How do rigid-flex PCB contribute to lightweight designs?
In today’s fast-paced technological world, industries are constantly pushing the boundaries of innovation. One area where this innovation is particularly crucial is in the design of electronic devices. As the demand for smaller, lighter, and more efficient devices grows, the emergence of rigid-flex PCBs, a hybrid of rigid and flexible printed circuit boards, has sparked a wave of inspiration and intrigue. These PCBs can integrate complex electronic systems into compact, lightweight structures, revolutionizing design. This article will delve into how rigid-flex PCBs can contribute to lightweight design, making them ideal for industries prioritizing portability, durability, and efficiency.
Introduction and Working Principles of Rigid-Flex PCB
A Rigid-flex PCB is a printed circuit board that integrates rigid and flexible substrates into a single board. This hybrid design combines strong, rigid areas for components that require stability with flexible sections that can bend and conform to specific shapes. Combining the best of both worlds makes rigid-flex PCBs compact and durable while minimizing the final product’s weight.
In addition, rigid-flex PCBs can reduce the need for multiple separate circuit boards, connectors, and cables, significantly reducing the device’s overall weight. Reducing the number of components not only reduces weight but also simplifies the manufacturing process, ultimately helping to improve design efficiency.
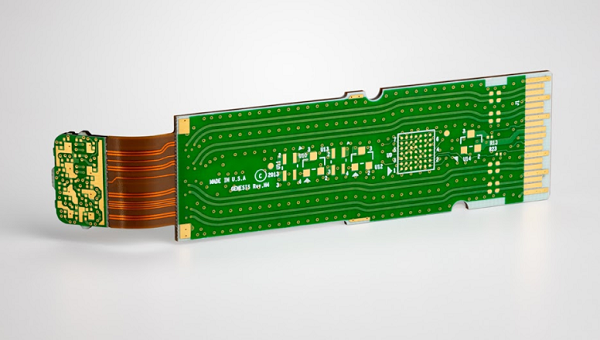
The Benefits of Lightweight Designs in Modern Electronics
The trend in the modern electronics market is clear: smaller, lighter, and more portable devices are in high demand. Whether smartphones, wearable technology, or medical devices, consumers expect high performance from products that are easy to carry and use.
Rigid-flex PCBs play a crucial role in achieving lightweight designs in electronic devices. For instance, in smartphones, tablets, and wearables, manufacturers must balance performance with portability. By integrating rigid-flex PCBs into their products, manufacturers can eliminate the need for bulky connectors, wires, and other components that add unnecessary weight. This reduction in weight not only enhances the user experience but also opens up possibilities for more innovative product designs.
As a result, devices with rigid-flex PCBs are often thinner and lighter than their traditional counterparts. This enhances the user experience and opens up possibilities for more innovative product designs. Additionally, the lightweight nature of rigid-flex PCBs enables the creation of more energy-efficient devices, as they often require less power to operate.
Rigid-Flex PCB in Wearables
Wearable technology is one of the fastest-growing sectors in the electronics industry. Smartwatches, fitness trackers, and medical monitoring devices are all examples of products where size and weight are critical factors. A rigid-flex PCB is ideal for wearable applications because it allows manufacturers to reduce the device’s size and weight while maintaining functionality.
By utilizing a rigid-flex PCB, manufacturers can place components in compact, curved, or flexible areas, allowing the device to maintain its slim profile and lightweight design. The flexible nature of the PCB also makes it easier to integrate into complex shapes, such as the slight curves of a wristband or the slim profile of a smartwatch. Furthermore, wearables require high reliability and durability, especially in medical applications. Rigid-flex PCBs offer excellent shock resistance and can withstand the physical stresses of daily wear, making them a perfect fit for these types of devices. Their lightweight yet durable design ensures that the end product remains functional and long-lasting.
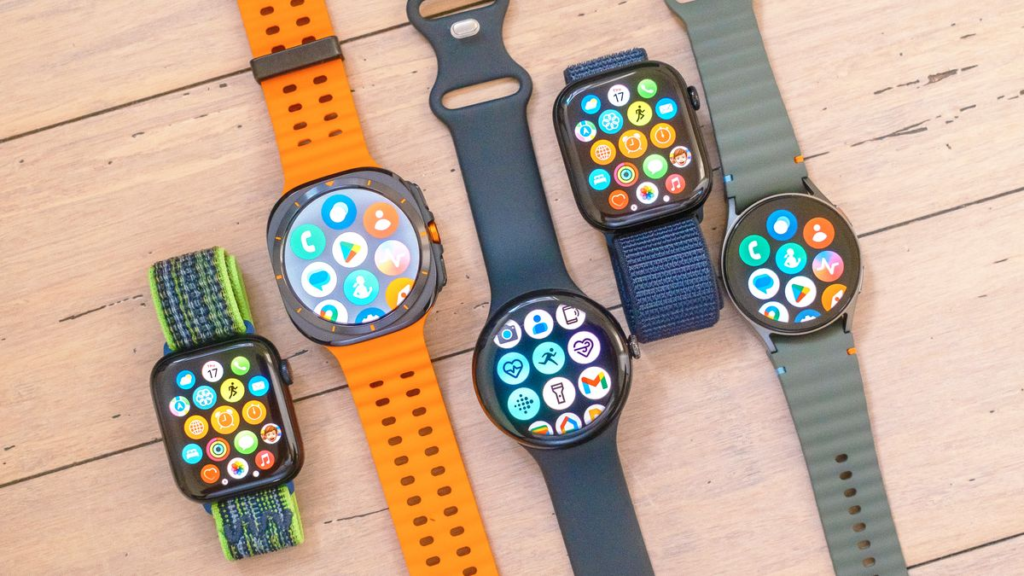
Applications in the Automotive Industry
The automotive industry is another sector that has seen significant benefits from rigid-flex PCBs. As manufacturers continue to develop more efficient and lightweight vehicles, reducing the weight of the electronic components plays a crucial role in improving overall performance and fuel efficiency.
