Industrial Equipment: Utilizing Rigid-Flex PCB for Durability
In industrial environments, durability and reliability are non-negotiable. Traditional PCBs often fall short under constant motion and stress. Rigid-Flex PCB technology combines rigid strength with flexible adaptability, offering a more innovative, resilient solution. Ideal for control systems, robotic arms, and high-vibration machinery, Rigid-Flex PCBs ensure performance where it matters most. In this blog post, we’ll explore how Rigid-Flex PCB enhances durability in industrial equipment, the engineering behind its reliability, and why it’s becoming the go-to solution for manufacturers pushing the limits of performance and design.
Rigid-Flex PCB Strengthens Systems Against Mechanical Stress
Industrial settings often push hardware to its physical limits. Vibrations, shocks, and thermal changes are constant threats. Rigid-flex PCBs handle these conditions with ease. Integrating flexible and rigid sections allows the board to bend and twist without breaking or delaminating. This unique construction significantly extends the lifespan of internal circuitry.
Additionally, these PCBs reduce the need for traditional connectors and cables, often failure points under mechanical stress. The system becomes more stable with fewer physical joints and solder points. This advantage is especially valuable in automated manufacturing lines, where reliability directly affects productivity.
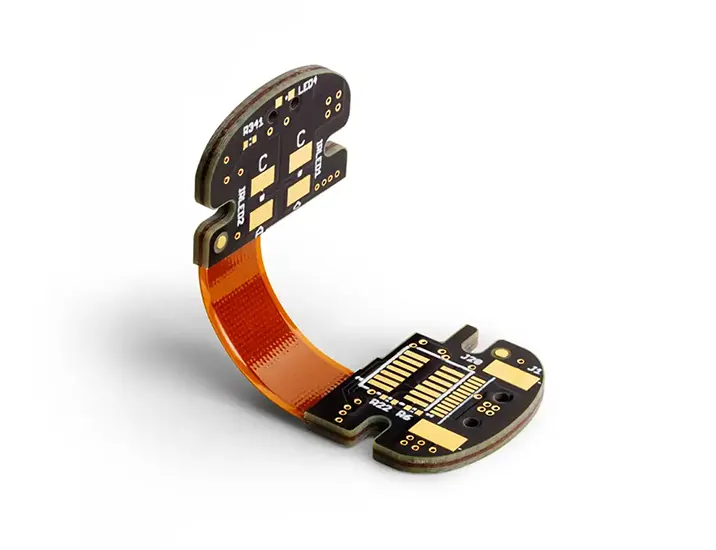
Rigid-Flex PCB Enables Compact, Space-Efficient Equipment
Space inside industrial equipment is often at a premium. Engineers must fit high-performance components into compact enclosures. Rigid-flex PCBs make this possible by enabling three-dimensional configurations. Unlike standard PCBs, which require flat mounting, Rigid-Flex boards fold and bend to fit complex geometries.
This flexibility allows designers to minimize board count and internal wiring. The result? Smaller, lighter devices with fewer points of failure. Moreover, reduced component density helps lower heat generation and improve airflow—critical factors in high-performance environments. As a bonus, fewer mechanical parts mean fewer service calls and maintenance costs.
Improved Signal Integrity and Electrical Performance
In high-speed industrial systems, signal integrity is paramount. Crosstalk, EMI, and signal loss can lead to catastrophic failures. Rigid-flex PCBs provide an excellent foundation for clean, stable signal transmission. Their layered architecture allows precise control of impedance and trace routing.
By integrating flexible interconnects, engineers can eliminate long cables that often introduce latency or interference. Moreover, reduced connector use ensures consistent electrical contact, vital for feedback systems and data-driven machinery. This leads to improved accuracy and efficiency in automated equipment, from assembly lines to CNC machinery.
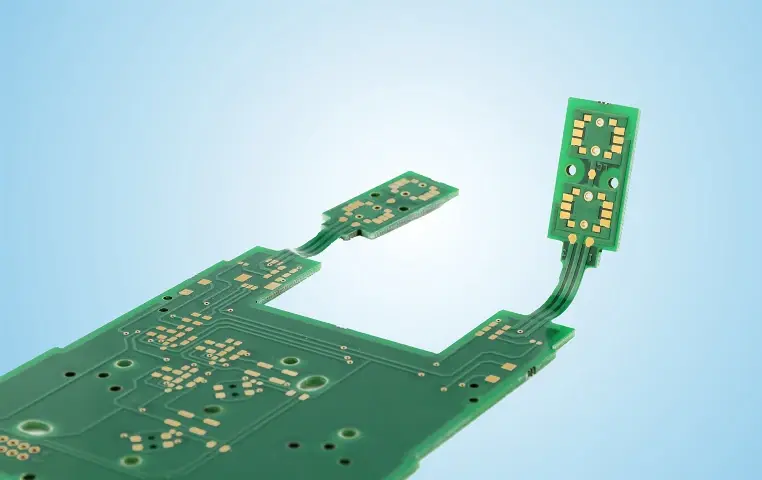
Enhanced Thermal Management Capabilities
Heat is the enemy of electronic longevity. In industrial environments, where components operate continuously, thermal management is critical. Rigid-flex PCBs can be designed with advanced thermal dissipation in mind. Their compact form reduces hot spots, while the material layering aids in efficient heat spreading.
