How are HDI PCB used in medical devices and wearables?
The demand for smaller, more efficient, and higher-performing devices has surged as technology evolves, especially in the medical and wearable technology sectors. Central to this evolution is the ability to pack more functionality into smaller spaces without compromising performance or reliability. HDI PCB has become integral to meeting these demands, providing a solution to miniaturization while enhancing the functionality and performance of electronic devices. In this article, we will explore how HDI PCB has been used in medical devices and wearables and highlight their role in driving the growth of these industries.
HDI PCB is Essential for Medical Devices
In medical devices, miniaturization is not just a trend; it’s a necessity. As the healthcare industry moves toward more advanced, portable, and minimally invasive solutions, smaller, more efficient devices are required. HDI PCB is pivotal in enabling this transformation by providing a compact yet highly functional platform for complex medical electronics.
For example, portable diagnostic tools, such as heart monitors or glucose sensors, must be lightweight and small so patients can easily carry them. HDI PCBs enable this by integrating more circuits into a small footprint while maintaining the necessary performance standards. This level of miniaturization is critical in ensuring that medical devices can function effectively in real-world scenarios without taking up excessive space or requiring bulky components.
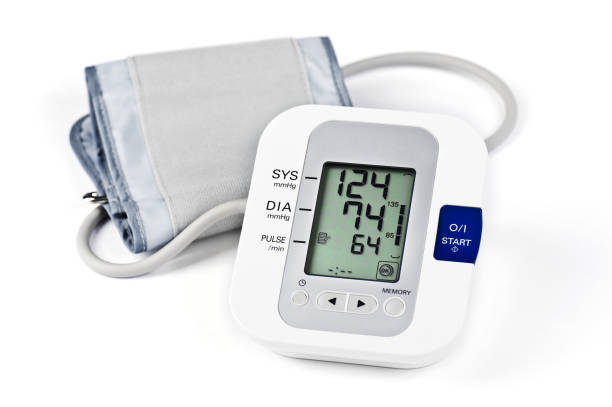
Enhancing Reliability and Performance in Medical Devices
Due to the potential life-or-death consequences of their failure, medical devices must meet the highest standards of reliability and performance. This is where HDI PCB comes into play. The technology’s ability to create high-density circuit boards with greater precision ensures that devices remain reliable even in challenging environments.
HDI PCBs allow for more advanced features, such as higher-speed data transmission and increased functionality, without increasing the device’s size. For medical applications, this means that devices such as pacemakers, defibrillators, and wearable glucose monitors can operate efficiently, delivering critical real-time data to patients and doctors alike. The compactness and density of HDI designs contribute to reliability and performance, enabling medical devices to perform vital functions over extended periods, often without requiring maintenance or replacement.
The Role of HDI PCB in Wearable Technology
Wearable technology has become integral to modern healthcare and fitness, with devices such as smartwatches, fitness trackers, and health-monitoring sensors gaining popularity. These devices rely heavily on HDI PCBs to achieve the miniaturization, efficiency, and high performance required in today’s fast-paced, health-conscious world.
Wearable devices must be lightweight and comfortable while packing advanced features such as heart rate monitoring, GPS, step tracking, and ECG readings. HDI PCBs enable this by providing a compact design that houses all necessary components, such as sensors, batteries, and communication modules, in a minimal space. The small size of HDI PCBs allows for better integration of these components into sleek, aesthetically pleasing wearables, ensuring that users can wear them comfortably throughout the day while benefiting from accurate data and real-time insights.
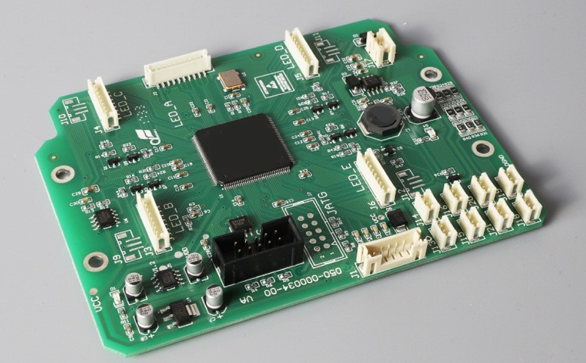
Advanced Functionality with Multi-layer Designs
One of the significant advantages of HDI PCBs is their ability to incorporate multi-layer designs, which is particularly beneficial in medical and wearable devices. By using multiple layers, HDI PCBs can increase component density and support more complex circuits without taking up additional space. This results in more advanced functionality within smaller devices.
In medical devices, multi-layer HDI PCBs allow for integrating sensors, power management circuits, signal processing units, and wireless communication modules in one compact form factor. This multi-layer capability supports the inclusion of advanced diagnostic tools, such as ECG or EEG sensors, that require high-speed data transmission and processing in a small, wearable device. For wearables, this means that devices can offer advanced features while remaining lightweight and comfortable for the user.
Cost Efficiency and Production Scalability
In addition to offering high-density designs and advanced functionality, HDI PCBs are also cost-effective, particularly in mass production. Cost efficiency is a critical factor for both medical devices and wearables. HDI PCBs are manufactured using advanced techniques for greater production scalability, ensuring that devices can be produced competitively without sacrificing quality.
The scalability of HDI PCB production allows manufacturers to meet the growing demand for medical and wearable devices while keeping costs under control. This is particularly important in markets where mass production is necessary to meet consumer needs, such as the wearable fitness tracker industry, which sells millions of units annually. By using HDI PCBs, manufacturers can optimize the production process, reduce waste, and lower costs, making these devices more accessible to a broader range of consumers.
