Aluminum PCB thermal resistance impacts performance in what ways?
Thermal resistance refers to a material’s ability to resist heat flow and is one of the most critical factors in determining PCB performance. The aluminum PCB’s thermal resistance directly affects its ability to dissipate heat generated by components such as power LEDs, processors, or other high-power devices. Without proper heat dissipation, components may overheat, leading to premature failure or performance degradation. This blog post will explain the impact of thermal resistance on aluminum PCB performance.
The Role of the Dielectric Layer in Thermal Resistance
One key factor influencing the thermal resistance of an Aluminum PCB is the dielectric layer that sits between the aluminum base and the copper circuitry. This layer acts as an insulating material but also impacts how efficiently heat moves from the circuitry to the aluminum base. The thickness, material composition, and quality of this dielectric layer significantly influence the overall thermal resistance of the PCB. A thinner, high-quality dielectric layer reduces thermal resistance, improving heat transfer.
Choosing boards with an optimized dielectric layer for users requiring Aluminum PCB in high-power applications is critical. The heat generated from components must travel through the dielectric before reaching the aluminum core, where it can dissipate. If the dielectric material has poor thermal properties, it will act as a bottleneck, preventing heat from escaping effectively. Thus, manufacturers and users should prioritize selecting materials with low thermal resistance to improve board performance.
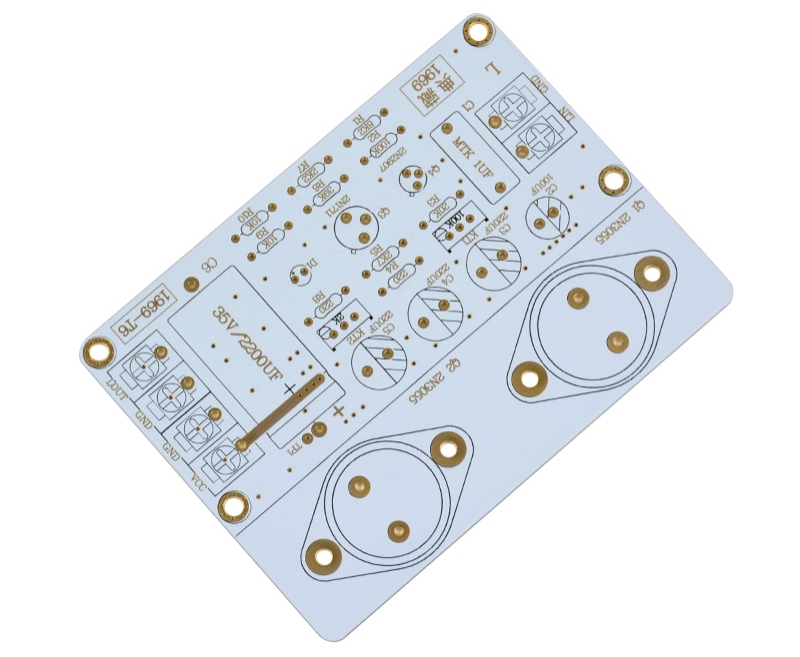
Impact on High-Power Applications
In high-power applications, the thermal resistance of an Aluminum PCB plays a defining role. High-brightness LEDs, automotive electronics, and power supplies rely on efficient thermal management to function correctly. High thermal resistance can lead to localized hotspots, causing components to operate outside their optimal temperature range. Over time, this thermal stress reduces component lifespan, impacting the reliability of the entire system.
Conversely, low thermal resistance ensures that heat is effectively transferred away from critical components, maintaining their temperature within an acceptable range. For users who depend on Aluminum PCBs for demanding applications, understanding and controlling thermal resistance is crucial for maintaining performance and extending the board’s and components’ life. Investing in a high-quality Aluminum PCB with low thermal resistance will pay dividends in long-term reliability and performance.
Material Selection and Its Impact on Thermal Resistance
The choice of materials used in constructing Aluminum PCBs is a primary factor in determining their thermal resistance. Aluminum is an excellent conductor of heat, but other materials used in the board, such as the copper layer and dielectric, can significantly impact overall performance. For example, copper’s thickness and placement on the board can either improve or hinder heat transfer.
Moreover, manufacturers can select different dielectric materials based on the application’s thermal requirements. Advanced dielectric materials designed for high thermal conductivity can significantly reduce thermal resistance, resulting in better overall heat management. Thus, when selecting an Aluminum PCB, it’s essential to consult with the manufacturer to ensure that the chosen materials are optimized for thermal performance, especially for high-power applications where thermal management is critical.
