What factors should I consider when purchasing a Power Supply PCB?
Choosing the proper power supply PCB is essential for ensuring your device functions reliably and efficiently. Power supply PCBs are integral to converting and managing power and providing energy to various electronic systems. However, selecting the right one for your specific needs can be complex, as it involves considering multiple technical factors, such as power requirements, material choice, heat dissipation, and more. Whether you are designing a small consumer gadget or a high-power industrial system, understanding the key factors in choosing a power supply, PCB will ensure optimal performance and longevity. This article will guide you through the essential considerations when purchasing a power supply PCB. These factors range from material selection to layout considerations and thermal management, influencing the board’s efficiency, durability, and cost-effectiveness. By understanding these elements, you can make an informed decision that meets your power needs while ensuring reliable and efficient operation for your system.
Basic Requirements of Power Supply PCB
When choosing a power supply PCB, the first consideration is its basic requirements. The design of a power supply PCB must meet specific power and current demands. Depending on the application, the PCB’s size, thickness, and current carrying capacity must be precisely designed. A power supply PCB not only needs to provide stable power but also needs to have good heat dissipation capabilities. Heat dissipation design is crucial for the stability of the power supply board, as a well-designed heat dissipation system can significantly extend its lifespan.
Moreover, signal integrity and power noise suppression are essential factors. The design of a power supply PCB must ensure stable power signals while preventing electromagnetic interference (EMI). This is particularly critical as EMI can affect the system’s performance and negatively impact other devices. Therefore, proper wiring and filtering design are essential when designing power supply PCBs.
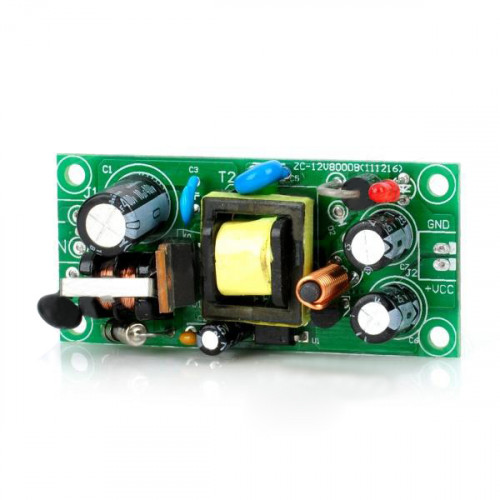
Load Capacity and Power Requirements
Understanding the load capacity and power requirements is crucial when purchasing a power supply PCB. Different applications require power supply PCBs with varying levels of power. For example, high-power devices need high-power PCBs, while smaller devices may only require low-power designs. It’s essential to ensure the power supply PCB matches the application’s power needs to avoid power shortages or system instability.
Along with power requirements, current carrying capacity must also be considered. Excessive current can cause the PCB to overheat, which affects the equipment’s longevity. When designing, it’s essential to calculate the current density for each channel and select the appropriate conductor width and thickness to ensure current flows without overheating issues. High current density increases the difficulty of heat dissipation and may cause the power supply board to fail.
Material Selection for Power Supply PCB
Choosing materials for power supply PCBs directly impacts the circuit board’s performance and stability. Common materials include FR4, aluminum-based boards, and ceramic substrates, each suitable for different applications. For example, FR4 is a cost-effective material commonly used in most power supply PCBs. In contrast, aluminum-based boards are widely used in high-power designs due to their excellent heat dissipation properties. Ceramic substrates are used in high-frequency, high-power, and high-temperature environments.
In addition to base materials, the thickness of the copper layers is another critical factor. Thicker copper layers offer better current carrying capacity, making them suitable for high-power applications. In contrast, thinner copper layers are ideal for low-power, smaller devices. When selecting a power supply PCB, choosing the right materials and copper thickness is essential to ensure stable operation and optimal performance.
