How can consistency be ensured in Low loss PCB manufacturing?
For low loss PCB manufacturing, any customer requires post-production consistency. This is the key to producing high-quality products. This guide will share how to ensure post-production consistency when manufacturing low-loss PCBs, including using reliable and sturdy materials, strict process control, advanced equipment technology, adopting strict quality assurance protocols, etc.
Choose strong materials for low-loss PCB manufacturing.
Materials with low Dk and Df values are our first choice when doing low-loss PCB manufacturing, as this helps reduce signal distortion and attenuation, ensuring high-speed and high-frequency performance. In addition, we will consider the various environmental stresses that the device may endure during operation, including factors such as temperature fluctuations, mechanical shock, and vibration. Therefore, materials with excellent mechanical properties, such as high tensile strength and resistance to warping or delamination, are also selected, which can ensure that low-loss PCBs maintain structural integrity when used.
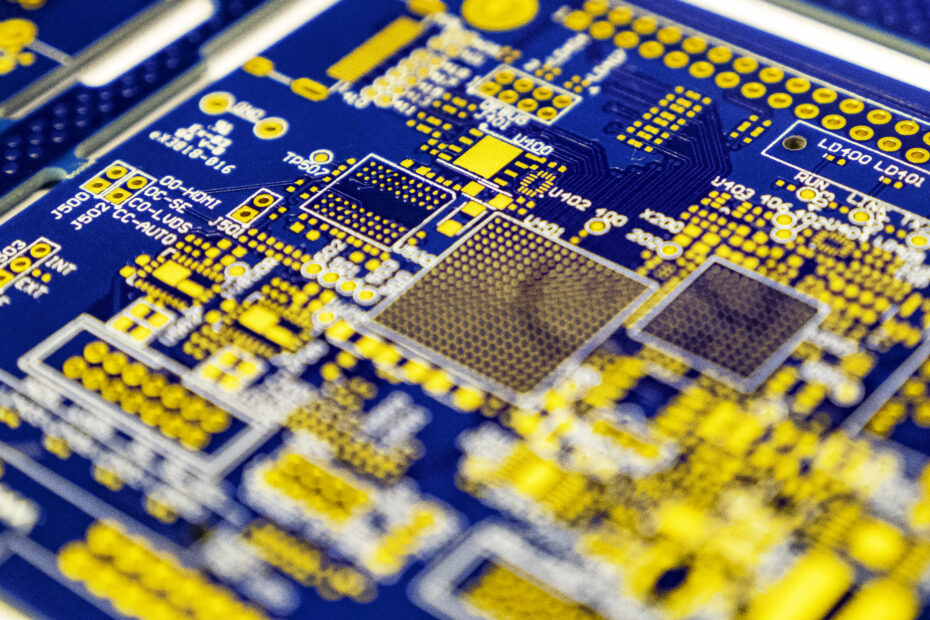
Low-loss PCB manufacturing follows strict process controls!
Our low-loss PCB manufacturing process precisely controls material properties and dimensions and maintains tight tolerances during material preparation, lamination, and pressing. A work standards manual will be developed to require employees to conduct production according to the standards in the manual to ensure the consistency of substrate thickness, copper foil thickness, and dielectric properties on low-loss PCB panels. We tightly control the etching, drilling, and plating processes throughout manufacturing to ensure precise pattern transfer, hole alignment, and copper deposition. We utilize advanced imaging and exposure techniques to achieve high precision and repeatability of fine lines.
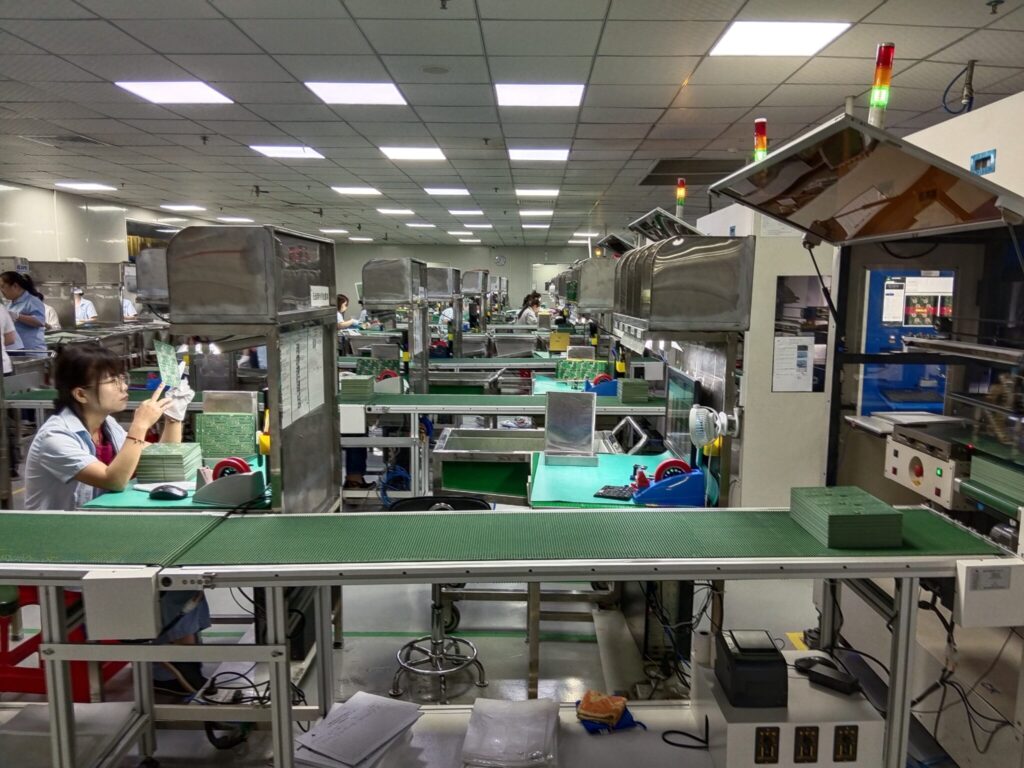
Use advanced equipment and technology!
