Can Rigid-flex PCB support HDI designs?
In the dynamic world of electronics, the innovative Rigid-flex PCB and HDI designs are revolutionizing the miniaturization and performance of modern devices. As consumer demands for smaller, more efficient, and more reliable products continue to escalate, the integration of these two groundbreaking technologies has become a pivotal consideration for manufacturers. But the question arises: Can Rigid-flex PCBs support HDI designs? This blog post aims to answer that question and guide you through the capabilities, benefits, and applications of Rigid-flex PCBs in supporting HDI designs, sparking your curiosity and inspiring you with the possibilities.
Introduction to Rigid-flex PCB
Rigid-flex PCBs are a hybrid solution that combines the benefits of rigid PCBs with the flexibility of flexible PCBs. These circuits consist of both rigid and flexible sections, allowing the board to be used in applications where space is at a premium and a combination of flexibility and durability is required. Rigid-flex boards are often used in compact, high-performance electronics such as smartphones, medical devices, and aerospace systems.
The rigid sections of the board are typically used for mounting components that require stability. In contrast, the flexible sections enable the PCB to conform to various shapes, allowing it to be bent or folded. The flexibility makes Rigid-flex PCBs particularly useful in applications where space constraints or the need for dynamic movement are factors. For manufacturers, Rigid-flex PCBs offer both design flexibility and the ability to meet the demands of high-performance applications.
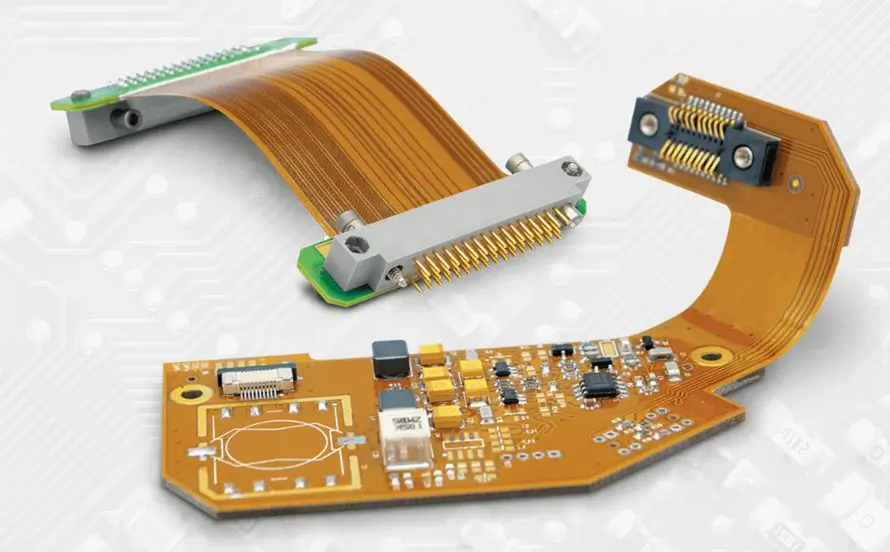
Introduction to HDI PCB
HDI PCBs, or High-Density Interconnect PCBs, are advanced circuit boards that use finer lines, smaller vias, and more tightly packed components to achieve higher density than traditional PCBs. They are designed to meet the needs of modern electronics, where the demand for higher performance and smaller, more compact designs is ever-growing. HDI PCBs allow for more complex circuits in a smaller space, which is essential for applications such as smartphones, tablets, wearables, and high-performance computing.
The primary advantage of HDI technology lies in its ability to support high-speed signal transmission and complex circuit designs, making it ideal for high-performance applications where signal integrity and reliability are paramount. HDI designs incorporate advanced manufacturing techniques such as micro vias, blind and buried vias, and laser drilling. These techniques are instrumental in achieving greater density and smaller footprints, making HDI boards an ideal choice for products that need to pack more functionality into a smaller, lightweight package.
Rigid-flex PCB supports HDI design
Yes, Rigid-flex PCBs can indeed support HDI designs, but this integration demands specialized expertise and precise manufacturing techniques. The fusion of the high-density capabilities of HDI designs with the flexible nature of Rigid-flex PCBs offers a potent solution for industries that require both high-performance and compact, adaptable designs. The ability to incorporate HDI designs into the rigid-flex structure opens up new possibilities for electronic devices, particularly in industries such as telecommunications, automotive, and medical equipment.
Engineers typically make rigid-flex PCBs with multiple layers, and incorporating HDI elements into these layers provides greater functionality in a smaller space. Advanced manufacturing techniques, such as microvias and laser drilling, enable engineers to implement HDI designs in both the rigid and flexible areas of the board. These technologies enable smaller, more efficient circuit layouts that designers can integrate into flexible sections of the board, offering high-density performance even in tight spaces.
Moreover, the use of high-density components in the rigid sections of the PCB complements the board’s flexible nature, allowing for greater performance without compromising on size or durability. This combination of flexibility and high density is particularly valuable in applications that require both dynamic movement and advanced functionality, such as wearable medical devices or aerospace equipment.
