What are the available options for customizing multi-layer PCB?
In today’s rapidly evolving electronics world, as the demand for advanced and miniaturized electronic products grows, the custom multi-layer PCB is also increasing. Custom multi-layer PCBs offer a variety of benefits, including improved performance, greater cost-effectiveness, and the ability to meet specific design requirements for different applications. Custom multilayer designs enable engineers and manufacturers to achieve the exact functionality and reliability they need for their unique projects. In this blog post, we will explore the various options for custom multi-layer PCBs to help users understand the best choice for their needs.
Understanding Multi-Layer PCB Design and Structure
Before delving into the customization options, it is essential first to understand what constitutes a multi-layer PCB. Multi-layer PCBs comprise multiple conductive layers stacked on top of each other. These layers are interconnected through vias, which allow electrical signals to pass from one layer to another. Typically, multi-layer PCBs consist of three or more layers, but they can be built with many more depending on the design’s requirements.
When customizing a multi-layer PCB, several design elements must be considered. The number of layers, the type of material used for each layer, the layer thickness, and the type of vias all play a critical role in the PCB’s overall performance. Customization options allow users to adjust these parameters to ensure the board meets their specific applications’ functional and manufacturing requirements.
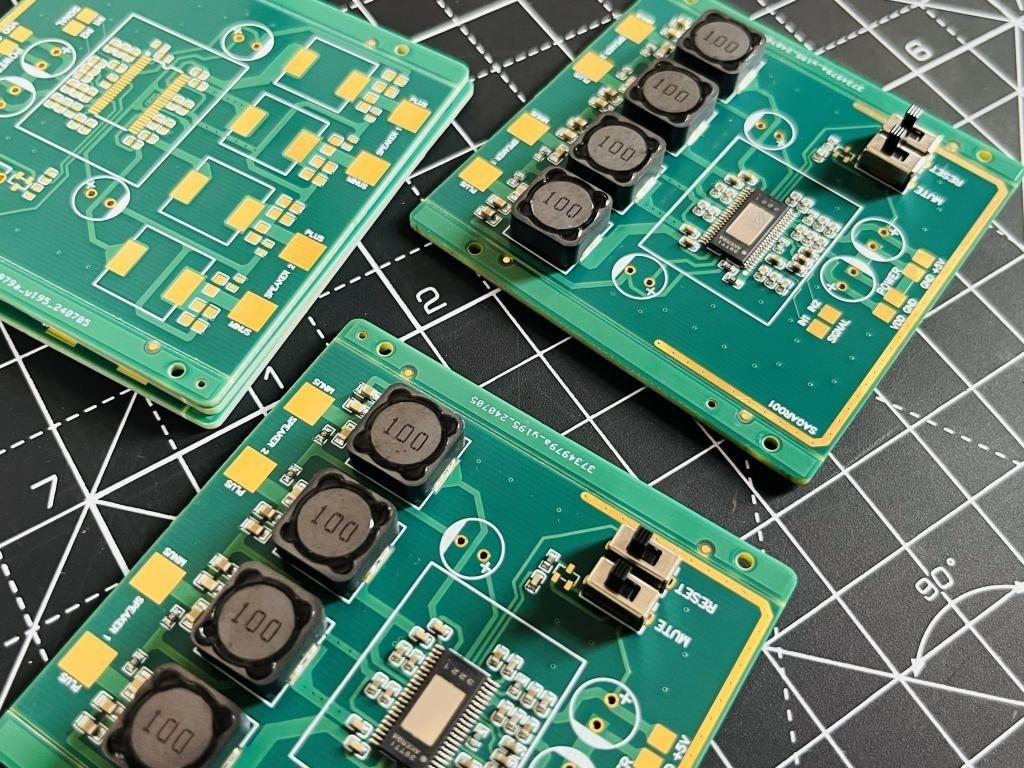
Options for Customizing the Number of Layers
One of the most important decisions when designing a multi-layer PCB is determining the number of layers required. A basic multi-layer board might have four layers, but more complex designs can include six, eight, or even twelve layers. The number of layers in the PCB is determined mainly by the complexity of the circuit and the space constraints.
A four-layer PCB might suffice for more straightforward applications like low-frequency circuits. However, more advanced applications, such as high-frequency RF circuits, high-speed digital circuits, or power distribution systems, often require more layers. Customizing the number of layers in a PCB helps engineers ensure that the design meets specific signal routing and power delivery requirements. Adding extra layers also allows for more compact designs, improving the device’s overall size and form.
Different Custom Material Options
Selecting suitable materials for multi-layer PCB customization is crucial for ensuring performance, reliability, and manufacturability. PCB materials can vary widely, and each offers different properties that affect signal integrity, thermal management, and electrical performance.
The most common material used for multi-layer PCBs is FR4, a flame-retardant epoxy resin-based laminate. However, designers may use alternative materials like Rogers, Teflon, or polyimide for high-frequency or high-performance applications. Engineers specially design these materials to minimize signal loss, improve heat dissipation, and enhance the overall reliability of the board.
Choosing the suitable material is essential to customizing multi-layer PCBs to meet specific needs. For example, if your application requires high-speed data transmission, using a material with a low dielectric constant and low loss tangent is critical. Customizing material options helps ensure that the board can handle the demands of your particular application, whether it’s high-frequency, high-power, or high-speed electronics.