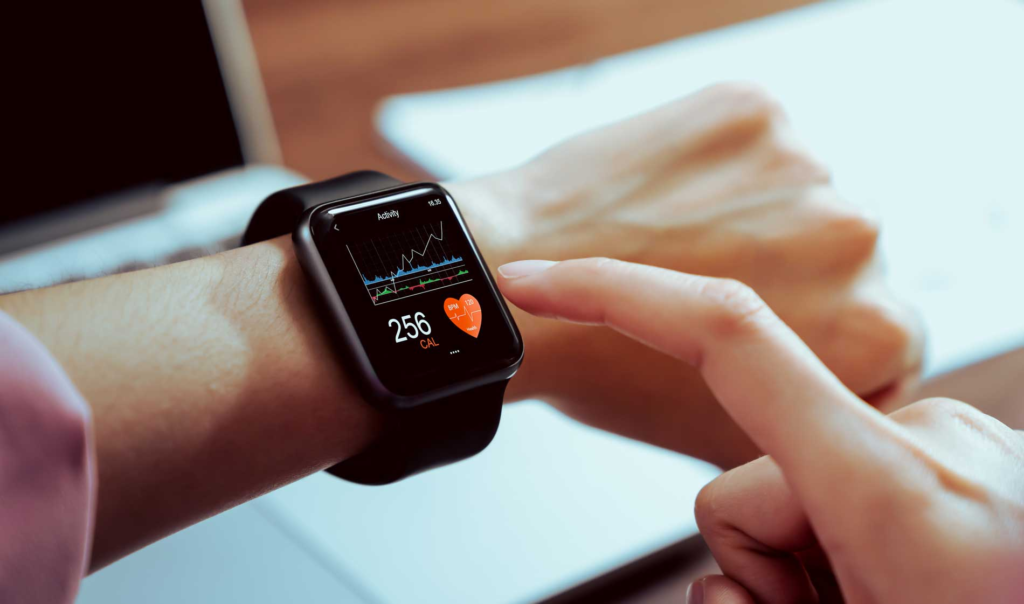
Design Flexibility for Custom Medical Applications
Another significant advantage of HDI PCBs is their design flexibility, which is especially beneficial in the medical field. Medical devices often require customization to meet specific patient needs or regulatory standards. Designers can design HDI PCBs to fit a variety of shapes, sizes, and functions, making them ideal for applications ranging from hearing aids to prosthetics.
For example, custom HDI PCBs can be used to design implantable devices such as cochlear implants or pacemakers. These devices must meet strict size, power, and performance requirements, all while ensuring that they remain safe and effective for long-term use in the human body. The ability to design HDI PCBs with precise configurations allows manufacturers to create tailored solutions for a wide range of medical applications, providing patients with life-saving devices that are small, reliable, and effective.
The Future of HDI PCBs in Healthcare and Wearables
As the medical and wearable technology industries evolve, the demand for smaller, more efficient, and more powerful devices will only increase. HDI PCBs will continue to play a key role in enabling these advancements, as they offer the necessary miniaturization, functionality, and reliability required for the next generation of medical devices and wearables.
We can expect even more integration of advanced technologies such as 5G connectivity, AI-driven health monitoring, and advanced sensors within medical and wearable devices. HDI PCBs will be at the forefront of these innovations, allowing manufacturers to create devices that push the boundaries of what is possible in healthcare and personal wellness. With continuous advancements in PCB manufacturing technologies, we can expect even greater design flexibility, improved performance, and lower costs, making these life-changing devices more accessible to people worldwide.
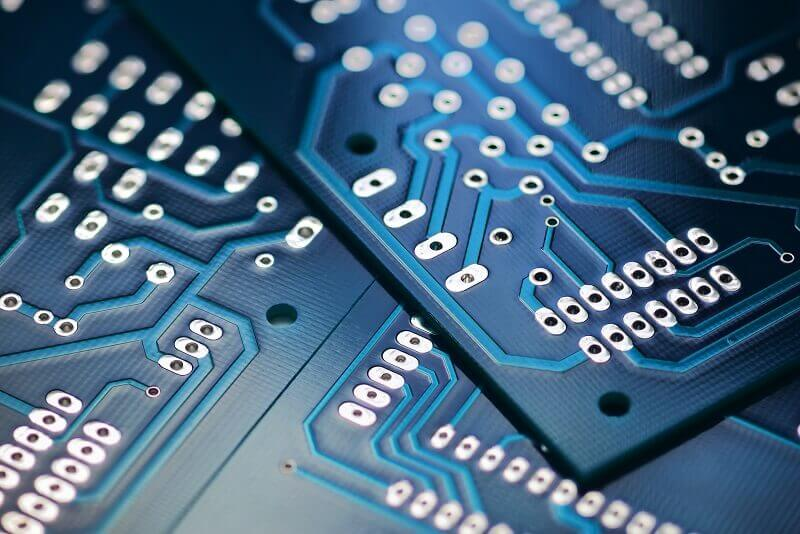
The Essential Role of HDI PCB in Modern Healthcare and Wearables
HDI PCBs are crucial enablers of innovation in medical devices and wearable technologies. Their ability to integrate more components into smaller spaces while maintaining performance and reliability has revolutionized how devices are designed and used in healthcare and fitness. From compact heart monitors to advanced fitness trackers, HDI PCBs enable the next generation of medical and wearable technology, driving efficiency, miniaturization, and improved user experiences.