The Role of Rigid-Flex PCB in Advancing SSD and HDI Technology
In the fast-paced world of electronics, where speed, reliability, and miniaturization are king, Rigid-Flex PCB technology has quietly become a game-changer. Rigid-flex PCBs are at the heart of modern tech advancements, from powering the latest solid-state drives (SSDs) to enabling high-density interconnect (HDI) designs. But what makes them so unique? And how are they shaping the future of storage and connectivity? Let’s dive into the critical role Rigid-Flex PCBs play in advancing SSD and HDI technology—and why they’re indispensable in today’s electronics landscape.
What Is Rigid-Flex PCB
A Rigid-flex PCB combines the best of both worlds: rigid boards’ stability and flexible circuits’ adaptability. These hybrid boards use layers of flexible polyimide film sandwiched between rigid sections, allowing them to bend and fold without breaking. This unique design eliminates the need for connectors and cables, reducing weight and space while improving reliability.
In SSDs, a Rigid-Flex PCB enables compact, high-performance designs. For example, Samsung’s latest NVMe SSDs use Rigid-Flex boards to fit more storage into smaller form factors. Similarly, in HDI applications, these boards support intricate routing and higher signal integrity, which are essential for devices like smartphones and wearables. Manufacturers achieve sleeker, faster, and more durable products by integrating Rigid-Flex PCBs.
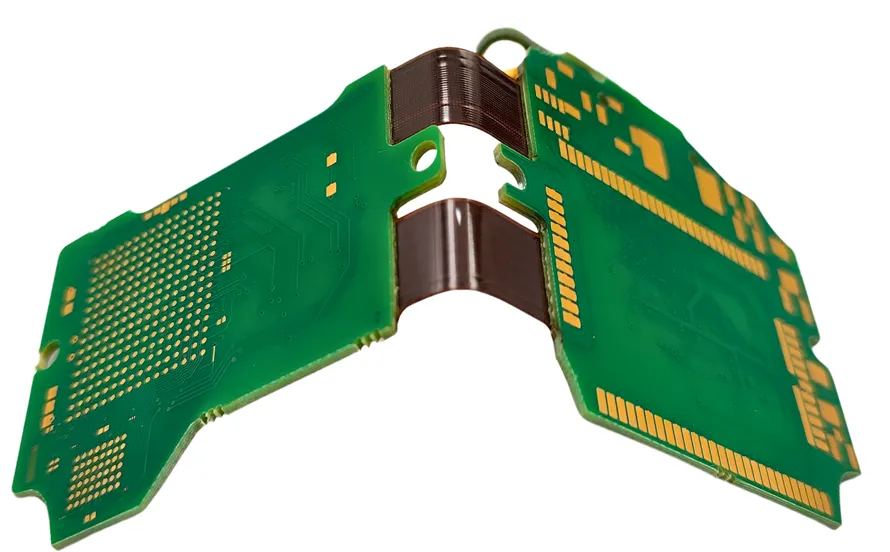
Driving SSD Performance: Speed, Space, and Reliability
Solid-state drives (SSDs) have revolutionized data storage, offering faster read/write speeds and more excellent durability than traditional hard drives. Rigid-flex PCBs play a pivotal role here. Their compact design allows SSD manufacturers to pack more NAND flash chips into smaller spaces, boosting storage capacity without increasing size.
Take the PCIe Gen 4 SSDs, for instance. These drives rely on Rigid-Flex PCBs to handle high-speed data transfers—up to 7,000 MB/s. The flexible sections of the board absorb vibrations, reducing wear and tear, while the rigid sections ensure stable connections. This combination enhances both performance and longevity. According to a 2023 report by TrendForce, a Rigid-Flex PCB has helped SSD manufacturers reduce failure rates by 15% while increasing storage density by 20%.
Enabling HDI Technology: Precision in Miniaturization
High-density interconnect (HDI) technology involves packing more functionality into smaller devices. Rigid-flexRigid-flex PCBs are a natural fit for HDI designs, as they can support complex routing and multiple layers in a compact form.
Smartphones are a prime example. Apple’s iPhone 15 uses Rigid-Flex PCBs to connect its camera module, display, and motherboard seamlessly. This eliminates bulky connectors, freeing space for larger batteries or additional sensors. Rigid-flex PCBs enable ultra-thin designs for implants and wearables in medical devices, improving patient comfort and device performance. A study by Grand View Research predicts the HDI market will grow by 8.5% annually, driven by the demand for smaller, more innovative devices—and Rigid-Flex PCBs are at the forefront of this trend.

