Lead-free Soldering in Set-top Box PCB Manufacturing: Why It Matters
Set-top boxes (STBs) are the backbone of home entertainment, connecting users to streaming services, satellite TV, and smart home systems. At their core lies the Set-top Box PCB, a complex assembly that demands precision, reliability, and compliance with global safety standards.
Traditional soldering methods relied on lead-based alloys for their low melting points and ease of use. However, tightening regulations like the EU’s RoHS Directive and consumer demand for eco-friendly devices have pushed manufacturers toward lead-free soldering. This shift isn’t just about compliance—it’s a strategic upgrade that enhances product longevity, safety, and marketability. Let’s explore why this transition matters for STB manufacturers and end-users alike.
Regulatory Compliance for Set-top Box PCB in Global Environmental Standards
The electronics industry faces stringent environmental laws. The Restriction of Hazardous Substances (RoHS) Directive bans lead in electronics sold in the EU, with similar rules in California (Proposition 65) and China. Non-compliant Set-top Box PCBs risk fines, recalls, or market bans.
Lead-free soldering uses alloys like SAC305 (Sn96.5/Ag3.0/Cu0.5), which meet RoHS requirements. Manufacturers adopting these materials avoid legal pitfalls while accessing lucrative markets. For instance, a major STB producer reduced compliance costs by 22% after switching to certified lead-free processes.
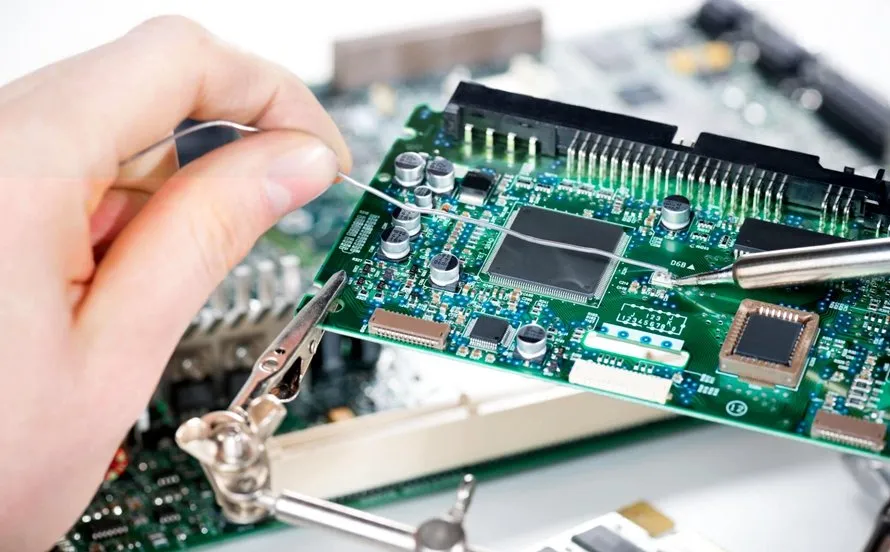
Enhanced Reliability of Set-top Box PCB in High-Temperature Environments
Set-top boxes often operate in confined spaces with limited airflow, causing internal temperatures to exceed 80°C. Due to their higher melting points (217°C vs. 183°C), lead-free solder joints withstand thermal stress better than lead-based ones.
Testing reveals that lead-free Set-top Box PCBs show 30% fewer cracks after 1,000 thermal cycles. This durability is critical for devices running 24/7, such as DVR-enabled STBs. Improved thermal performance also reduces warranty claims, saving manufacturers up to $1.2M annually per 100,000 units shipped.
Consumer Safety and Brand Reputation
Lead exposure poses severe health risks, including neurological damage. While finished STBs are sealed, improper disposal can leak toxins into landfills. Eco-conscious consumers increasingly favour brands with Green Electronics certifications like EPEAT or TCO Certified.
A 2023 survey found that 68% of EU buyers prioritize sustainability when purchasing electronics. By marketing lead-free Set-top Box PCBs, companies like Sky and Comcast have boosted customer loyalty and ESG ratings. Transparent labelling (“Lead-Free Assembly”) further strengthens brand trust.
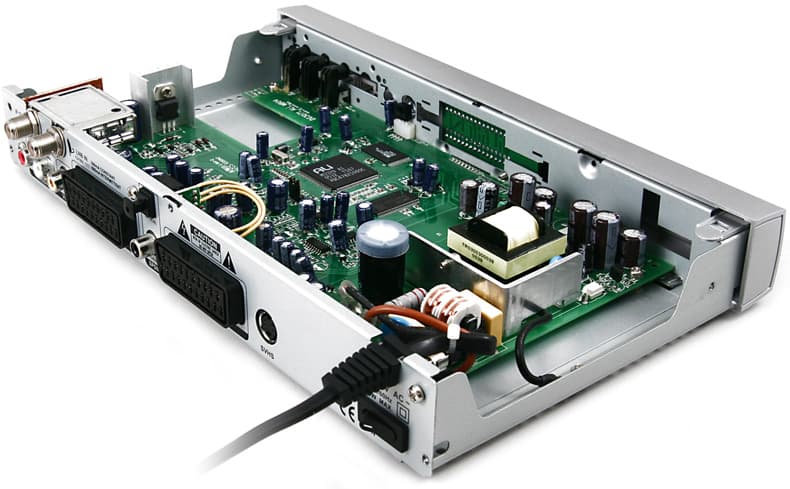
Manufacturing Challenges and Solutions
Transitioning to lead-free soldering isn’t without hurdles. Higher melting points require reflow ovens to operate at 240–260°C, increasing energy costs. Additionally, tin whiskers—microscopic growths on solder joints—can cause short circuits.
