What are the factors that affect double side PCB pricing?
PCBs are the backbone of most modern electronic devices. Among the various types of PCBs, double side PCBs are widely used in industries where space and functionality are critical. These boards feature conductive layers on both sides, which allow for higher component density and more complex circuit designs. Many users are curious about how double side PCB is priced. Next, we will explore the key factors affecting double side PCBs’ cost and pricing.
Material Quality and Type
One of the most significant factors influencing the price of a double side PCB is the type and quality of materials used in its production. The base material of a PCB is typically fiberglass or epoxy resin, with copper being the most common conductor. However, variations in material quality can significantly impact the overall cost.
For example, using high-quality copper with a thicker layer can improve the board’s conductivity and increase cost. Similarly, some projects may require more advanced materials, such as high-frequency or heat-resistant substrates, which are typically more expensive. The selection of material directly affects the PCB’s performance and price. In general, the more specialized the material, the higher the cost.
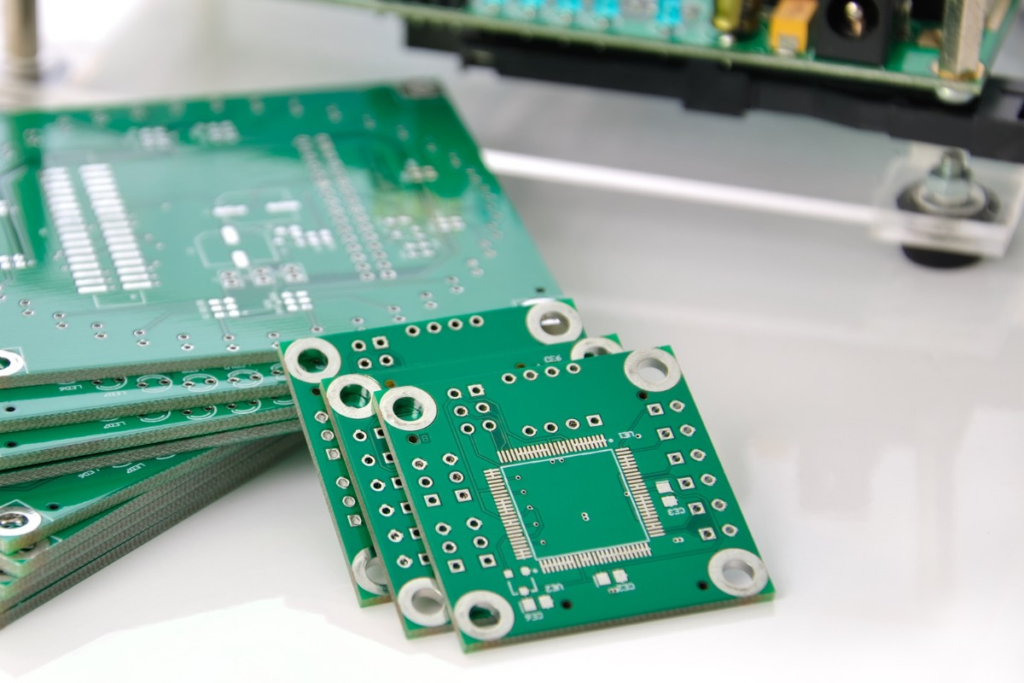
Board Size and Complexity of Design
The size of a double side PCB and the complexity of its design can also significantly impact its price. Larger boards require more materials, manufacturing time, and advanced machinery. Additionally, if the board has a high component density or a complex routing layout, the price will rise due to the extra work needed in design and manufacturing processes.
Complex designs with intricate routing and tight tolerances are more labor-intensive to produce. This often requires advanced technologies, like precision drilling and multi-layer stacking, which increase the cost of labor and the time required for manufacturing. Similarly, smaller boards or simpler designs may be produced more quickly and at a lower price, making size and design complexity crucial in determining final pricing.
Production Volume and Order Size
Production volume plays a crucial role in determining the price of double side PCBs. Manufacturers often offer bulk discounts, meaning that the more units you order, the lower the cost per unit. However, the price per PCB may be significantly higher for small-scale projects or prototypes due to the relatively high setup costs and lower production volume.
On the other hand, large production runs benefit from economies of scale, reducing the overall cost per unit. Therefore, for businesses looking to order PCBs in bulk, negotiating larger order quantities may be an effective way to lower the unit price. This is especially relevant for companies with high manufacturing demands, as larger orders generally result in lower production costs over time.