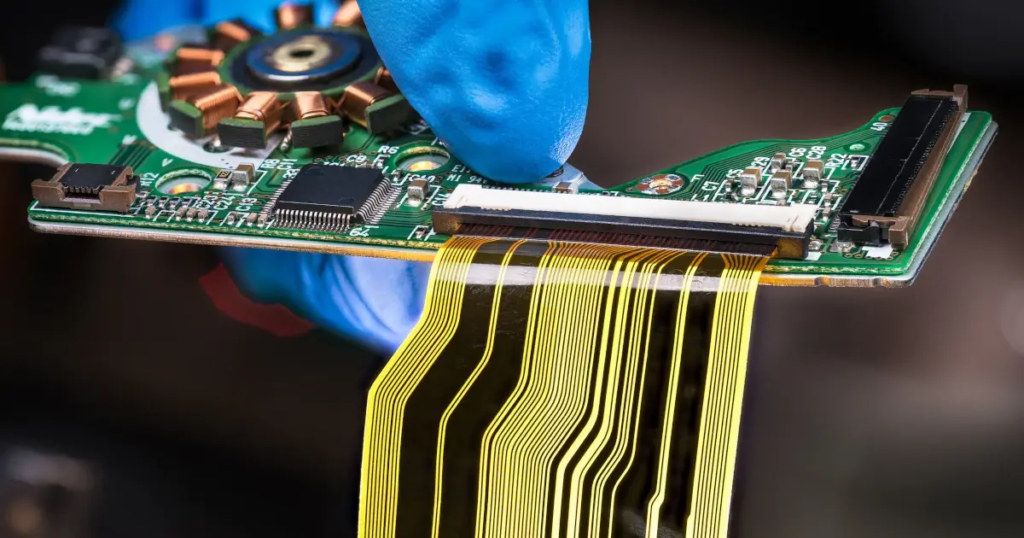
Several Benefits of Integrating HDI Designs
The integration of HDI designs into Rigid-flex PCBs brings several key benefits, especially in terms of performance, size, and reliability. First and foremost, combining these two technologies allows for higher circuit density without increasing the physical size of the PCB. This is critical for applications with limited space but high-performance requirements, such as portable consumer electronics and wearable devices.
Another major benefit is the enhanced signal integrity that HDI designs can provide. By reducing the number of layers and vias, HDI technology allows for faster signal transmission with less interference. This makes Rigid-flex PCBs with HDI designs ideal for high-speed applications, such as wireless communication devices and high-frequency systems. The smaller traces and vias in HDI designs also reduce the overall resistance and inductance of the circuit, leading to lower power consumption and faster processing speeds.
Finally, integrating HDI designs into Rigid-flex PCBs significantly enhances the board’s overall durability. The PCB’s flexibility allows it to withstand mechanical stresses, while the rigid areas provide the stability needed to support heavy components. This combination makes Rigid-flex PCBs with HDI designs highly reliable, even in harsh operating environments such as industrial or aerospace applications, giving you the confidence that your devices will perform consistently under challenging conditions.
Applications of Rigid-flex PCB with HDI Designs
Rigid-flex PCBs with HDI designs are particularly valuable in industries where performance, reliability, and compactness are essential. Some of the key applications, including Smartphones and Wearables, demand compact designs with high-density components to ensure optimal performance in a small form factor. Rigid-flex PCBs with HDI designs not only enable these devices to pack more features into a smaller space but also impress with their efficiency and space-saving potential, maintaining high performance in a compact package. Medical Devices, such as Wearable health monitors, hearing aids, and medical sensors, often need to fit into small enclosures while offering high reliability. Rigid-flex PCBs with HDI designs can meet these requirements by providing flexible, high-density circuits that engineers can integrate into compact medical devices.
Automotive and Aerospace, Both industries require durable, compact, and high-performance PCBs for applications such as navigation systems, sensors, and communication devices. Rigid-flex PCBs with HDI designs can withstand the mechanical stresses and environmental conditions typical in these environments while supporting advanced functionality. Consumer Electronics, From cameras to gaming consoles, Rigid-flex PCBs with HDI designs allow manufacturers to create cutting-edge products that are both compact and high-performing.
These applications demonstrate the versatility of Rigid-flex PCBs with HDI designs, making them ideal for sectors that demand the highest performance and miniaturization.
