What are the typical thermal conductivity values for Heavy Copper PCB?
Thermal management is one of the most crucial aspects of designing electronic systems, especially in high-power applications where heat generation is significant. Efficient heat dissipation prevents damage to sensitive components, ensuring longer lifespans and reliable operation. Heavy Copper PCBs play a key role in this process by offering superior thermal conductivity compared to standard PCBs, making them ideal for power-hungry devices like automotive electronics, industrial machinery, and LED systems. In this article, we will focus on the thermal conductivity values typical of Heavy Copper PCBs, how these values influence their performance, and why understanding this aspect is critical when selecting the correct PCB for your applications.
Thermal conductivity of heavy copper PCB and standard PCB
Standard copper PCBs typically feature copper traces ranging from 1 oz/ft² (35 µm) to 2 oz/ft² (70 µm). These boards offer thermal conductivity of 390-420 W/mK, which suits low- to medium-power applications. However, these PCBs can’t dissipate heat efficiently in high-power systems like automotive electronics and industrial machinery. This inefficiency leads to overheating and potential damage to the components.
In contrast, heavy copper PCBs use copper traces ranging from 3 oz/ft² (105 µm) to over 10 oz/ft² (350 µm). The increased copper thickness significantly improves the PCB’s heat dissipation capacity. These PCBs handle higher currents without overheating, making them perfect for high-performance electronics. Heavy Copper PCBs ensure reliable operation even in demanding environments, allowing the safe and efficient operation of power electronics, automotive systems, and industrial machinery.
.jpg)
Typical Thermal Conductivity Values
Heavy Copper PCBs have thermal conductivity values similar to standard copper PCBs, around 390-420 W/mK. However, thicker copper traces in Heavy Copper PCBs dramatically enhance their heat dissipation capabilities. For example, a Heavy Copper PCB with 3 oz/ft² copper provides thermal conductivity similar to standard PCBs but manages heat far more effectively due to its thicker copper traces. As the copper thickness increases, the PCB’s ability to dissipate heat improves. Heavy Copper PCBs with 6 oz/ft² copper or more significantly enhance heat dissipation, making them ideal for power electronics.
Factors Affecting Thermal Conductivity
The thickness of copper traces is the most critical factor in the thermal performance of Heavy Copper PCBs, but other factors also influence overall thermal conductivity. The type of substrate material plays a significant role, as different materials have different thermal properties. FR-4 is a common choice for most applications due to its cost-effectiveness and good thermal stability. However, for more advanced applications, designers may choose ceramic substrates with better thermal conductivity to improve heat dissipation further.
Additionally, PCB design impacts thermal performance. Designers often use thermal vias to create conductive paths from the top to the bottom layer of the PCB. These vias help heat travel more efficiently through the board, reducing hotspots and improving heat transfer. Heat sinks are also commonly added to enhance heat dissipation, especially in high-power systems where rapid temperature increases occur.
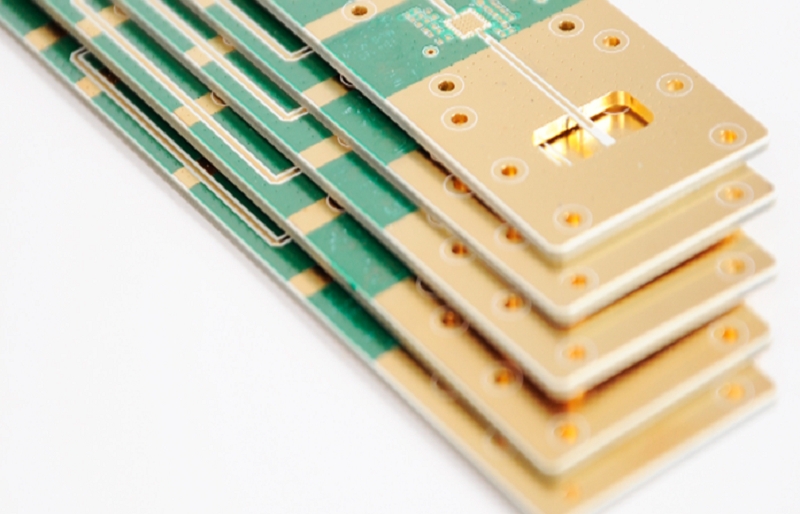
Comparing Thermal Performance in Different Applications
Heavy Copper PCBs are vital for high-power applications where efficient heat management is necessary. In automotive electronics, for instance, these PCBs control power electronics for electric motors and batteries in electric vehicles (EVs). These systems generate significant heat during operation, and Heavy Copper PCBs prevent overheating while ensuring that the components remain safe and functional. By using Heavy Copper PCBs, designers can allow the systems to operate at higher currents without risking damage. This ensures the long-term reliability and safety of the vehicle’s power systems.
