Understanding Carbon Ink PCB: Benefits and Applications
Carbon-ink PCB technology represents a cost-effective solution for various electronic applications. These printed circuit boards utilize conductive carbon-based inks instead of traditional copper traces, offering unique advantages in specific use cases. Due to their simplicity and reliability, carbon-ink PCB designs have gained popularity in consumer electronics, automotive controls, and medical devices.
Carbon Ink PCB’s manufacturing process differs significantly from that of conventional PCBs. Screen printing deposits the conductive carbon ink onto substrate materials, creating durable conductive pathways. This method eliminates complex etching processes while maintaining adequate conductivity for many applications. The technology continues evolving to meet modern electronic demands.
Cost-Effective Production Advantages
Carbon Ink PCB manufacturing reduces production expenses through simplified processes. The screen printing technique requires fewer steps than traditional PCB fabrication, cutting labour and material costs. Manufacturers save on copper and chemical etchants while maintaining functional circuit performance.
These boards also minimize waste during production. Unlike subtractive copper etching, carbon ink application adds material only where needed. This efficient process appeals to environmentally conscious companies seeking sustainable manufacturing options. The cost benefits make carbon ink ideal for high-volume, low-complexity circuits.
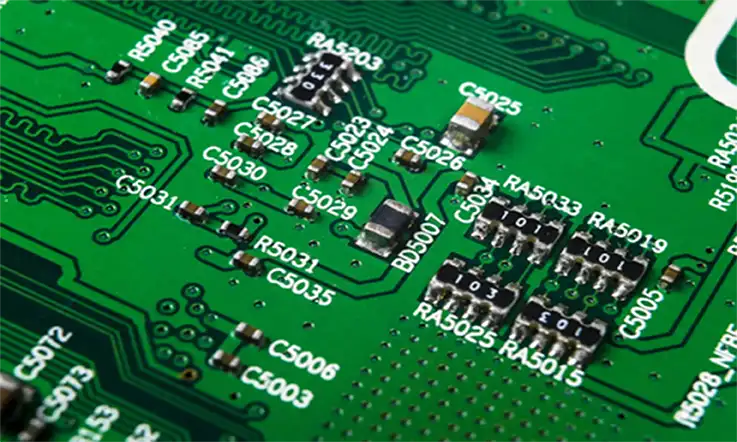
Durability and Environmental Resistance
Carbon-based circuits demonstrate remarkable resilience in challenging conditions. The surface of Carbon Ink PCBs resists corrosion better than exposed copper traces, performing well in humid environments. The material maintains conductivity when moisture, chemicals, and temperature fluctuations are exposed.
The ink’s composition provides excellent mechanical durability. Carbon layers withstand repeated flexing better than thin copper traces, making them suitable for flexible circuits. This characteristic proves valuable in wearable devices and automotive applications where vibration resistance matters.
Application-Specific Benefits
Carbon Ink PCB technology excels in membrane switches and touch interfaces. The material’s consistent resistivity creates reliable contact surfaces for buttons and controls. Many appliance panels and industrial controls utilize carbon ink circuits for their tactile responsiveness and longevity.
Medical devices frequently incorporate carbon ink circuits for disposable applications. The cost structure supports single-use diagnostic equipment while maintaining performance standards. Carbon’s biocompatibility also makes it suitable for certain implantable devices.
