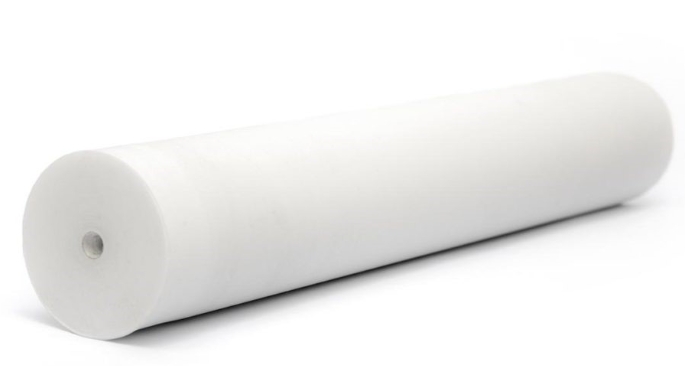
Evaluate Thermal Management Needs
Effective thermal management is critical to the reliable operation of SSD PCBs, so we also consider managing heat when selecting substrates and evaluating related thermal management needs. We will determine the heat generated by components on the SSD PCB. High-performance SSDs have faster data transfer rates and more NAND flash chips, which create more heat, so substrates with better thermal conductivity are required. We will also integrate heat sinks or heat sinks into the SSD PCB design to enhance thermal management, and we will also perform thermal simulations and tests to evaluate the performance of the substrate under actual operating conditions.
Ensuring signal integrity at high speeds
Signal integrity is critical for SSDs due to the high data rates required. Maintaining signal quality and minimizing losses are also considerations when selecting a substrate. In this case, we choose substrates with low dielectric constants to reduce signal delays and distortion, such as materials such as ceramic-filled PTFE. We perform signal integrity testing and verification with tools such as time domain reflectometry (TDR) and vector network analyzers (VNA) to measure the performance of the substrate under actual operating conditions.
Suitable Substrate Selection
The suitable substrate for SSD PCB is a complex but crucial process affecting the final product’s performance, reliability, and cost. As a professional and experienced SSD PCB manufacturer, we provide high-quality materials to our customers. We ensure that our customers get the best substrate for their specific applications.