M6 Material PCB Comparison with Other PCBs
M6 material PCB has advantages over traditional PCB materials due to its unique properties. In recent years, they have often appeared in applications in automobiles, aerospace, and other fields. In this guide, we will explore the advantages of M6 material PCB, compare it with PCB represented by FR4 PCB and aluminum PCB, and introduce their differences and applications.
Learn about M6 Material PCB
M6 material PCB is a PCB substrate that requires high-temperature resistance. M6 refers to the grade of base material, usually consisting of fiberglass fabric impregnated with epoxy resin. One of their main advantages is their enhanced thermal stability, often with a higher glass transition temperature (Tg). This means that M6 material PCBs can withstand high temperatures without deforming or losing mechanical strength, making them suitable for applications that are thermally cycled or exposed to high temperatures, like automotive electronics, industrial control systems, and LED lighting, to name a few. They also have excellent electrical insulation properties, low water absorption, and good chemical resistance, ensuring reliable performance under harsh operating conditions.
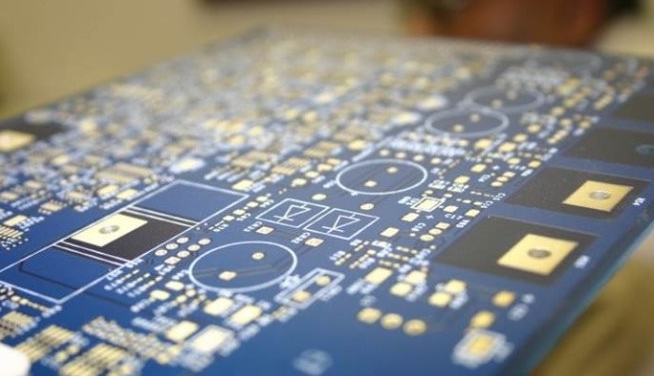
Advantages of M6 material PCB
They have excellent mechanical strength and dimensional stability. They can withstand mechanical stress and vibration during operation, ensuring reliable performance in demanding environments. They also have low water absorption, which helps maintain their electrical insulating properties even in humid conditions. In addition, M6 material PCBs have excellent electrical insulation properties, helping to prevent short circuits and electrical failures. This is critical to maintaining the integrity and functionality of electronic circuits, especially in high voltage or high power applications. They exhibit good resistance to various chemicals and solvents, preventing them from degradation and corrosion in harsh operating environments.
Comparison of M6 material PCB and FR4 PCB
There are similarities between M6 material PCBs and FR4 PCBs, but they also differ significantly in properties, performance, and applications.
- Thermal stability:
Compared to FR4 PCB, M6 material PCB has higher thermal stability and a higher glass transition temperature (Tg). This allows them to withstand high temperatures without significantly losing mechanical or electrical properties, making them suitable for high-temperature applications. The Tg of FR4 PCB is low, which limits its applicability to high-temperature environments. - Mechanical strength and dimensional stability:
M6 material PCB has muscular mechanical strength and dimensional stability, making it more resistant to mechanical stress and vibration during operation. While FR4 PCBs have good mechanical properties, they cannot match the superior strength and stability of M6 material PCBs. - Cost:
In terms of cost, M6 material PCB is usually more expensive than FR4 PCB due to its advanced performance and manufacturing process. FR4 PCBs are versatile and cost-effective, making them the first choice for applications where cost is essential.
