How to Avoid Thermal Fatigue on 2 layer heavy copper PCB?
Thermal fatigue is a critical issue in electronic devices using 2 layer heavy copper PCB, affecting PCB performance and longevity. Preventing thermal fatigue is critical for those who manufacture these PCBs. This guide will comprehensively introduce the avoidance of thermal fatigue in 2 layer heavy copper PCBs, highlighting design considerations, material selection, manufacturing processes, and more.
Thermal Fatigue of 2 layer heavy Copper PCB
Thermal fatigue refers to the progressive and irreversible damage that occurs in materials due to cyclic thermal stress. In 2-layer thick copper PCBs, thermal fatigue can cause the board to crack, delaminate, and ultimately fail. These problems arise because the material repeatedly expands and contracts at fluctuating temperatures, which is common in high-power and high-frequency applications. While great for handling high current loads and thermal management, thick copper layers can exacerbate thermal stress if not managed properly.
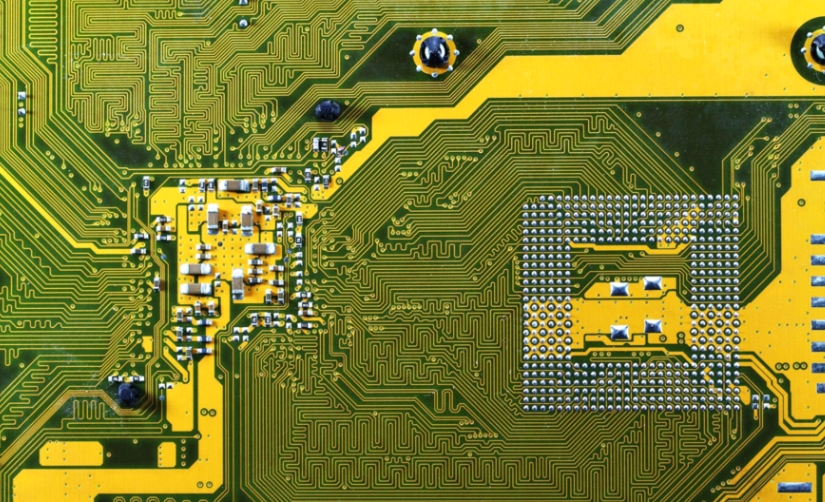
Design Considerations for 2 layer heavy copper PCB
The design phase is critical to preventing thermal fatigue. One key consideration is ensuring that thermal stress is evenly distributed on the 2 layer heavy copper PCB. This can be accomplished by optimizing the layout of components and copper traces, placing thermally sensitive components away from high-power areas, and using thermal vias to promote efficient heat dissipation.
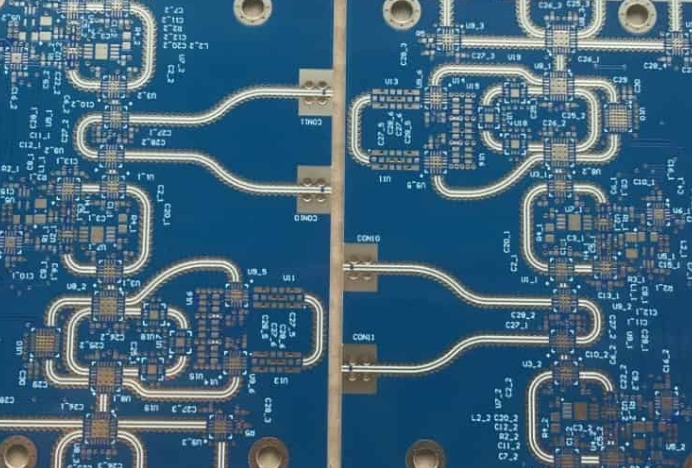
Another important design strategy is minimizing thermal gradients. This involves PCB design, which should keep temperature changes across the board to a minimum. Thermal gradients can cause differences in expansion and contraction, leading to mechanical stress and fatigue. Using a symmetrical copper layout and ensuring balanced heat distribution are effective ways to mitigate these issues. Additionally, incorporating heat sinks into the PCB design can help reduce stress on solder joints and vias.
