What types of devices benefit most from using HDI PCB?
As technology advances, modern devices become smaller while their performance improves. In this context, HDI PCB plays a crucial role in enabling the design of smaller yet more powerful devices. These circuit boards allow for higher component density, optimizing the available space and improving the overall performance of devices. HDI PCB has emerged as a key technology as the demand for high-performance, compact designs and reliability increases globally. This article will explore which types of devices benefit the most from using HDI PCBs and explain in detail how this technology enhances efficiency and functionality in various devices.
Consumer Electronics: HDI PCB Helps Improve Performance and Efficiency
The rise of smartphones, tablets, wearables, and other consumer electronic products has created a growing demand for smaller, more powerful devices. The HDI PCB plays a significant role in these devices by helping designers integrate more functional components within a limited space, thereby improving operational efficiency. HDI PCBs achieve higher component density, making devices more compact and powerful.
For example, smartphones integrate high-resolution displays, processors, and sensors that rely on HDI PCB to achieve high-density interconnect designs. Using HDI PCBs, these devices can improve data transfer speeds, reduce device sizes, and extend battery life. Apple’s iPhone, for example, owes much of its compact design and high performance to using HDI PCBs, ensuring a perfect balance between size and power.
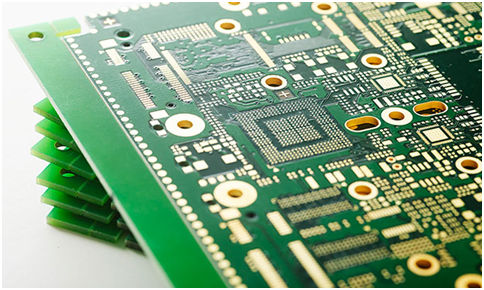
Medical Devices: Ensuring Precision and Reliability
Medical devices, which are incredibly portable and implantable, require extreme precision, trim sizes, and high reliability. HDI PCBs’ high-density designs enable complex electronic components to be integrated into compact medical devices, supporting efficient real-time data processing. The precision of medical devices directly impacts patient safety, so the stability and density of the HDI PCB are critical in these designs.
For example, implantable pacemakers and wearable health monitoring devices benefit from HDI PCBs, as they require complex circuits, miniaturization, and reliability. By using HDI PCBs, these devices are optimized in size while enhancing their stability and durability, ensuring long-term performance without failure.
Automotive Industry: Improving Safety and Efficiency
As the automotive industry evolves toward automation and electrification, HDI PCBs are becoming increasingly important in modern vehicles. From advanced driver assistance systems (ADAS) to electric vehicle (EV) battery management systems, HDI PCBs help integrate more complex systems into compact spaces. The automotive industry requires HDI PCBs to meet high-frequency signal transmission needs while ensuring extreme durability in harsh environments.
For instance, electric vehicles’ battery management system (BMS) relies on HDI PCBs to manage efficient battery charging and discharging, improving energy efficiency. In ADAS, HDI PCBs facilitate the integration of sensors, cameras, and processors, enabling real-time data processing that enhances safety and driving experience. The compact design of HDI PCBs allows these complex systems to be integrated into the limited space available in modern vehicles.
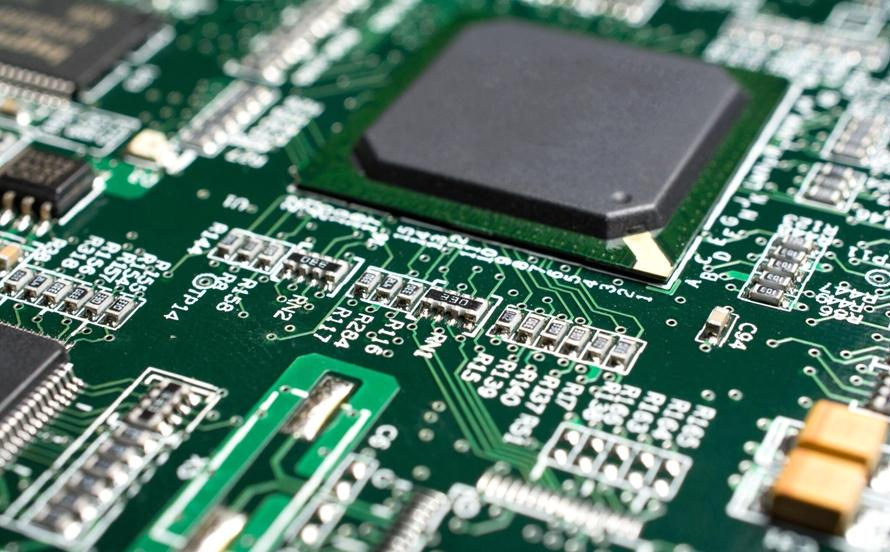
Communication Devices: Enhancing Data Transfer Speeds
Devices must handle high-speed data transfers in fields like 5G, fiber-optic, and wireless communication. HDI PCBs are an ideal choice for these high-performance communication devices due to their high-density interconnect features. HDI PCBs optimize circuit layouts and minimize signal loss, ensuring the stability and speed of data transmission, which is critical in modern communication systems.
