Bending resistance of multilayer rigid-flex pcb
In the field of PCB, multilayer rigid-flex PCB has good flexibility and powerful function integration. This hybrid structure meets modern electronic devices’ complex spatial arrangements and enhances durability under mechanical stress. This article will give you an in-depth look at the bend resistance of multilayer rigid-flex PCBs, a key attribute that industries that require reliable physical stress seek.
Material composition and its effect on bending resistance
The bending resistance of multilayer rigid-flex PCBs depends largely on their material composition. This type of PCB usually consists of a multi-layer flexible circuit substrate attached to a rigid board.
The PI film is the core of the flexible layer in the multilayer rigid-flex PCB. PI membranes are known for their excellent thermal stability and chemical resistance, providing flexibility and durability for applications requiring frequent bending and movement. Additionally, their inherent strength and flexibility greatly increase the board’s resistance to bending, allowing it to withstand multiple bending cycles without failure. The flexural strength of multi-layer rigid-flex boards is mainly affected by the type and thickness of the material. Polyimide and thin copper layers in the flexible parts of multilayer rigid-flex PCBs enable these boards to adapt to small bending radii without affecting electrical functionality or structural integrity.
Design considerations for high bending resistance of multilayer rigid-flex pcb
Careful consideration is needed when designing multi-layer rigid-flex boards that increase bending resistance without compromising electrical integrity. We can keep them balanced and evenly distributed across the board when bending by symmetrically stacking them, and designing effective transition zones between rigid and flexible areas is crucial. Traces in flex areas can follow the direction of the bend, as traces perpendicular to the bend are more likely to break. Additionally, increasing the trace width in the bend area can reduce stress on each trace. Avoid placing pads and vias in curved areas.
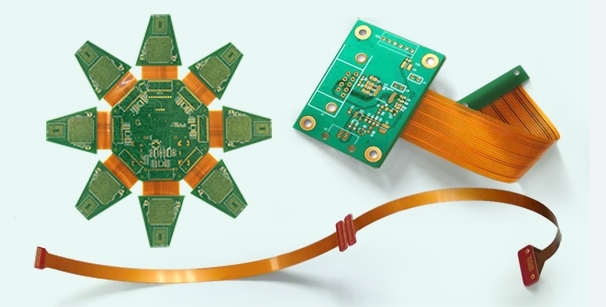
Manufacturing processes that affect bending properties
The manufacturing process of the multi-layer rigid-flex board can also affect its bending resistance. Polyimide film will be used in the flexible layer, and an adhesive will be used to bond the copper foil evenly to the flexible substrate during the lamination process. Lamination can prevent delamination, which is the main cause of bending area failure. In addition, the copper etching used to form circuit patterns must be precisely controlled to avoid under- or over-etching. Drilling vias and through-holes in multilayer rigid-flex boards requires precise alignment to prevent damage to the flexible substrate. Subsequent plating requires adequate coverage of the hole walls to ensure electrical continuity and mechanical strength. During assembly, you must take care to ensure that components and connectors in the rigid areas do not place undue stress on the flexible areas.
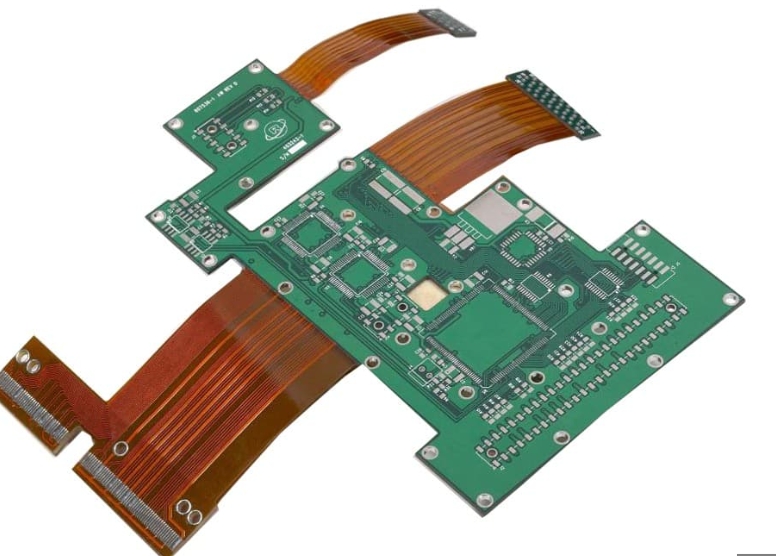
Bending performance tests and standards
Testing the flexural properties of a multilayer rigid-flex board is an important step to ensure its reliability and durability in applications. The main standards for bending performance testing include IPC-6013D, which is a performance specification and method for checking flexible and rigid-flex printed boards. The IPC-TM-650 2.4.9 standard determines circuit boards’ flexibility and ability to withstand a certain bending radius without breaking. It requires multi-layer rigid-flex boards to be wrapped around a mandrel of a specific diameter to simulate reality. Bend scenes of the world to see if conductive traces break under pressure. The IPC-TM-650 2.4.9 test evaluates the number of cycles a circuit board can withstand before failure.
Applications that rely on bending resistance
The unique properties of multilayer rigid-flex boards make them ideal for various applications in industries such as aerospace, consumer electronics, and medical devices. Smartwatches can integrate multiple rigid areas that house essential components such as microprocessors, battery terminals, and sensor modules. In contrast, flexible areas can bend around the wrist and between moving parts without failure. In wearable technology, multilayer rigid-flex boards must accommodate a variety of components while meeting ergonomic considerations.
Ultimately
As electronic devices become more integrated and physically dynamic, the bending resistance of multi-layer rigid-flex printed circuit boards will be the focus of various application manufacturers. For PCB designers and engineers, leveraging the full potential of these means they can continue to innovate in product design.