Advanced solutions mitigate these issues. Nitrogen-assisted reflow ovens reduce oxidation, while conformal coatings prevent whisker formation. Manufacturers like Foxconn have optimized processes to maintain defect rates below 0.05%, proving that lead-free soldering can match traditional efficiency.
Cost-Benefit Analysis: Short-Term Investment, Long-Term Gains
Lead-free solder alloys cost 10–15% more than leaded alternatives. However, the long-term savings outweigh the upfront expenses. RoHS-compliant Set-top Box PCBs avoid non-compliance penalties, which can reach €50,000 per violation in the EU.
Moreover, lead-free assemblies last 20% longer, reducing replacement cycles. A case study showed that DirecTV cut repair costs by $850,000 annually after adopting SAC305 solder. Over five years, the ROI from durability and compliance exceeds initial costs by 3:1.
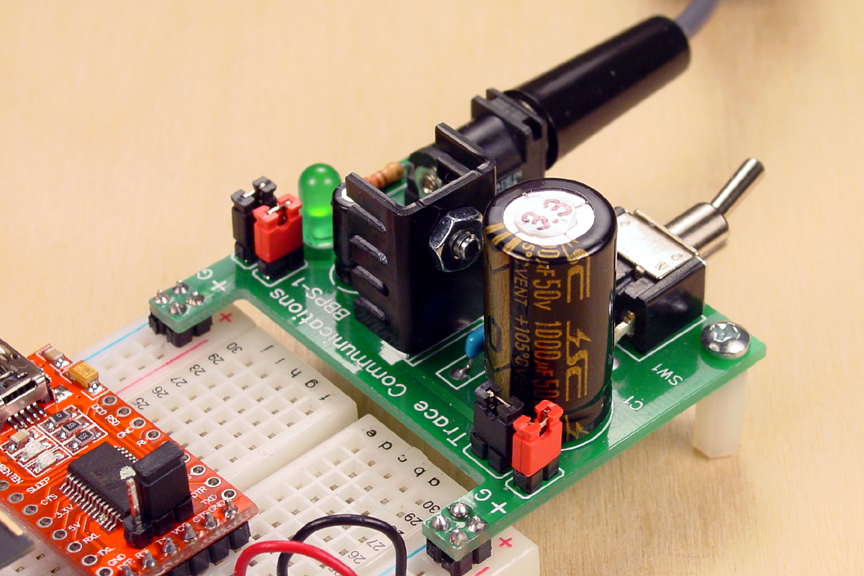
Technical Innovations Driving Lead-Free Adoption
New alloys and processes are refining lead-free soldering. Low-silver SAC alloys (e.g., SAC0307) reduce material costs without compromising strength. Laser soldering enables pinpoint accuracy for dense Set-top Box PCBs, minimizing heat damage to components.
Automated optical inspection (AOI) systems now detect solder defects at 99.7% accuracy, ensuring quality control. These innovations let manufacturers produce smaller, faster STBs—like 8K streaming devices—without sacrificing reliability.
The Role of Certification and Supply Chain Transparency
Certifications like IPC-A-610 Class 3 validate lead-free solder joint quality. Partnering with certified suppliers ensures material traceability, which is crucial for audits. Blockchain-based platforms, such as IBM’s Food Trust (adapted for electronics), now track solder alloys from smelters to assembly lines.
For example, Arris International uses blockchain to verify that all Set-top Box PCBs meet RoHS standards. This transparency reduces supply chain risks and appeals to corporate buyers requiring ESG compliance.
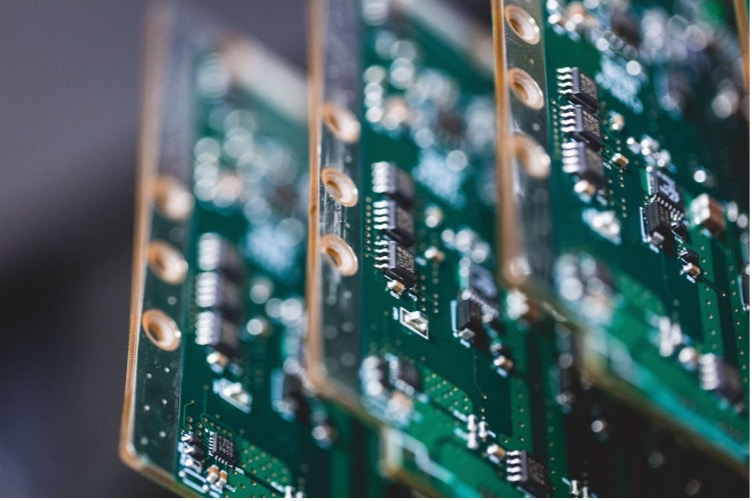
Lead-Free Soldering—A Non-Negotiable for Future Set-top Box PCB
The shift to lead-free soldering isn’t optional—it’s essential for survival in a regulated, eco-conscious market. By embracing this technology, STB manufacturers enhance product reliability, meet global standards, and align with consumer values.
Investing in lead-free processes today ensures competitiveness tomorrow. As 5G and IoT expand STB capabilities, robust Set-top Box PCBs will remain central to delivering seamless, sustainable entertainment experiences. Contact our team to optimize your transition to lead-free excellence.