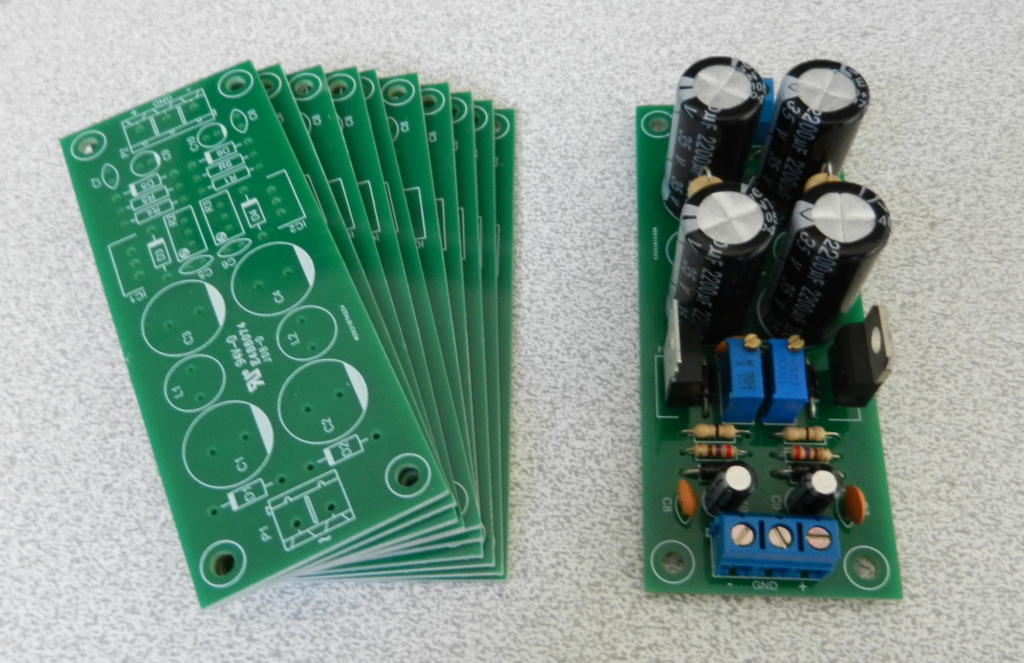
Choose an effective heat dissipation design
Heat dissipation design is one of the most critical factors to ensure stable operation of power supply PCBs. Heat dissipation can be achieved through various methods, such as using thermally sensitive materials, designing heat dissipation holes, and using heat sinks. Proper heat dissipation design can significantly lower the operating temperature of the power supply PCBs, preventing failures caused by overheating.
In addition to traditional heat sinks, many power supply PCBs adopt advanced heat dissipation technologies such as heat balancing and liquid cooling. These technologies enhance the heat dissipation effect and ensure the power supply PCB maintains a stable temperature even under high power loads. Choosing a PCB with an effective heat dissipation design can significantly improve the reliability and lifespan of the device.
Reliability and Lifespan of PCB
The reliability and lifespan of a power supply PCB are essential for long-term stability during operation. Consumers must ensure that the PCB’s materials and processes can withstand prolonged high-load operation when purchasing. High-quality power supply PCBs can endure extended periods of high-power usage without performance degradation, guaranteeing long-term system stability.
Additionally, environmental tolerance is an essential factor in PCB reliability. Temperature, humidity, and vibration can all affect the performance of the power supply PCB. Power supply PCBs may need enhanced resistance to high temperatures and moisture in some unique environments. Therefore, users should confirm that the PCB can operate in the intended environment to ensure long-term stability.
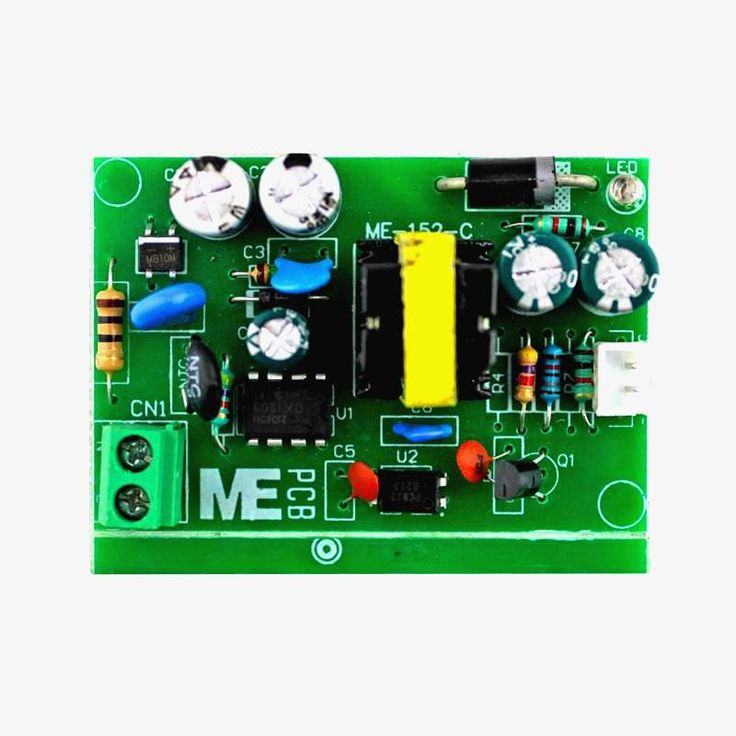
Size and Layout of PCB
The size and layout are other essential aspects to consider when purchasing power supply PCBs. Different applications have different size requirements for PCBs, and selecting the proper size can ensure easy installation and better efficiency. A well-designed layout can help reduce current path lengths, improve current flow efficiency, and minimize energy waste.
