The main differences between Aluminum substrate PCB and FR4 PCB
When making PCB for some applications, we often choose PCB. This time, we will tell you below how to distinguish aluminum substrate PCB from FR4 PCB. What is the difference between them? Each type of PCB has its unique characteristics, advantages, and applications. Understanding the distinction between these differences can aid designers in optimizing circuit choices for various applications.
Aluminum substrate PCB
Aluminum substrate PCBs (metal-core PCBs) are increasingly gaining importance in applications requiring superior thermal management. The aluminum core in these PCBs acts as a highly efficient heat sink, dissipating heat more effectively than traditional substrates. This is especially beneficial in high-power applications where thermal considerations are critical. Designers can take advantage of this feature to improve electronic systems’ overall reliability and longevity.
Thermal conductivity:
One of the outstanding features of aluminum substrate PCBs is their excellent thermal conductivity. The aluminum core facilitates rapid heat dissipation and prevents components from overheating. This characteristic makes aluminum substrate PCBs a superb choice for LED applications, power electronics, and any scenario where thermal management is critical. PCB design engineers can optimize their designs to reduce operating temperatures, ensuring optimal performance and minimizing the risk of heat-induced failure.
Lightweight design and enhanced durability
In addition to thermal benefits, aluminum substrate PCBs offer lightweight designs, making them suitable for applications where weight is critical. Additionally, aluminum’s strong properties enhance PCBs’ durability, making them resistant to mechanical stress and environmental factors. This durability factor can extend the life of electronic devices.
Advanced precision manufacturing process:
The production of aluminum substrate PCBs involves complex manufacturing processes to ensure precision and quality. The aluminum core is typically covered with dielectric and copper layers, and the design is etched using advanced techniques. This level of accuracy enables complex circuit patterns, making aluminum substrate PCBs suitable for applications requiring high complexity and reliability.
Wide temperature range applications:
Aluminum substrate PCBs exhibit stability over a wide temperature range, making them ideal for applications exposed to extreme environmental conditions. Whether in automotive electronics, where temperatures vary, or in industrial environments, where ambient temperatures are higher, aluminum substrate PCBs maintain consistent performance.
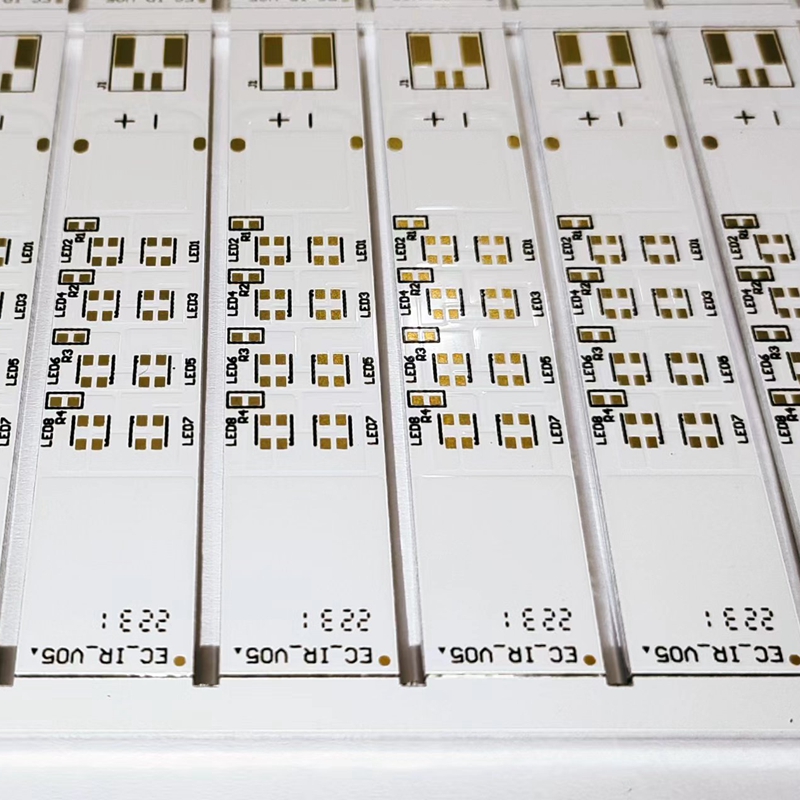
FR4 PCB: Traditional Versatility in PCB Design
They have long been the first choice for a variety of applications. FR4 consists of fiberglass-reinforced epoxy resin laminate (which we have also mentioned in previous articles). This substrate is widely used in consumer electronics, industrial applications, and other fields, providing reliable and economical solutions for various design needs.