Manufacturers can significantly reduce the weight of these components by incorporating rigid-flex PCBs into automotive applications, such as navigation systems, sensors, and infotainment systems. This weight reduction helps improve the vehicle’s overall energy efficiency and performance. Moreover, rigid-flex PCBs are well-suited for the automotive environment, where durability is key. These PCBs can withstand extreme temperatures, vibrations, and shocks, ensuring reliable operation in the harsh conditions of the automotive industry. Their lightweight nature allows automotive manufacturers to incorporate more advanced technologies without adding excessive weight to the vehicle.
Helps improve manufacturing efficiency and design flexibility
In addition to contributing to lightweight designs, rigid-flex PCBs also offer significant advantages in terms of manufacturing efficiency and design flexibility. Combining rigid and flexible areas on a single board reduces the need for multiple components, connectors, and wiring, making the overall design process simpler and more streamlined.
Manufacturers can design rigid-flex PCBs to fit specific shapes and sizes, allowing for greater flexibility in product design. This flexibility enables designers to create more compact and innovative products, essential in industries where space is at a premium. Additionally, the reduced number of components and connectors means that assembly time is shorter, and there is less risk of errors during manufacturing. This not only helps reduce production costs but also improves the overall quality of the product.
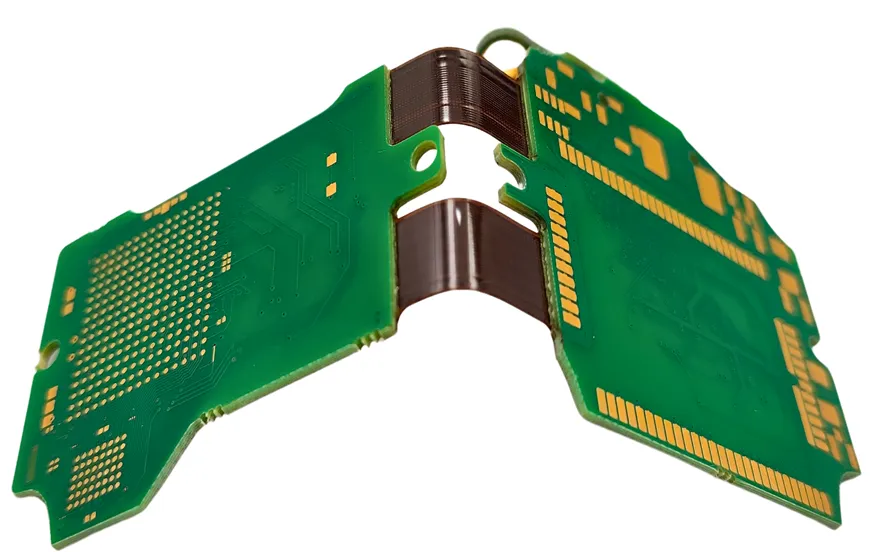
Environmental Benefits of Lightweight Design
As industries worldwide focus on sustainability, rigid-flex PCBs play a significant role in contributing to the environmental goals of reducing material waste and energy consumption. Their lightweight nature helps reduce the environmental impact of products by requiring fewer raw materials to produce. This responsibility and environmental consciousness are key factors driving the adoption of rigid-flex PCBs in the industry.
In many cases, weight reduction also translates to improved energy efficiency. For example, lighter components in portable devices like smartphones and laptops contribute to better battery life. This can lead to a longer lifespan for the product, reducing the need for frequent replacements and, in turn, decreasing e-waste.
Furthermore, rigid-flex PCBs can be manufactured using eco-friendly materials, contributing to their sustainability. As companies look for ways to reduce their carbon footprint, rigid-flex PCBs offer a way to build high-performance, lightweight products with a minimal environmental impact.
Embracing the Future of Lightweight Designs with Rigid-Flex PCB
The benefits of rigid-flex PCBs extend beyond weight reduction; they also provide enhanced durability, design flexibility, and manufacturing efficiency. As industry demand for lighter, more efficient, and compact electronic devices grows, rigid-flex PCBs are quickly becoming essential to modern design. With their ability to streamline production and facilitate more sustainable products, rigid-flex PCBs offer a promising solution for industries looking to embrace the future of lightweight designs. This future is one of optimism and forward-thinking, where rigid-flex PCBs play a central role in a rapidly evolving technology landscape.