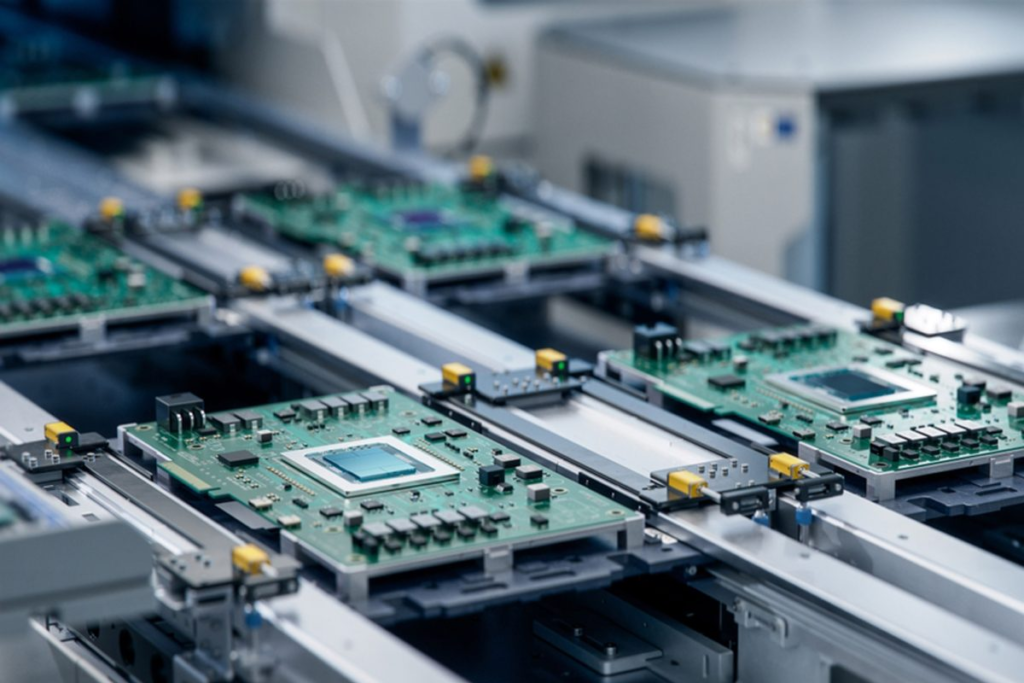
Surface Finish and Coating Options
Other significant factors that affect a double side PCB’s pricing are the surface finish and coating options. A PCB’s surface finish is crucial for ensuring the proper connection between components, and different finishes come with varying costs. The most common surface finishes include HASL (Hot Air Solder Leveling), ENIG (Electroless Nickel Immersion Gold), and OSP (Organic Solderability Preservative), each of which has its own set of characteristics.
For instance, ENIG provides superior reliability and performance, especially for high-density boards, but it is more expensive than HASL due to its more complex manufacturing process. Additionally, specialized coatings such as silver or gold plating may further raise the cost of production. The choice of surface finish not only affects the board’s performance but also impacts its final price.
Manufacturing Technology and Equipment
The manufacturing process and technology for double side PCBs significantly impact their pricing. Advanced technologies, such as laser drilling, fine-pitch components, or micro-via designs, can raise the cost of manufacturing. These technologies are often necessary for boards with high-performance requirements or those designed for small, compact devices.
Furthermore, the equipment used in the manufacturing process can influence both the quality and cost of production. For example, manufacturers with state-of-the-art machinery can produce higher-quality PCBs more efficiently. Still, the cost of operating and maintaining such equipment is often passed on to the customer. Conversely, older or less sophisticated machinery may produce lower-quality boards at a more affordable price but may not meet the stringent requirements for specific applications.
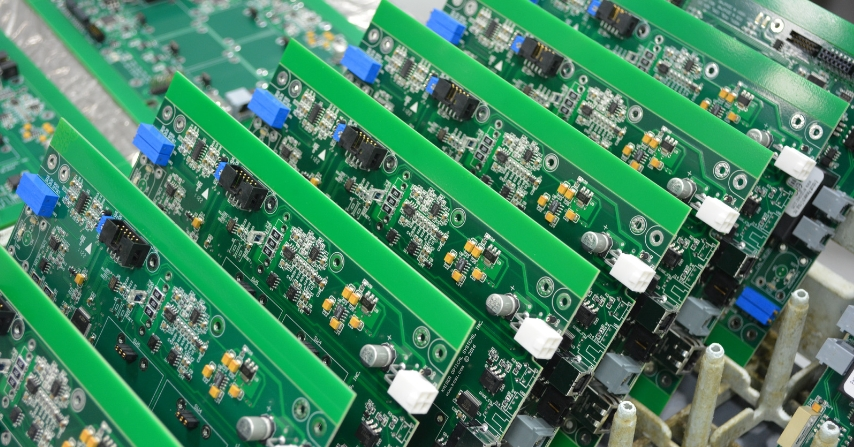
Regulatory Compliance and Certifications
In some industries, double side PCBs must meet specific regulatory standards and certifications, which can affect their cost. For example, medical, aerospace, or automotive PCBs must comply with strict safety and reliability standards, such as ISO 13485 or IATF 16949.
These regulatory requirements often require additional testing, higher-quality materials, and more precise manufacturing processes. As a result, PCBs that meet these standards tend to be more expensive than those used in consumer electronics or less regulated industries. The extra costs associated with obtaining certifications, conducting tests, and ensuring compliance add to the overall price of the PCB.
The lead time and urgency required for double side PCB
The lead time needed to manufacture and deliver double side PCB can also influence their price. Standard lead times are typically longer, especially for complex or custom boards. However, expedited manufacturing and shipping options can significantly increase costs if you need your PCBs quickly.
Manufacturers may charge a premium for rush orders or those requiring fast turnaround times, as these orders often necessitate priority scheduling and additional resources. Opting for a standard lead time can help you save money if you are not in a hurry. However, if your project is time-sensitive, paying for faster production may be necessary but will likely increase your overall expenses.

Custom Design and Prototyping Services for double side PCB
For companies or individuals seeking custom-designed double side PCBs, the cost of prototyping can also add to the overall price. Designing a custom PCB typically involves more time for engineers to develop the schematic and layout and testing and prototyping to ensure the design meets performance expectations.
Prototyping is an essential step in the development process, but it can be costly, especially for complex or novel designs. The more iterations or revisions required, the higher the cost will be. Once the prototype is finalized, the cost of mass production may be reduced, but initial development costs should be factored into the overall price.
Thoroughly consider the factors that affect double side PCB pricing
Understanding the factors influencing the pricing of double side PCBs is essential for making informed decisions and optimizing your purchasing strategy. By carefully considering material quality, design complexity, production volume, and other factors, you can effectively manage costs while obtaining high-quality PCBs that meet your needs.