The Manufacturing Edge: Why Rigid-Flex PCBs Shine
Producing Rigid-Flex PCBs is no small feat, but the benefits outweigh the challenges. These boards require advanced manufacturing techniques, such as laser drilling and sequential lamination, to achieve precise layer alignment and reliable connections.
Despite the complexity, Rigid-Flex PCBs reduce assembly costs by eliminating connectors and cables. They also improve product reliability by minimizing points of failure. For example, in aerospace applications, Rigid-Flex PCBs withstand extreme temperatures and vibrations, ensuring consistent performance. A case study by Flex Ltd. revealed that switching to Rigid-Flex PCBs reduced assembly time by 30% and cut material costs by 25% in a satellite project.
Challenges and Solutions: Overcoming the Hurdles
While Rigid-Flex PCBs offer numerous advantages, they’re not without challenges. Designing these boards requires expertise in both rigid and flexible circuit technologies. Misalignment during lamination or improper bend radius can lead to failures.
However, advancements in design software and manufacturing techniques are addressing these issues. Tools like Altium Designer now include Rigid-Flex-specific features, enabling engineers to simulate bends and optimize layouts. Additionally, manufacturers are adopting automated optical inspection (AOI) systems to detect defects early in the process. These innovations are making Rigid-Flex PCBs more accessible and reliable than ever.
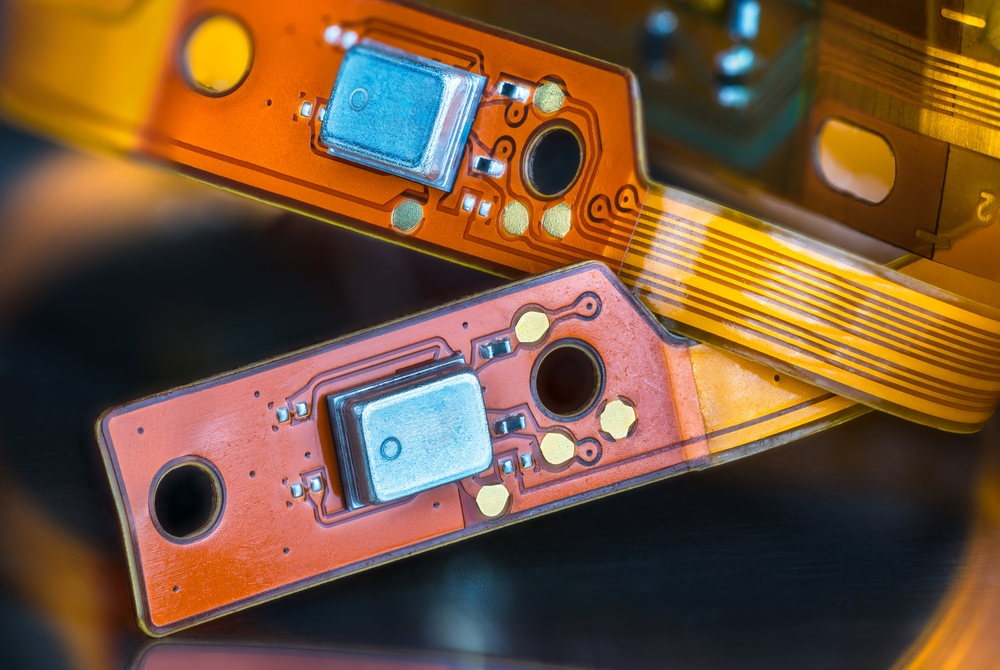
Sustainability and Future Trends: A Greener Path Forward
As the electronics industry embraces sustainability, Rigid-Flex PCBs play a key role. Their ability to reduce material waste and energy consumption aligns with global green initiatives. For instance, using fewer connectors means less plastic and metal waste.
Looking ahead, Rigid-Flex PCBs are set to enable even more groundbreaking applications. Foldable smartphones, flexible displays, and next-gen SSDs will rely on these boards for their compact, durable designs. According to MarketsandMarkets, the Rigid-Flex PCB market will grow at a CAGR of 9.2% through 2028, driven by demand for advanced electronics.
Why Rigid-Flex PCB Is the Future of Electronics
From boosting SSD performance to enabling HDI breakthroughs, Rigid-Flex PCBs are transforming the electronics industry. Their unique flexibility, durability, and compact blend make them indispensable in today’s tech-driven world.
As devices become smaller, faster, and more complex, Rigid-Flex PCBs will continue to push the boundaries of what’s possible. Whether you’re designing the next-gen smartphone or a cutting-edge medical device, these boards offer the reliability and innovation you need. The future of electronics is flexible—and Rigid-Flex PCBs are leading the way.