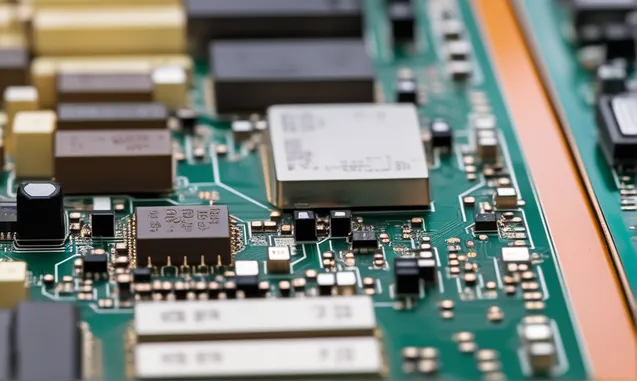
Customization of Different Via Types
Vias connect the different layers of a multi-layer PCB. There are several types of vias, including through-hole vias, blind vias, and buried vias. The choice of via type and size plays an important role in the overall functionality of the PCB and the space available for routing electrical signals.
When customizing multi-layer PCBs, you can choose from various options to optimize space and signal routing. For example, micro vias are often used in high-density designs where space is at a premium, while blind vias allow connections to only specific layers of the PCB. Additionally, buried vias allow for internal connections between layers, which can be particularly useful in complex, multi-layer designs.
Customization of via types, sizes, and placement can improve signal integrity, reduce the PCB’s size, and enhance performance. Moreover, ensuring the design suits the visa types can help minimize manufacturing costs and prevent issues like signal interference or electrical noise in high-speed applications.
Layer Thickness and Trace Width Customization
The thickness of each layer and the width of the traces within the multi-layer PCB are critical factors influencing performance. Trace width, in particular, affects the PCB’s current carrying capacity, impedance, and overall signal integrity. By customizing trace width, engineers can ensure that the board performs optimally under the specified operating conditions.
For example, high-speed digital circuits require precise trace width customization to match impedance requirements, reducing the risk of signal reflection and interference. In power distribution systems, customizing the trace width can also help ensure that the board can handle high current levels without overheating.
Layer thickness also plays a vital role in the PCB’s performance. Thicker copper layers can improve current handling capabilities, while thinner layers may be necessary to reduce overall size or improve signal integrity. Customizing trace width and layer thickness allows for better performance tuning of multi-layer PCBs, ensuring that the board meets the specific application’s needs.
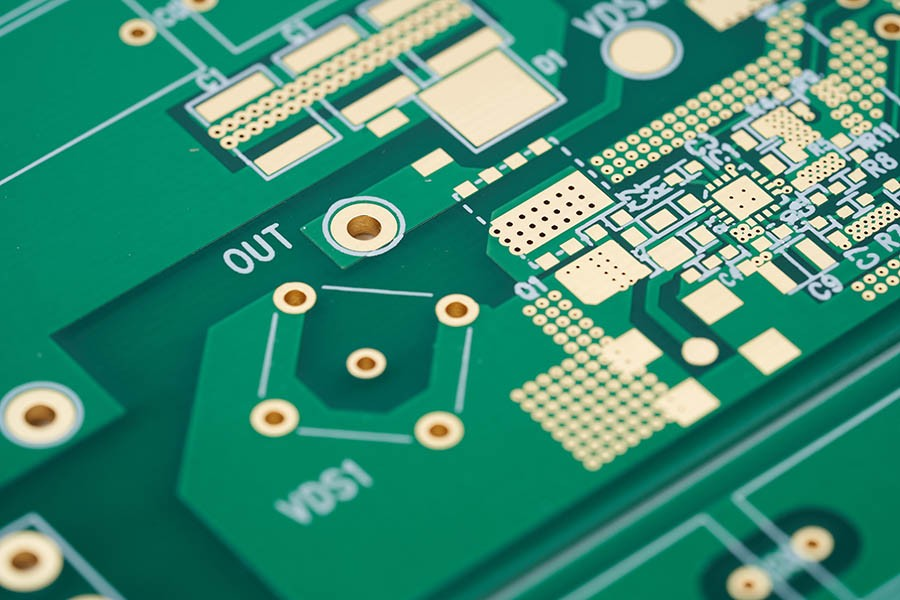
Advanced Surface Finish and Coating Options
When customizing multi-layer PCBs, surface finish and coating options should also be considered. The surface finish refers to the coating applied to the copper pads and traces on the PCB, which ensures proper solderability and electrical performance.
Popular surface finishes for multi-layer PCBs include HASL (Hot Air Solder Leveling), ENIG (Electroless Nickel Immersion Gold), and OSP (Organic Solderability Preservative). Each of these finishes provides different durability, solderability, and cost benefits. For example, engineers often choose ENIG for high-performance applications due to its excellent corrosion resistance and flat surface. At the same time, HASL is more cost-effective and suitable for lower-end consumer electronics.
Coating options such as conformal or protective coatings can protect the board from moisture, dust, and chemicals. These coatings are essential for enhancing the reliability of multi-layer PCBs, especially in harsh environments or outdoor applications.
Choosing the Best Customization Options for Your Multi-Layer PCB
Custom multi-layer PCBs allow manufacturers and engineers to optimize their electronic products’ design, performance, and cost. From selecting the number of layers and materials to customizing vias, trace widths, and surface finishes, various options are available to customize PCBs to meet the specific needs of any application. Whether for consumer electronics, medical devices, or automotive systems, the correct elements of a custom PCB ensure it performs as expected, providing reliability, durability, and efficiency.