Cost considerations for manufacturing ultra low loss PCB
Ultra low loss PCBs are essential for industries requiring high speed and high-frequency applications. These PCBs provide excellent signal integrity while reducing losses, ensuring optimal performance of electronic devices. However, implementing these advanced capabilities comes with various cost factors to consider. This guide will take you through the factors affecting the ultra low loss PCB manufacturing cost.
Material selection and its impact on ultra low loss PCB cost
Material selection can determine the cost of an ultra low loss PCB and directly affect its performance and reliability. Substrate materials with low dielectric constant (Dk) and low dissipation factor (Df), such as PTFE or ceramic filler materials, are preferred for ultra-low loss applications. These materials have excellent electrical properties, including low signal attenuation and minimal energy loss, critical to maintaining high-frequency signal integrity. However, these high-performance substrate materials often cost more than the standard FR-4 materials used in traditional PCBs. The increased cost is primarily attributable to higher raw material costs, more stringent manufacturing processes, and specialized manufacturing techniques required to produce ultra-low-loss PCBs.
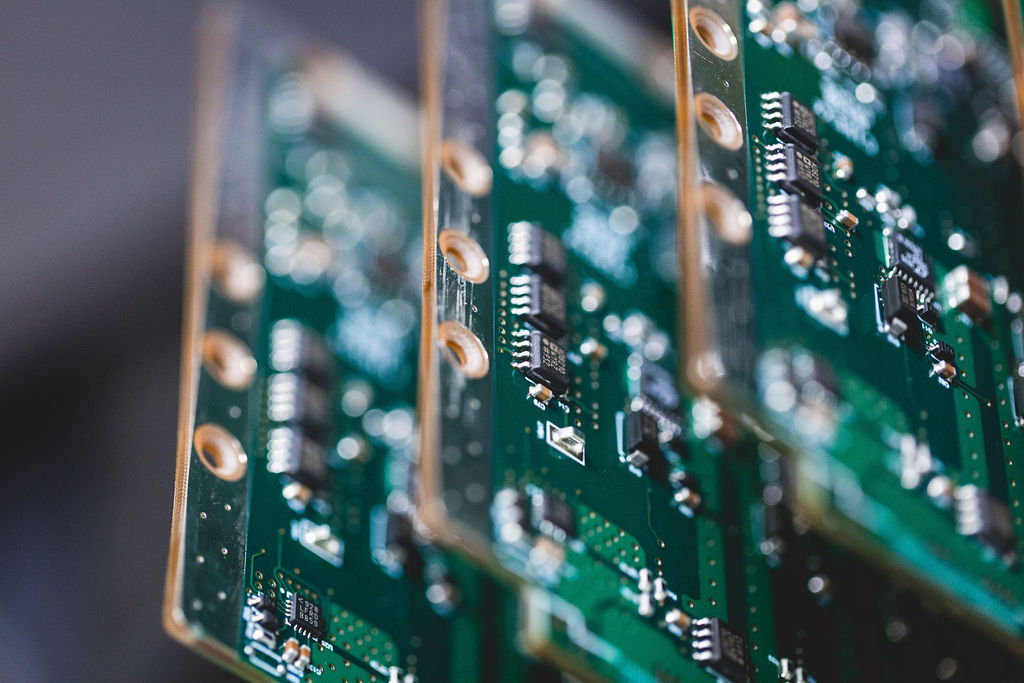
The complexity of ultra low loss PCB design and its impact on manufacturing costs
Manufacturing costs are impacted when designing ultra-low loss PCBs due to the specialized materials, complex manufacturing techniques, and strict quality control measures required to achieve high performance. The design of ultra-low-loss PCBs often involves complex layout considerations to minimize signal interference, impedance mismatch, and crosstalk. Controlled impedance routing, differential pair routing, and optimized trace geometry are critical to maintaining signal integrity and minimizing high-frequency energy loss. These complex designs require specialized CAD tools and experienced engineers, increasing overall design and development costs.
