What is the difference between ultra low loss PCB and standard PCB?
Designed for high-frequency and high-performance applications where signal integrity is critical, ultra low loss PCBs represent an advancement in the printed circuit board industry. Many industries are turning to ultra low loss PCB solutions to meet the demand for faster and more reliable electronic systems. This blog post explains the difference between ultra low loss PCBs and standard PCBs to help users understand why ultra low loss PCBs may be the best choice for their high-performance needs.
Differences in Manufacturing Materials
Ultra low loss PCBs differ from standard PCBs mainly in the materials used in their production. Standard PCBs typically use FR4, a glass-reinforced epoxy laminate known for its durability and affordability. FR4 works for general applications but struggles with high-frequency signals due to its high dielectric loss. Ultra low loss PCBs use specialized substrates like Rogers with significantly lower dielectric constants. These materials minimize signal attenuation, making them ideal for applications that require low signal loss and high-frequency performance.
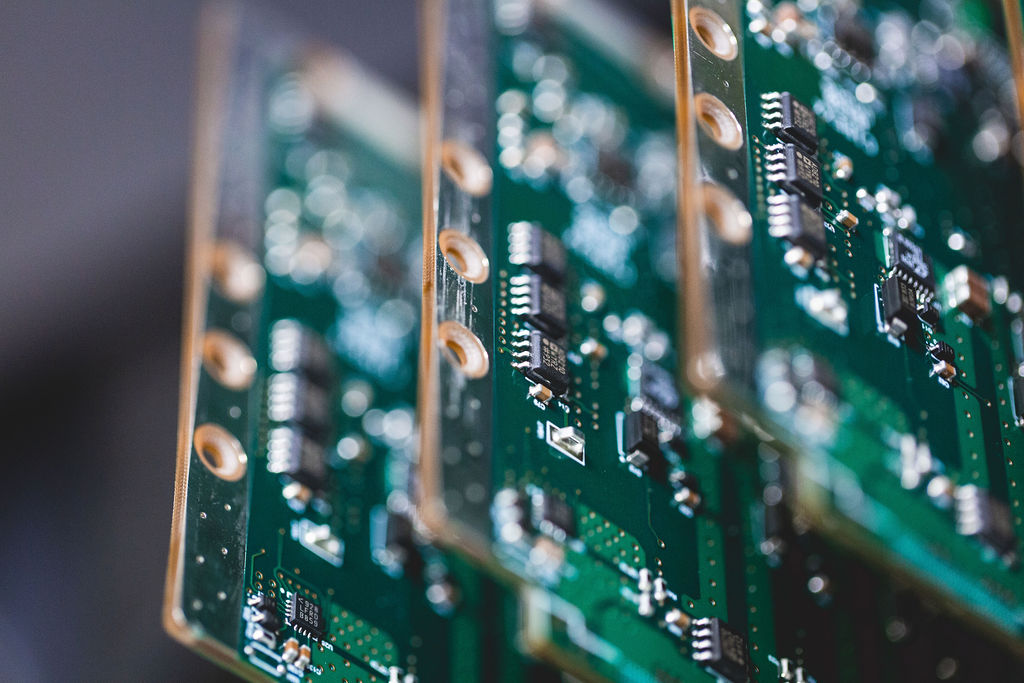
The difference in performance between them
In terms of performance, the difference between ultra low loss PCBs and standard PCBs is significant. Standard PCBs excel in low- to medium-frequency applications but struggle with high frequencies and precise signal transmission. Ultra low loss PCBs minimize signal attenuation and energy loss at high frequencies, ideal for 5G, RF systems, and high-speed data. Specialized materials in ultra low loss PCBs reduce the dissipation factor, preserving signals over longer distances and enhancing system performance.
Are ultra low loss PCBs worth the investment?
Cost is an essential factor when choosing between ultra low loss PCBs and standard PCBs. Standard PCBs are generally more affordable due to the use of low-cost materials such as FR4. Ultra low loss PCBs, while more expensive, offer enhanced performance in critical areas such as signal integrity and thermal management. For users working in industries where high precision, reliability, and long-term performance are crucial, the additional investment in ultra low loss PCBs can deliver better results and reduce maintenance costs. Although the upfront cost is higher, ultra low loss PCBs can prevent expensive performance issues in the long run, making them a wise choice for mission-critical applications.
