The Future of Electronics: How HDI PCB are Driving Miniaturization and Performance
Electronic devices’ miniaturization and high performance are essential in today’s fast-evolving technology landscape. HDI PCB (High-Density Interconnect Printed Circuit Boards) are crucial in meeting these demands. These advanced circuit boards enable smaller, faster, and more efficient electronic products, making them a cornerstone of modern electronics. Whether in consumer electronics, automotive applications, or healthcare devices, HDI PCB technology continues to drive innovation. As industries push for even more compact and robust solutions, the role of HDI PCB in shaping the future of electronics becomes increasingly significant.
The Core Technology Behind HDI PCB
To understand why HDI PCBs are critical to modern electronics, it is essential to examine the technology behind them. Unlike traditional PCBs, which rely on larger trace widths and through-hole vias, HDI PCBs incorporate micro vias, finer traces, and multiple interconnect layers. These features allow for higher circuit density, reduced signal loss, and improved electrical performance. Manufacturers can create precise interconnections using laser drilling techniques, enabling more compact and robust designs. Furthermore, advancements in materials and lamination processes enhance the durability and reliability of HDI PCBs, making them suitable for high-speed and high-frequency applications.
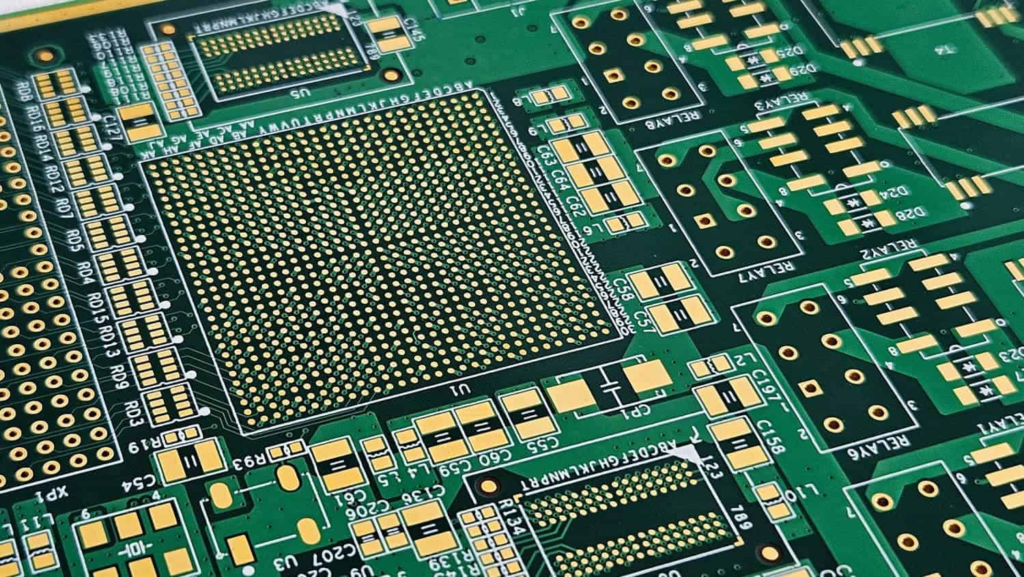
How to Promote Miniaturization of Electronics
Miniaturization is a key trend in modern electronics, and HDI PCBs play a pivotal role in achieving it. As electronic devices become smaller, manufacturers must find ways to integrate more functionality into limited spaces. HDI PCB enables this by reducing component size while maintaining or improving performance. For example, smartphones, wearable technology, and IoT devices benefit from HDI PCB designs, which allow compact and lightweight solutions. By utilizing blind and buried vias, HDI PCBs significantly reduce the need for large interconnect spaces, ensuring that miniaturization does not come at the expense of functionality.