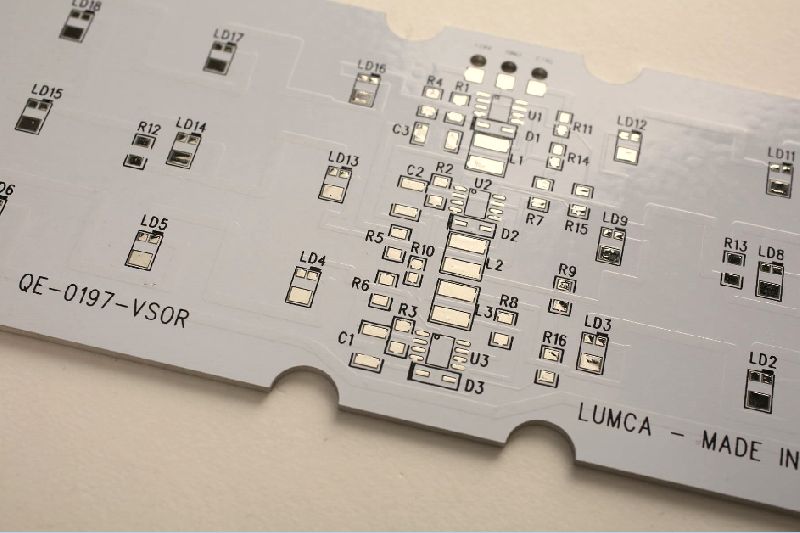
The Influence of Aluminum PCB Thickness on Heat Dissipation
Thickness is another crucial factor that impacts the thermal resistance of an Aluminum PCB. The thickness of the aluminum base, copper layer, and dielectric material all contribute to the board’s ability to transfer heat. Generally, thicker aluminum layers provide better heat dissipation, lowering the thermal resistance. However, increasing the thickness of the dielectric layer can have the opposite effect by slowing heat transfer.
For users seeking Aluminum PCBs with excellent thermal performance, striking the right balance between thickness and functionality is essential. While thicker boards may be better at dissipating heat, they can also introduce other design challenges, such as increased weight and reduced flexibility. By working closely with an experienced manufacturer, users can find the optimal balance that meets thermal and functional requirements without compromising the board’s performance.
Thermal Management and Overall System Efficiency
Thermal resistance is not only a matter of protecting components from overheating; it also plays a significant role in the overall efficiency of an electronic system. Excess heat can directly affect the system’s energy efficiency in applications like LED lighting or power electronics. Higher thermal resistance in an Aluminum PCB can result in more significant energy losses as heat builds up and increases the system’s operating temperature.
In contrast, reducing thermal resistance ensures energy is not wasted as excess heat. This is particularly important in energy-sensitive applications where every watt counts. Users of Aluminum PCBs can benefit from improved efficiency, which translates to reduced operational costs and lower energy consumption. In short, controlling thermal resistance not only improves performance but also makes systems more cost-effective and sustainable.
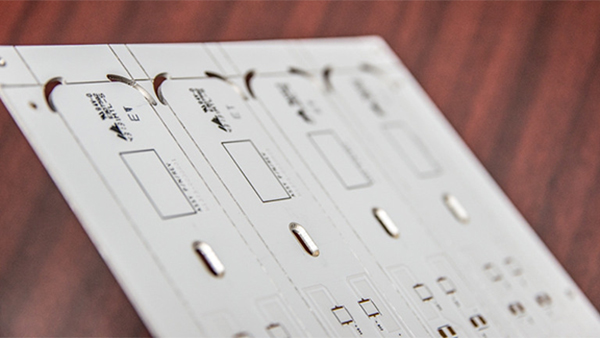
Aluminum PCB Designing for Low Thermal Resistance
Design considerations also play a role in determining the thermal resistance of an Aluminum PCB. The layout of components, copper traces, and thermal vias can all influence how effectively heat is managed. For instance, placing heat-generating components closer to thermal vias or designing wider copper traces can help dissipate heat more efficiently. Similarly, multi-layer designs with embedded thermal layers can reduce thermal resistance and improve heat dissipation.
For users looking to optimize the thermal performance of their Aluminum PCB, working with a manufacturer that offers custom design services is essential. By tailoring the design to meet specific thermal requirements, users can ensure that their boards maintain optimal performance, even under high-power conditions. With careful design and material selection, the thermal resistance of an Aluminum PCB can be minimized, ensuring long-term reliability and efficiency.
Importance of Controlling Thermal Resistance of Aluminum PCB
The thermal resistance of an aluminum PCB is a critical factor that directly affects its performance, especially in high-power applications. By understanding the role of materials, design, and construction techniques, users can make an informed decision when selecting a PCB that fits their needs. Whether optimizing high heat dissipation or ensuring long-term reliability, controlling thermal resistance is critical to maximizing the efficiency and performance of aluminum PCBs.