In substrate material preparation, we use precision cutting machines with laser-guided cutting technology to ensure precise cutting of substrates such as PTFE (polytetrafluoroethylene) and high-frequency laminates. We also utilize advanced automated material handling systems to simplify the handling and processing of substrate materials, reducing manual intervention and the risk of contamination or damage. In addition to manufacturing equipment, we employ automated optical inspection (AOI) systems to detect defects such as solder bridges, missing components, and misalignments to ensure compliance with quality standards and specifications. Automated conveyors, robotic loaders, and material feed systems ensure smooth and efficient material flow throughout our factory.
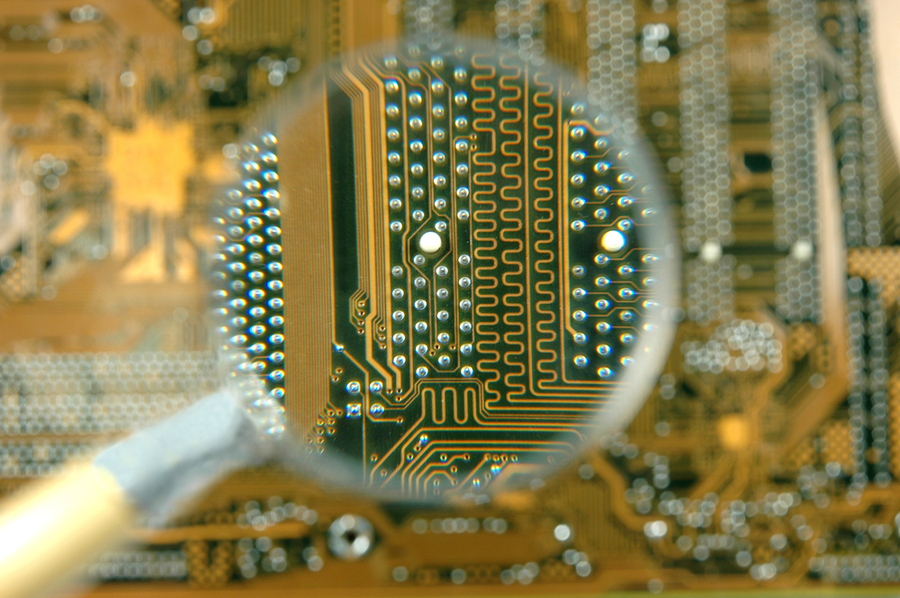
Conduct strict quality assurance protocols!
Regarding quality assurance in low-loss PCB manufacturing, we establish strict quality control checkpoints at every production stage. These checkpoints include inspecting and testing materials, substrates, and finished PCBs to identify deviations from design specifications or manufacturing standards. Our suppliers are also subject to a rigorous evaluation and qualification process, including material testing, certification, and traceability requirements. This ensures the consistency and reliability of substrate materials, laminates, copper foil, and other manufacturing products.
Communicate with customers
When manufacturing low-loss PCBs, we will also communicate with customers, the one hand, to determine the manufacturing progress, and on the other hand to make timely adjustments and scope when encountering problems. When you have any questions, we can provide after-sales service for repair and rework. Suppose you have any quality issues with the product. In that case, you can communicate with us through the contact information on the website to ensure that the products produced are of reliable quality.
Ultimately
When we manufacture low-loss PCBs, we will follow a strict material selection process, control strict process controls, and use advanced equipment and technology to ensure that each batch of your low-loss PCBs can meet the most demanding requirements.