Enhancing Performance with HDI PCB Technology
Beyond miniaturization, HDI PCBs also enhance overall device performance. As consumer expectations for speed, efficiency, and power consumption increase, manufacturers must turn to HDI PCBs to optimize circuit design. These boards improve signal integrity, reduce electromagnetic interference (EMI), and enhance thermal management. HDI PCBs minimize latency and power loss by shortening signal paths and using advanced routing techniques. High-speed computing, advanced networking, and next-generation mobile devices rely on these benefits to deliver seamless user experiences. Additionally, HDI PCB supports the integration of high-performance processors and memory modules, which are essential for data-intensive applications.
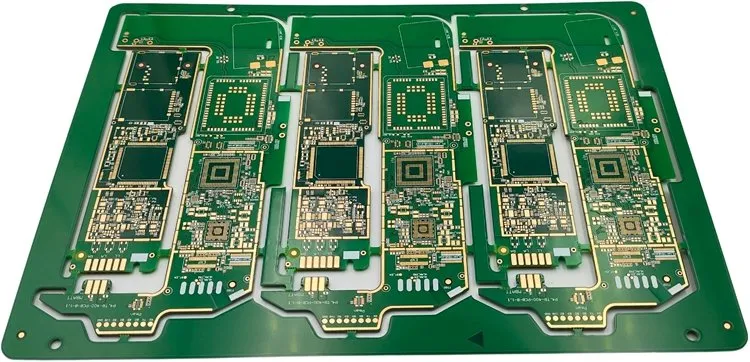
Role in Consumer Electronics
Consumer electronics manufacturers are among the biggest adopters of HDI PCBs. The demand for sleeker, more powerful devices drives innovation in PCB technology. Smartphones, tablets, and gaming consoles all utilize HDI PCBs to maximize space while maintaining high performance. Features such as high-resolution displays, multiple camera systems, and 5G connectivity require intricate circuit designs, which HDI PCBs enable. As new technologies like foldable screens and augmented reality gain popularity, HDI PCBs will continue to be a foundational element in consumer electronics, allowing for more sophisticated and feature-rich products.
Applications in the Automotive Industry
The automotive sector is transforming with the rise of electric vehicles (EVs), autonomous driving, and advanced infotainment systems. HDI PCB is integral to these developments, enabling compact and reliable electronic control units (ECUs). HDI PCBs help optimize battery management systems, power distribution networks, and onboard computing in EVs. Automotive radar, LiDAR, and sensor-based safety systems depend on HDI PCB for fast data processing and accurate signal transmission. As vehicles become more intelligent and connected, HDI PCB technology will remain essential to ensure reliability and performance in extreme conditions.
Medical and Industrial Applications of HDI PCB
In the medical and industrial sectors, HDI PCBs enable the creation of high-precision, compact devices. Medical equipment such as portable imaging systems, wearable health monitors, and implantable devices rely on HDI PCB for their small form factors and high reliability. In industrial automation, HDI PCB supports robotics, sensors, and control systems that require complex circuitry in limited space. The durability and efficiency of HDI PCBs make them ideal for harsh environments where reliability is paramount. As medical and industrial technologies advance, HDI PCBs will enable innovation.
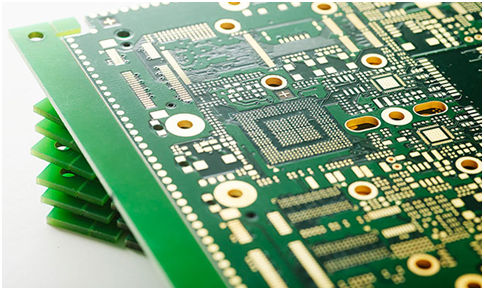
The Future of HDI PCB in Electronics
As the demand for smaller, faster, and more efficient electronics grows, HDI PCBs will remain at the forefront of innovation. The ability to integrate complex circuits into compact designs makes HDI PCBs an indispensable technology in consumer electronics, automotive systems, and medical devices. With continuous advancements in materials, manufacturing processes, and circuit design, HDI PCBs will continue to push the boundaries of what is possible in electronic miniaturization and performance. For industries looking to stay ahead in an increasingly competitive market, investing in HDI PCB technology is no longer optional—it is a necessity.