When designing the layout of power supply PCBs, it’s essential to consider the placement of power components to maximize space utilization. A well-planned layout can reduce signal interference and improve overall performance. Additionally, it’s necessary to consider how the power supply PCB will interface with other components, ensuring a seamless integration with the overall system.
Cost and Cost-Effectiveness of PCB
Finally, cost-effectiveness is a crucial consideration when purchasing power supply PCBs. High-performance PCBs are typically more expensive, but overly costly power supply PCBs may not be the best choice for low-power devices. When selecting a power supply PCB, users must balance performance and cost to ensure the best value.
Furthermore, the complexity of the process and the choice of materials during the design and manufacturing of the power supply PCB will also impact the cost. Choosing a design that fits the needs while keeping the budget in mind can help achieve a cost-effective solution. Proper budget planning allows users to get the best value without sacrificing performance.
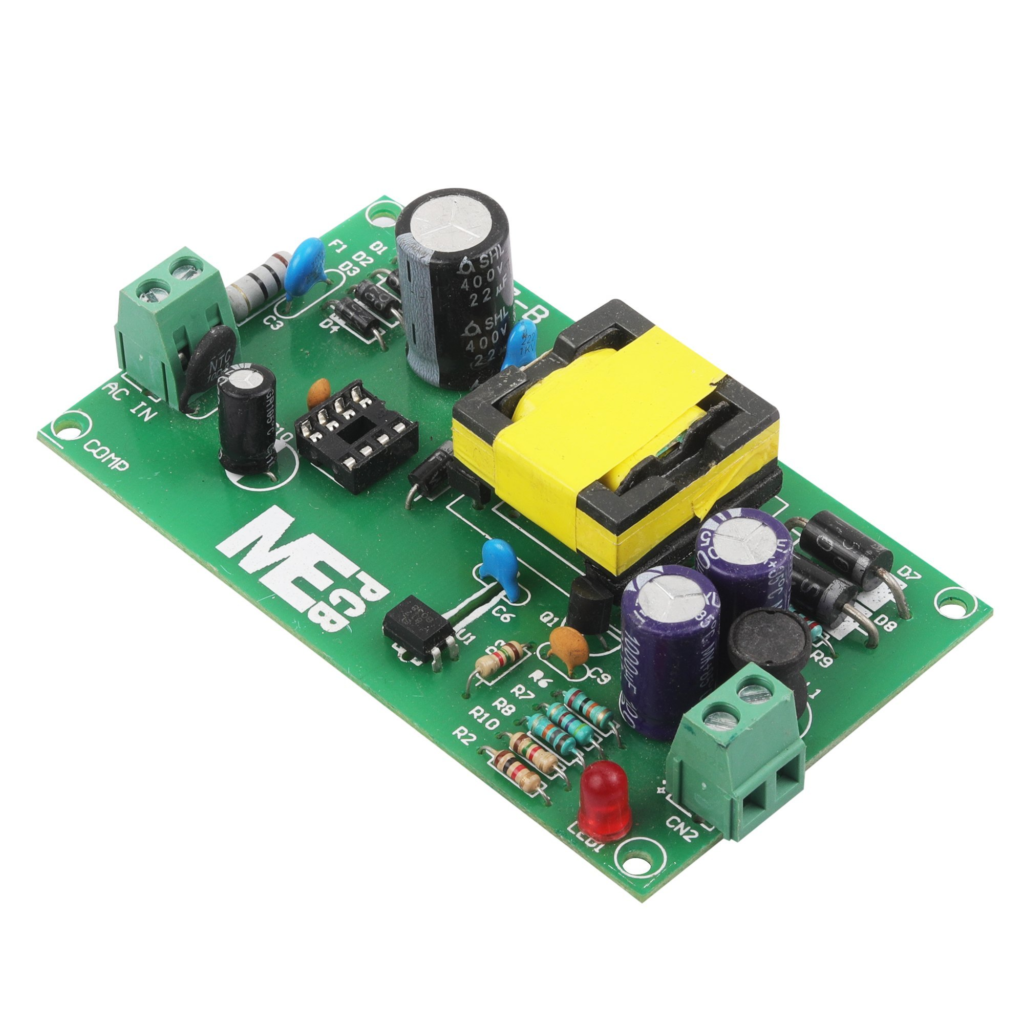
Making the Right Choice for Your Power Supply PCB
Choosing the right Power Supply PCBs is critical to ensuring the performance and longevity of your electronic device. By considering factors such as material selection, power requirements, current carrying capacity, heat dissipation, and reliability, you can make an informed decision that meets your needs. Understanding how the power PCB’s design, layout, and quality can affect the system’s stability is essential to avoiding costly mistakes and making your device operate more efficiently.