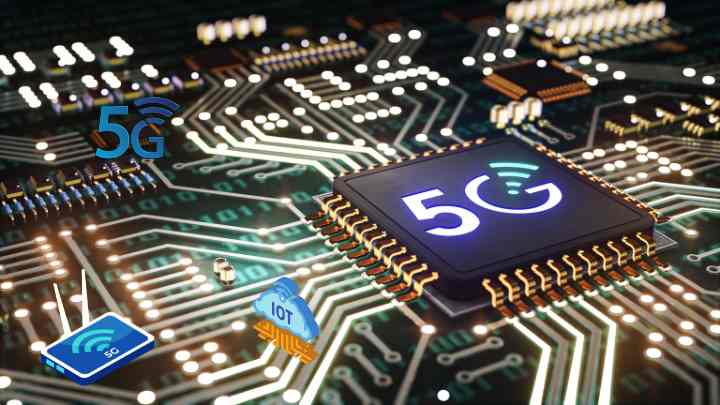
Manufacturing throughput and economies of scale
Yield is another critical factor affecting the cost of ultra low loss PCB manufacturing. Economies of scale dictate that larger production volumes spread fixed costs over more units, resulting in lower unit costs. However, due to the specialized and targeted application of ultra-low loss PCBs, they are usually produced in smaller quantities compared to standard PCBs. However, achieving economies of scale may require significant upfront investments in production equipment, tooling, and infrastructure, which may be challenging for low-volume production.
Ultra low loss PCB technology advances reduce costs
Advances in ultra low loss PCB technology are designed to reduce manufacturing costs by improving material efficiency, streamlining manufacturing processes, and increasing yields. By developing cost-effective substrate materials with enhanced electrical properties. Continuous innovation to create materials with a lower dielectric constant (Dk) and dissipation factor (Df) while maintaining high performance and reliability. These advances allow using more affordable materials without compromising signal integrity, resulting in cost savings in ultra-low-loss PCB production. Additionally, advancements in manufacturing technology reduce manufacturing costs by increasing efficiency and precision. Automated robotic assembly and laser drilling replace manual labor, reducing production time and labor costs.
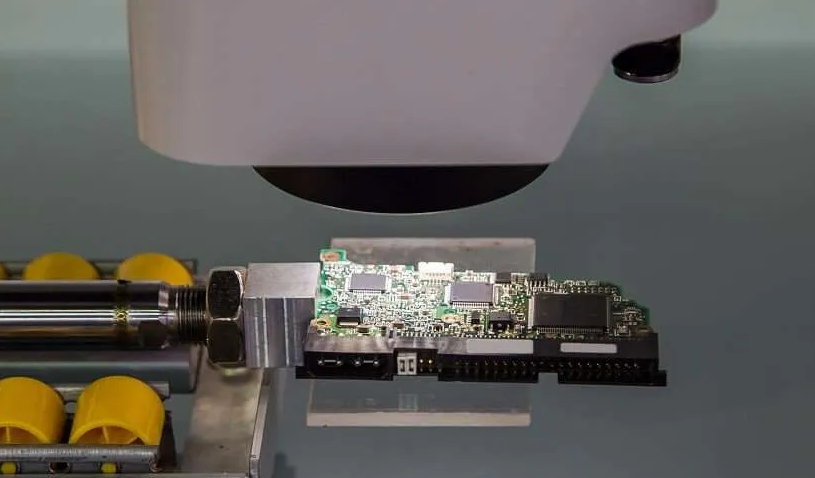
Quality control measures and their impact on manufacturing costs
Quality control measures for ultra-low loss PCBs are critical to ensuring consistent performance and reliability. However, strict quality control measures may increase the manufacturing cost of ultra-low loss PCBs. Specialized equipment and test instruments, such as impedance testers and environmental chambers, are required to conduct comprehensive quality control testing. Skilled labor and expertise are also needed to interpret test results and resolve any issues during production accurately. Identifying and correcting defects early in production is critical to minimizing waste and ensuring that the finished PCB meets quality standards. However, these additional steps increase production costs and impact overall manufacturing efficiency.
Total cost of ownership and long-term considerations
When evaluating the cost of manufacturing ultra-low-loss PCBs, we must consider the total cost of ownership (TCO) over the entire product life cycle. While upfront manufacturing costs are high, reliability, performance, and lifecycle durability impact TCO. Investing in high-quality materials, advanced manufacturing processes, and strict quality control measures may result in a slightly higher initial cost. Still, it can generate significant long-term savings through reduced maintenance, downtime, and replacement expenses. By taking a holistic approach to considering costs, businesses can make informed decisions that optimize short-term spend and long-term value.