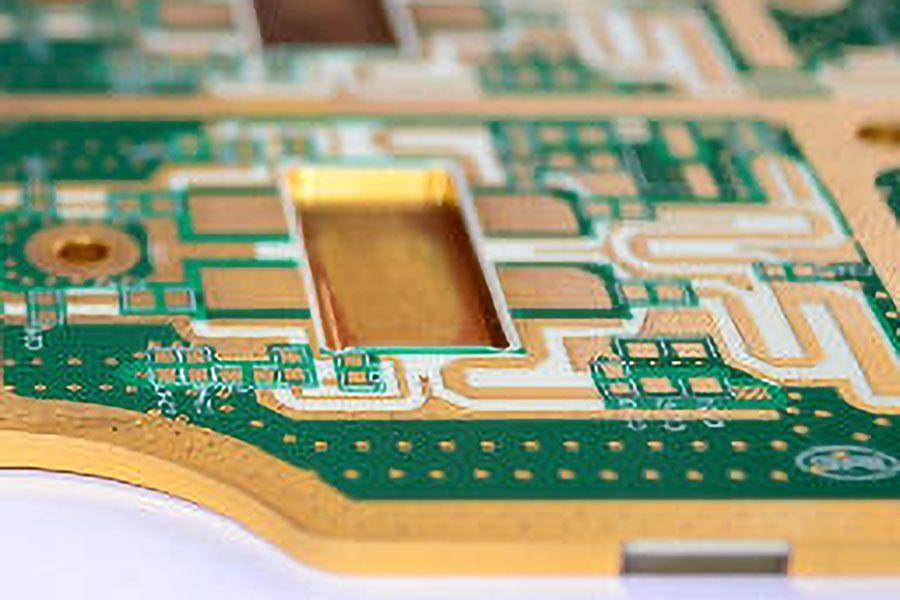
Where ultra low loss PCB are superior to standard PCBs
Another significant difference between ultra low loss PCBs and standard PCBs is their range of applications. Manufacturers use standard PCBs in everyday electronic products such as consumer devices, home appliances, and automotive systems, where signal loss is less of a concern. However, ultra low loss PCBs are essential in industries where maintaining signal strength and accuracy is critical. Applications such as satellite communications, military-grade equipment, and radar systems rely heavily on ultra low loss PCBs for optimal performance. Manufacturers design these PCBs for high-frequency and high-power applications, where even minor signal degradation can have serious consequences.
Comparison of their thermal performance
When comparing ultra low loss PCBs to standard PCBs, thermal management is an important consideration. Standard PCBs can have problems with heat dissipation in high-power applications, resulting in performance degradation or even failure over time. In contrast, manufacturers use materials with excellent thermal management properties to make ultra low loss PCBs. This allows them to operate efficiently in environments where heat generation is a concern. Advanced substrates in ultra low loss PCB not only improve signal transmission but also help dissipate heat more effectively, making them a better choice for high-power and high-frequency applications where temperature control is critical.
Ultra low loss PCB vs. standard PCB durability and lifespan comparison
Durability is another differentiating factor between ultra low loss PCBs and standard PCBs. Both PCBs are durable, but ultra low loss PCBs offer superior long-term reliability due to their advanced materials and construction. Specialized laminates in ultra-low loss PCBs provide better resistance to humidity and temperature fluctuations compared to standard FR4 materials. As a result, ultra low loss PCBs tend to last longer, making them more suitable for applications that require extended life and high reliability, such as aerospace systems, defence equipment, and medical devices.
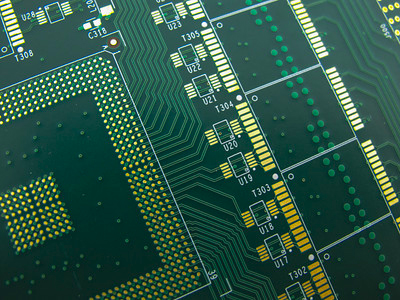
Signal Integrity and Transmission Speed
The difference between ultra low loss PCBs and standard PCBs lies in signal integrity and transmission speed. In high-frequency applications, maintaining signal integrity is critical for accurate and reliable data transmission. Standard PCBs have higher dielectric losses, which can cause severe distortion and loss of signals over long distances. However, ultra low loss PCBs are specifically designed to minimize these problems. Their lower dielectric constant and dissipation factor ensure that signals are transmitted with minimal loss, resulting in faster and more accurate data transmission. For industries where speed and precision are critical, such as telecommunications and advanced computing, using ultra low loss PCBs is not only an advantage but a necessity.
Ultra low loss PCB are the best choice for high-performance applications.
The main differences between ultra low loss PCBs and standard PCBs are materials, performance, cost, and applications. While standard PCBs are sufficient for many everyday electronic devices, ultra low loss PCBs provide the enhanced signal integrity, thermal management, and durability required for high-frequency, high-power, and mission-critical applications. For industries that demand the best performance and reliability, investing in ultra low loss PCBs is a wise decision.