Some manufacturers include thermal vias and embedded heat sinks in the rigid sections of the board. These additions pull heat away from sensitive components and distribute it throughout the assembly. Consequently, equipment runs cooler, fails less often, and lasts significantly longer. This performance edge translates directly into cost savings and operational efficiency.
Easier Assembly and Reduced Downtime
One of the biggest challenges in industrial electronics is efficient assembly. Rigid-flex PCBs streamline this process dramatically. Integrating multiple board functions into a single assembly reduces part counts and simplifies installation. This means faster production cycles and fewer opportunities for assembly errors.
Moreover, repair and replacement are more straightforward. Because fewer connectors and mechanical fasteners exist, technicians can service these systems more quickly. Downtime is reduced, and production lines resume operation faster in industries where every minute counts. These time savings have a significant impact on the bottom line.
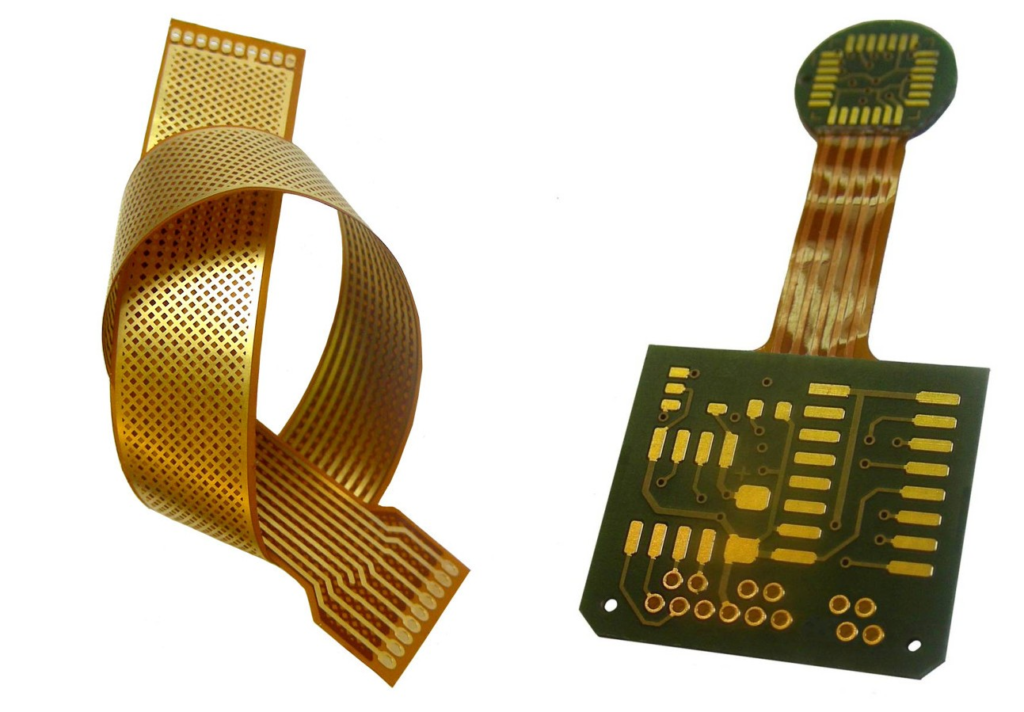
Greater Design Freedom and Customization
Industrial applications vary widely, from robotic welding arms to oil refinery sensors. Each use case demands unique specifications. Rigid-flex PCBs provide the design flexibility to meet those needs. Engineers can create custom shapes, sizes, and layer configurations that wouldn’t be feasible with traditional boards.
This adaptability makes it easier to integrate new functions without redesigning entire systems. For example, adding a new sensor or actuator can be as simple as updating a board layout rather than overhauling the housing. This modular approach accelerates innovation and reduces time-to-market for new equipment.
Reliability in Mission-Critical Operations
Industrial sectors like aerospace, energy, and manufacturing can’t afford failure. Equipment must perform consistently under pressure. Rigid-flex PCBs offer the long-term reliability needed for mission-critical applications. Their robust design resists fatigue, corrosion, and vibration damage over extended periods.
Redundancy can also be built into the circuit paths, providing backup in case of failure. In high-stakes environments, this reliability ensures safety and maintains uptime. Whether monitoring power grids or operating in hazardous conditions, these PCBs are trusted components in high-reliability systems.
Rigid-Flex PCB as the Backbone of Durable Industrial Design
Rigid-Flex PCB technology represents a pivotal shift in industrial equipment design—merging durability, flexibility, and efficiency into a single, streamlined solution. These advanced PCBs are becoming indispensable across various sectors, from heavy-duty machinery to precision robotics. Adopting Rigid-Flex PCBs isn’t merely a technical upgrade; it’s a strategic move. They help reduce maintenance costs, extend the operational life of equipment, and significantly enhance overall system performance. For manufacturers and system integrators aiming to build more resilient, future-ready systems, Rigid-Flex PCBs aren’t just the smart option—they’re the only one that truly makes sense.