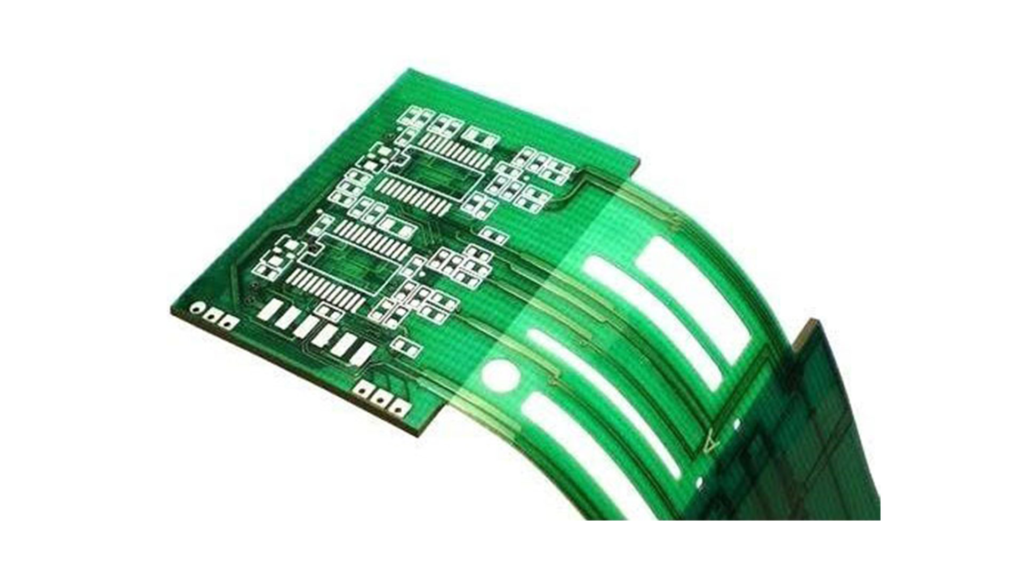
Manufacturing Considerations for Rigid-Flex Boards with HDI Designs
Manufacturing Rigid-flex PCBs with HDI designs requires specialized equipment and expertise. The process includes several steps that integrate both the rigid and flexible areas of the board seamlessly without compromising performance. The use of advanced techniques, such as laser drilling, micro via technology, and multi-layer stacking, allows for the creation of high-density interconnections that are essential for modern electronic devices.
In addition, quality control is crucial during the manufacturing of these complex boards. Engineers must precisely align each layer to ensure correct integration of the HDI features within the rigid-flex structure. Any misalignment can lead to faulty connections, reduced performance, or premature board failure. Therefore, collaboration with experienced PCB manufacturers who understand the intricacies of both Rigid-flex and HDI technologies is vital to ensure a successful product.
Future Development Trends and Application Areas
As technology continues to evolve, the demand for smaller, faster, and more reliable electronic devices will only increase. This places greater emphasis on the need for Rigid-flex PCBs that can support advanced HDI designs. In the future, we can expect continued advancements in manufacturing techniques, materials, and design tools, all of which will make the integration of Rigid-flex PCBs and HDI designs even more efficient and cost-effective.
For example, innovations in 3D printing and additive manufacturing may allow for even more complex, high-density designs in Rigid-flex PCBs. Additionally, the use of advanced materials such as high-frequency laminates and conductive inks could further enhance the performance of these boards, allowing them to support even faster speeds and higher frequencies. As these technologies progress, we can anticipate a wider range of applications that rely on Rigid-flex PCBs with HDI designs, particularly in cutting-edge fields such as IoT, autonomous vehicles, and quantum computing.
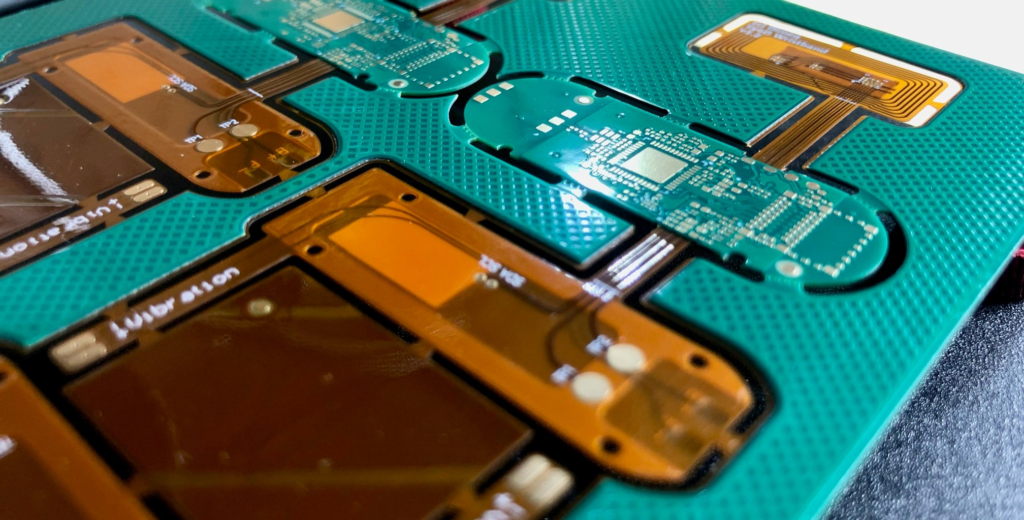
The Future of Rigid-flex PCB in HDI Designs
Rigid-flex PCBs are fully capable of supporting HDI designs, providing a versatile solution for manufacturers in various industries that require compact, high-performance, and durable electronic devices. Whether you’re developing a consumer electronic device, a medical instrument, or an aerospace component, understanding how Rigid-flex PCBs and HDI designs work together can help you make more informed decisions when selecting materials for yours.