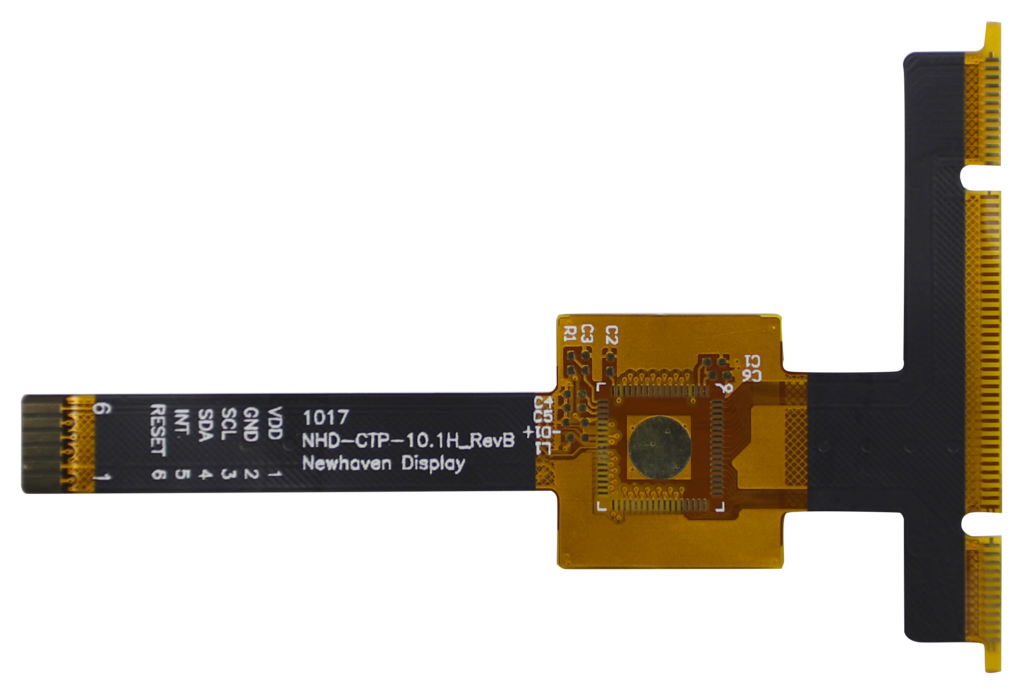
Comparison with Aluminum PCB
They and aluminum PCB are two different printed circuit board substrate materials, each with unique advantages and considerations.
- Thermal conductivity:
M6 material PCBs generally have lower thermal conductivity compared to aluminum PCBs. While they have good thermal stability, they may not dissipate heat, nor may aluminum PCBs. Aluminum PCB has excellent thermal conductivity, effectively dissipating the heat generated by electronic components. - Mechanical strength and durability:
The mechanical strength and durability of M6 material PCBs may not match the rigidity and robustness of aluminum PCBs, known for their high mechanical strength and durability, making them resistant to mechanical stress and vibration. - Weight and dimensions:
M6 material PCBs are typically lightweight and compact, making them suitable for limited space and weight applications.
Aluminum PCBs are larger and heavier because they use aluminum substrates. - Cost:
Due to the advanced performance and manufacturing process of M6 material PCB, M6 material PCB is usually more expensive than aluminum PCB. - Compatibility with high-frequency signals:
M6 material PCBs can provide better high-frequency signal compatibility than aluminum PCBs, which may have limitations in high-frequency applications due to their lower dielectric constant and loss tangent.
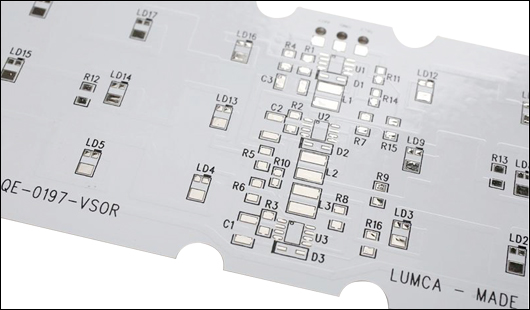
Application of M6 material PCB
Some typical applications for M6 material PCBs include engine control units (ECUs), transmission control modules (TCMs), infotainment systems, and advanced driver assistance systems (ADAS) in automobiles. Industrial equipment such as motor drives, power converters, industrial automation systems, and control panels in industrial equipment. Also suitable for use in LED lighting fixtures, including street, commercial, and automotive lighting.
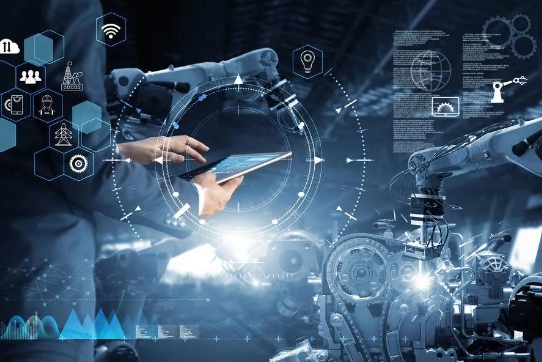
Ultimately
Compared with other PCBs, M6 material PCBs have obvious advantages, especially in thermal management and mechanical strength. Their unique properties make them ideal for various high-performance applications where reliability and durability are critical. Understanding the differences between M6 material PCBs and other PCB materials will enable designers to make the right decisions when choosing the most appropriate substrate for their designs.