Similarly, in industrial machinery, where equipment runs under heavy load conditions, Heavy Copper PCBs help maintain system efficiency. The thicker copper traces dissipate excess heat from sensitive components, reducing the risk of failure. This ensures better performance and durability while minimizing the need for additional cooling systems.
The Role of Thermal Simulation in Heavy Copper PCB Design
Thermal simulation is key in designing Heavy Copper PCBs for high-power applications. Engineers use specialized software to simulate how the PCB will behave thermally under various conditions. These simulations help them determine how the PCB will dissipate heat, identify potential hotspots, and assess how copper thickness and substrate materials affect overall heat management.
By running simulations before manufacturing, designers can make necessary adjustments to improve heat dissipation and ensure that the final PCB design meets the thermal requirements of the intended device. This predictive approach helps designers optimize the design and provides a PCB that can handle high power levels without overheating.
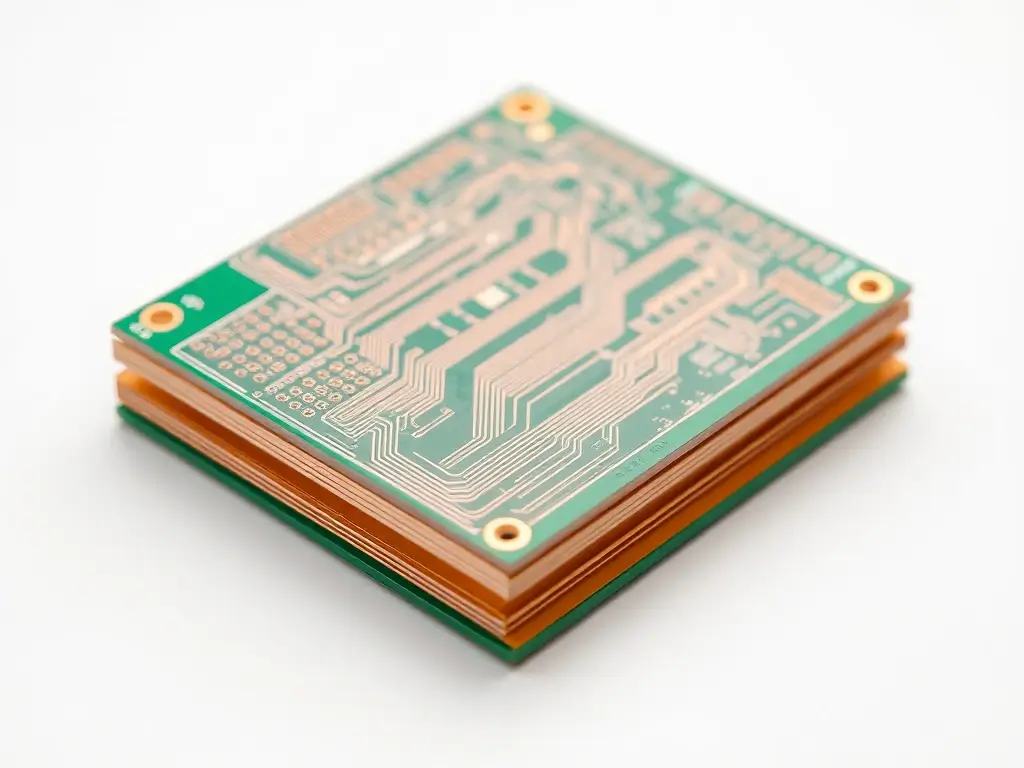
Choosing the Right Heavy Copper PCB for Your Needs
Heavy Copper PCBs are an excellent choice for applications that require superior thermal management. These PCBs provide similar thermal conductivity to standard copper boards but perform much better thanks to their thicker copper layers. This makes them ideal for high-power applications like automotive electronics, industrial machinery, and power electronics, where efficient heat dissipation is crucial. When selecting a Heavy Copper PCB, factors such as copper thickness, substrate material, and PCB design must be considered. By understanding these factors, manufacturers can choose the best PCB to meet the specific needs of their application.