Material Selection
Choosing the right materials is another critical aspect of preventing thermal fatigue. For 2 layer heavy copper PCBs, the choice of substrate, copper thickness, and solder mask material can significantly affect thermal performance.
High Tg laminates are particularly effective at enhancing thermal stability. These materials can withstand higher temperatures without degradation, making them ideal for heavy copper applications. Polyimide and PTFE laminates are also popular choices for 2 layer heavy copper PCBs due to their excellent thermal and mechanical properties.
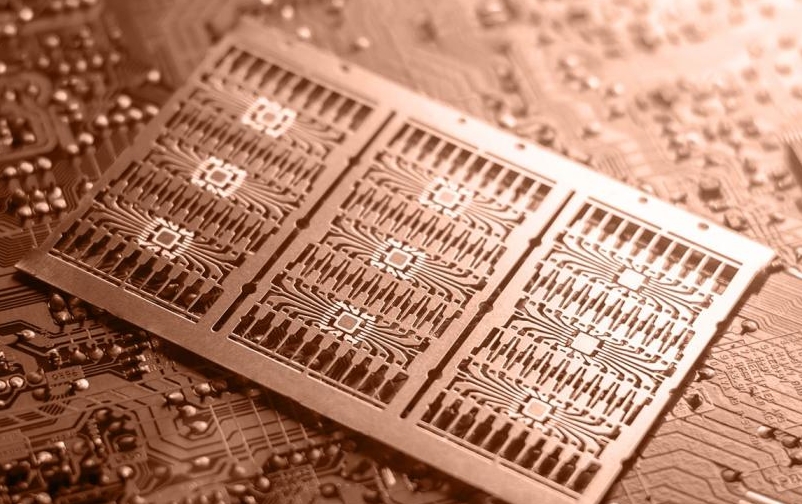
The thickness of the copper layer is also critical. While 2 layer heavy copper PCBs typically have 2 oz/sq ft to 20 oz/sq ft of copper layers, it is important to balance the advantages of thicker copper with the potential for increased thermal stress. Therefore, combining thick and thin copper layers can provide the necessary current carrying capacity. Finally, choosing a solder mask with high thermal conductivity can help dissipate heat more efficiently and reduce the risk of thermal fatigue.
The manufacturing process of 2 layer heavy copper PCB
The manufacturing process of a 2 layer heavy copper PCB involves multiple steps that can affect the board’s thermal performance. A key process is the lamination of the copper layers. Correct lamination ensures strong adhesion between the copper and the substrate, thereby reducing the risk of delamination under thermal cycling. So, using high-quality adhesives and maintaining optimal lamination temperatures are key factors in achieving a strong laminate.
Another important aspect is the etching process. Precise etching helps create clean, accurate copper traces. Therefore, it is important to use advanced etching techniques and conduct thorough inspections to ensure the integrity of the copper layer. Additionally, the soldering process affects thermal fatigue, and using solder with an appropriate melting point and ensuring proper solder joint formation can enhance the thermal stability of the PCB.
Advanced technology to enhance thermal reliability
In addition to standard practices, advanced techniques can further enhance the thermal reliability of 2-layer thick copper PCBs. One such technique is to use embedded cooling vents. These vias provide a direct thermal path from the heat-generating component to the heat sink or heat sink, thereby enhancing heat dissipation and reducing thermal gradients.
Another advanced technique is the use of thermal simulation software. These tools can model the thermal behavior of PCBs under different operating conditions, allowing designers to optimize the layout and materials for maximum thermal performance. In addition, advanced coating technologies can provide additional thermal fatigue protection.
Achieve long-term reliability
Preventing thermal fatigue in 2-layer thick copper PCBs requires a comprehensive approach that includes design, material selection, manufacturing processes, and best practices. Manufacturers can improve PCB thermal performance and reliability by understanding the root causes of thermal fatigue mentioned in the guidance and implementing effective strategies.