Electrical isolation and signal integrity
One of the critical attributes of FR4 PCB is its excellent electrical insulation properties. Fiberglass reinforcement ensures the PCB maintains high electrical insulation, preventing signal leakage and interference. This makes FR4 PCBs ideal for high-frequency circuits and communication systems.
Cost effective and mass-production
Due to the wide availability of materials and well-established manufacturing processes, FR4 PCBs provide an economical solution for mass production. This cost-effectiveness makes FR4 an attractive option for applications where budget constraints play a significant role. Designers can strike a balance between performance and economy.
Robust design for a variety of applications
The ruggedness of FR4 PCB makes it suitable for a wide range of applications. Their mechanical strength and resistance to environmental factors contribute to their longevity in different environments. From consumer electronics to industrial automation, FR4 PCBs provide a reliable foundation for electronic systems, ensuring long-term stable performance.
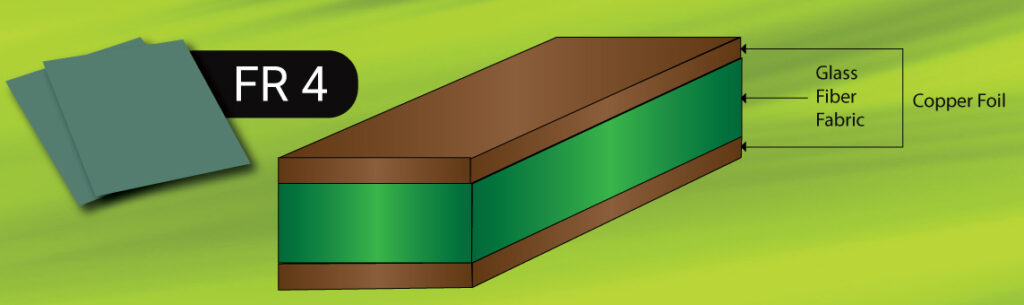
Choose between Aluminum substrate PCB and FR4 PCB
Application-specific considerations
The choice between aluminum base PCB and FR4 PCB ultimately depends on the project’s specific requirements. For high-power applications with stringent thermal requirements, aluminum substrate PCBs excel. On the other hand, if cost-effectiveness and versatility are a priority, FR4 PCB may be the first choice. Therefore our design engineers must carefully evaluate the project needs before deciding.
Thermal considerations in design optimization
When thermal considerations are critical, designers should weigh the advantages of aluminum substrate PCBs. These PCBs excel in scenarios where effective heat dissipation is vital, preventing performance degradation and ensuring the longevity of electronic components.
Material compatibility in different environments
Aluminum substrate PCBs and FR4 PCBs have different material properties that affect their performance in various environments. Aluminum has excellent thermal conductivity, making it ideal for applications where temperature changes. The FR4 features strong fiberglass reinforcements that provide stability in multiple settings.
Make the choice that’s right for you
The choice between aluminum substrate PCB and FR4 PCB ultimately comes down to the specific requirements of your project. Aluminum substrate PCBs offer superior thermal management and durability, while FR4 PCBs offer versatility and cost-effectiveness. This is the most significant difference between the two, and our design engineers must carefully evaluate their application priorities and weigh the advantages of each substrate to make the best choice.