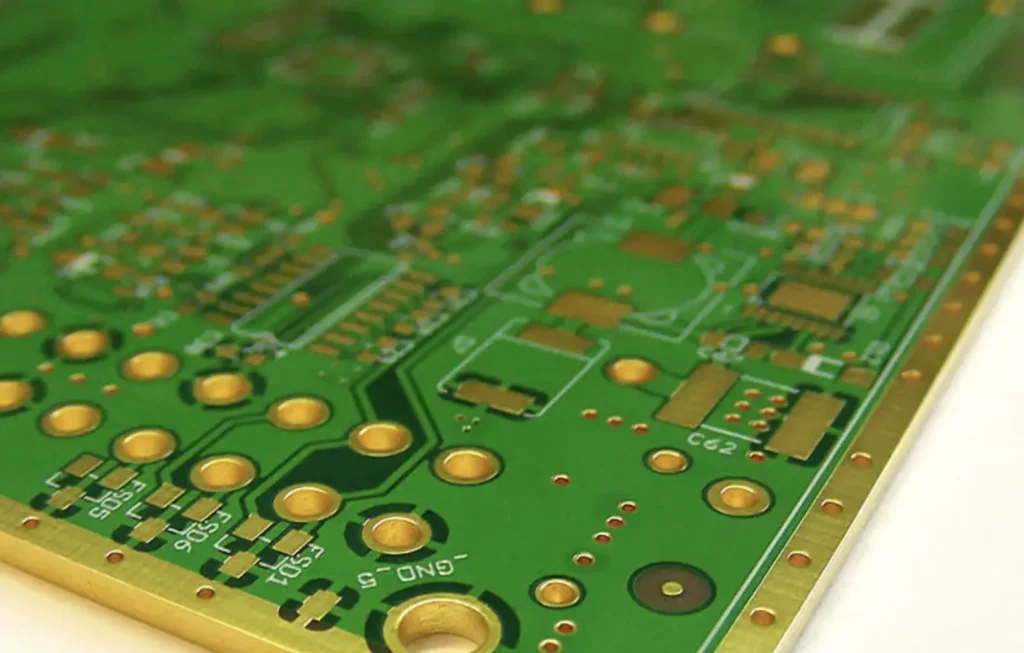
Design Flexibility and Customization
Engineers appreciate the layout freedom Carbon Ink PCB designs provide. The printing process accommodates complex patterns without additional cost penalties, allowing designers to create custom-shaped circuits that perfectly fit unique product enclosures.
The technology supports hybrid designs combining carbon and traditional copper elements. This approach allows optimized performance where standard circuits need enhancement. Manufacturers can print carbon contacts over conventional PCBs to create durable connection points.
Electrical Performance Characteristics
While less conductive than copper, carbon ink provides sufficient performance for many applications. Typical Carbon Ink PCB traces exhibit sheet resistance of 5-50 ohms per square, adequate for most low-current circuits. Advanced formulations continue improving conductivity while maintaining other benefits.
The material’s consistent resistance makes it ideal for creating resistors directly on boards. Designers can print precise resistive elements without additional components. This integration simplifies circuits and reduces part counts in many designs.
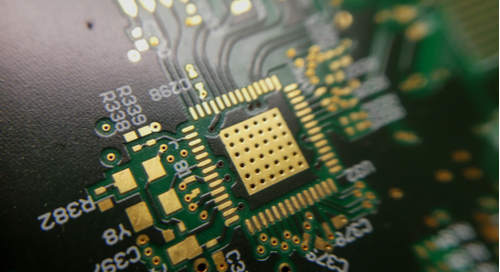
Manufacturing Considerations and Limitations
Carbon Ink PCB production requires specialized printing equipment and expertise. Manufacturers must carefully control ink viscosity, curing temperatures, and printing parameters. Proper process validation ensures consistent conductivity across production runs.
The technology faces limitations in high-frequency applications. Carbon’s higher resistance makes it less suitable for RF circuits or high-speed digital signals. Designers must evaluate current requirements before selecting carbon ink solutions.
The Expanding Role of Carbon Ink PCB
Carbon Ink PCB technology continues to find new applications across industries. Its unique cost efficiency, durability, and design flexibility make it invaluable for specific electronic solutions. Carbon ink circuits will likely expand into more demanding applications as material science advances.
The technology bridges the gap between conventional PCBs and printed electronics. Carbon Ink PCB solutions offer manufacturers a practical alternative when copper circuits prove excessive or cost-prohibitive. Their continued development promises to unlock new possibilities in electronic design and manufacturing.