Take 5G base stations as an example. HDI PCBs support the high-frequency signal transmission necessary for fast data transfer, ensuring data is transmitted quickly and accurately. Compared to traditional PCBs, HDI PCBs significantly reduce signal loss and interference, improving communication quality. HDI PCBs support multiple radio signals in wireless communication devices and increase the network’s overall efficiency, meeting the global demand for faster, more reliable communication networks.
Aerospace and Defense: Enhancing Durability and Performance
Aerospace and defense industries demand extreme reliability and durability from their equipment. HDI PCBs provide high-density interconnects, enabling the integration of powerful functions in lightweight devices. These devices must withstand extreme environmental conditions, such as high temperatures, pressure, vibration, and radiation, which makes their electronic systems crucial for reliable performance.
For example, HDI PCBs are commonly used in satellites and spacecraft, integrating navigation systems, communication devices, and power management systems. Their compact and dense design enables manufacturers to pack more functionality into a small space. HDI PCBs support radar, electronic warfare, and other high-performance equipment in military communication systems, ensuring the systems remain stable and precise even in combat conditions.
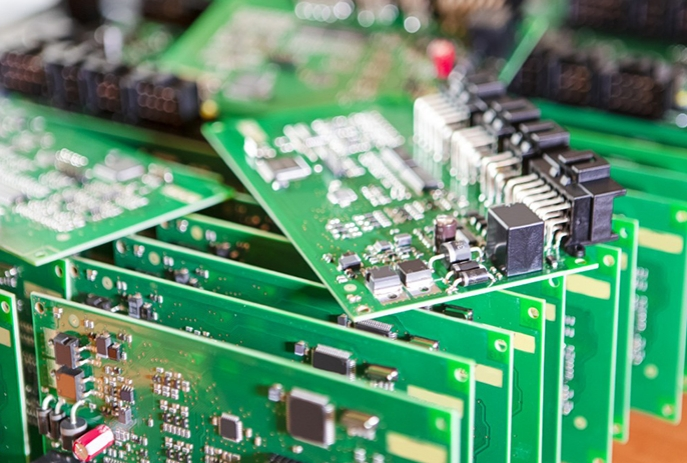
Industrial Equipment: Boosting Efficiency and Precision
Industrial automation, robotics, and control systems heavily rely on HDI PCBs to meet the growing demand for precision and high-efficiency operations. Manufacturers use HDI PCBs to integrate complex circuits into compact systems, fulfilling the needs of modern industrial devices. Whether in robotic arms on production lines or control systems in large factories, HDI PCBs offer high-performance solutions that ensure the stable operation of these systems.
For example, industrial robots require fast and accurate data processing to perform precise tasks. HDI PCBs support complex processing units in small form factors, allowing robots to perform efficiently in confined spaces. Additionally, manufacturers use HDI PCBs in the control panels of automated equipment, optimizing circuit layouts and improving energy efficiency and operational performance. The high-density interconnect design of HDI PCBs ensures that industrial devices remain compact while retaining excellent functionality.
The Future of HDI PCB: Innovation and Emerging Applications
As technology advances, the role of HDI PCBs will become even more critical. In emerging fields such as quantum computing, augmented reality (AR), and virtual reality (VR), HDI PCBs will support the development of devices that demand even higher density and performance. Quantum computing, for example, requires high-precision, high-density circuit boards, making HDI PCBs an essential technology for this next-generation field.
HDI PCBs will continue to drive the miniaturization and performance enhancements of AR and VR devices. By integrating more high-performance components into smaller spaces, HDI PCBs enable more immersive user experiences. As these emerging technologies continue to develop, HDI PCBs will provide the necessary support, becoming a cornerstone in the evolution of future electronic devices.
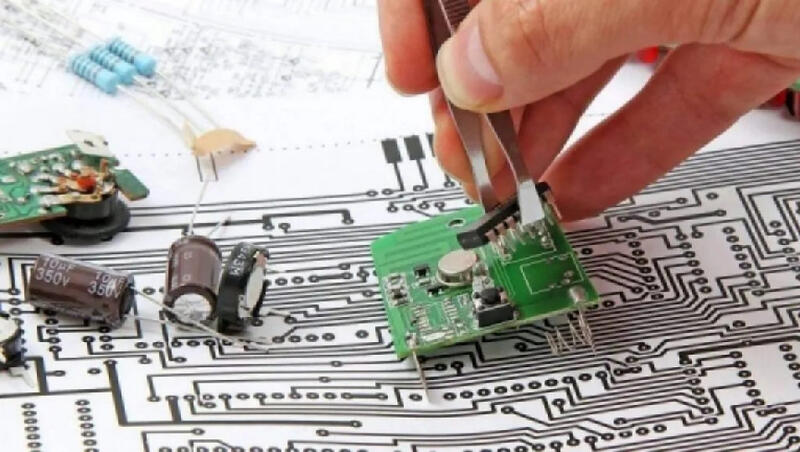
Embracing the Power of HDI PCB
As the demand for smaller, more efficient devices grows, HDI PCBs stand at the forefront of technological innovation, enabling high-density, high-performance electronic systems. Whether in consumer electronics, medical devices, automotive applications, or industrial machinery, HDI PCBs enhance devices’ performance, reliability, and miniaturization across multiple industries.