How to reduce costs when customizing aluminum PCB?
Aluminum PCB is a critical PCB component in various electronic applications due to its excellent thermal management properties and durability. However, the costs associated with custom aluminum PCBs can be high for some manufacturers. So, it’s crucial to know how to reduce the associated factors for businesses looking to optimize their budgets without compromising quality. In this guide, we share with you effective strategies for reducing costs when customizing aluminum PCBs.
Aluminum PCB Cost Structure
Aluminum PCB cost structure usually includes materials, manufacturing process, design complexity, testing, etc. The base material of aluminum PCB consists of the aluminum substrate, a dielectric layer, and a copper layer. The type and quality of these materials significantly affect the overall cost. Manufacturing processes such as drilling, etching, and welding require specialized equipment and expertise, adding to costs. Additionally, designs with multiple layers or complex patterns require advanced manufacturing techniques and additional labor, further increasing costs. Finally, comprehensive testing and quality assurance are critical to ensuring PCB reliability and performance and also add to overall costs.
Choosing Cost-Effective Materials for Aluminum PCBs
Material selection is one of the most important factors affecting the cost of aluminum PCBs, and the aluminum substrate is available in various grades and thicknesses. Although high-grade aluminum has good thermal conductivity and mechanical strength, it is not necessary to use such high-grade specifications for applications that do not require such strict specifications. So consider using a lower grade of aluminum that will still meet your thermal management needs but at a lower cost.
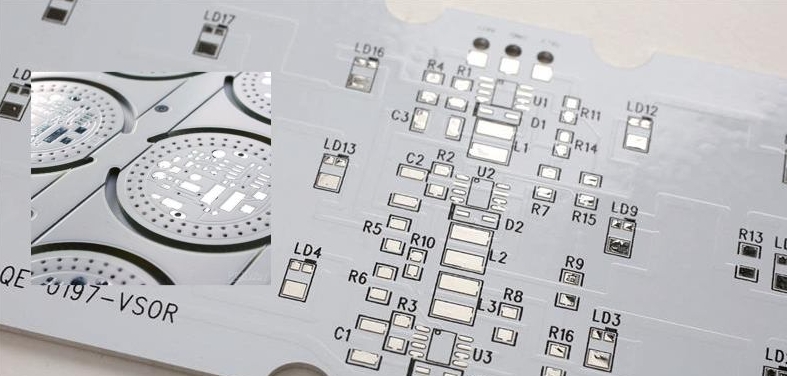
The dielectric layer, which provides electrical insulation between the aluminum substrate and the copper layer, is another area where cost savings can be achieved. Finally, consider the copper layer. While thicker copper layers can handle higher current loads, they also increase cost. Analyze your current requirements and select a copper thickness that meets your needs without incurring unnecessary expense.
Simplify design to reduce aluminum PCB customization costs
Design complexity is one of the major factors in aluminum PCB customization costs, and simplifying the design can lead to significant savings in manufacturing and testing costs.
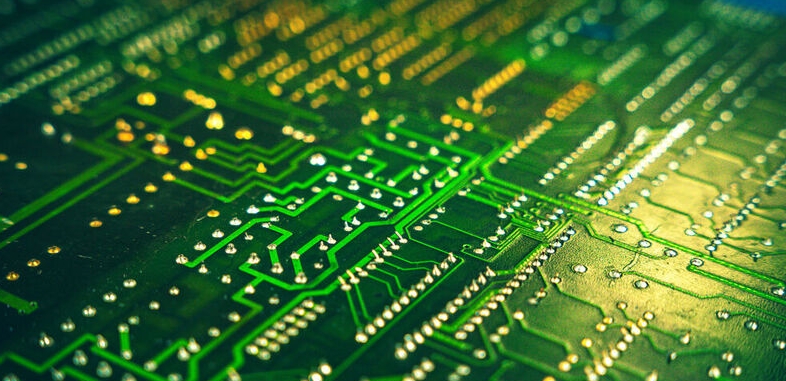
Multi-layer PCBs are more expensive to manufacture than single- or double-layer PCBs, and you can determine whether your product application can be effectively implemented with fewer layers, thereby reducing material and processing costs. Reducing PCB size reduces material costs and increases manufacturing efficiency. Using standard components instead of custom or rare parts can reduce costs. Complex trace patterns require more precise manufacturing techniques and increase the risk of defects. Simplify trace patterns as much as possible to maintain necessary electrical performance while reducing manufacturing complexity.
Optimize manufacturing process
The efficiency of the manufacturing process is critical to reducing aluminum PCB customization costs. Work with PCB manufacturers to identify and eliminate bottlenecks in the production process. Streamlining workflows can shorten delivery times and reduce labor costs, resulting in overall cost savings. Automation can be used to increase efficiency and reduce labor costs. Additionally, defects and rework can significantly increase PCB production costs. Implementing strict quality control measures throughout manufacturing helps identify and resolve problems early, reducing costly rework.
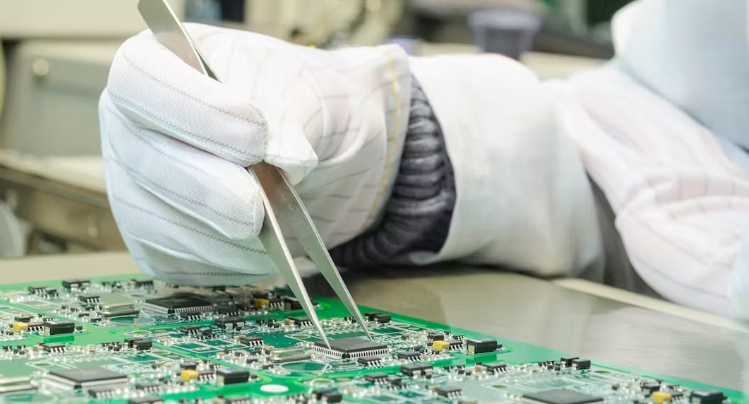
Efficient testing and quality assurance
Testing and quality assurance are key components of the aluminum PCB customization process, ensuring the reliability and performance of the final product. However, these processes can also significantly increase costs. Implementing automated test equipment into a customized process can perform testing faster and more accurately than manual methods, thereby reducing labor costs and increasing throughput. Standardized testing protocols can improve the efficiency and consistency of the testing process. Work with your manufacturer to develop and implement standardized testing procedures that meet industry standards and your specific requirements.
Ultimately
Reducing aluminum PCB customization costs requires choosing based on your product application. Not all products may use the most advanced and best materials and technologies. By employing continuous improvement and innovation in aluminum PCBs by continually seeking ways to improve efficiency and performance, you can achieve long-term cost savings and remain competitive in the market.