What are the reliability standards for multi-layer PCB in the automotive industry?
In the automotive manufacturing industry, circuit boards, and control systems ensure vehicle safety, efficiency, and performance, among other things. Multi-layer PCB is at the heart of these electronic systems, powering everything from the car’s infotainment system to ADAS. Given the harsh operating conditions in automotive applications, reliability standards for multi-layer PCBs are critical. This guide will explore these reliability standards.
Material selection is the foundation of multi-layer PCBs
For multi-layer PCBs in the automotive industry, materials must withstand extreme temperatures, humidity, and mechanical stress. FR-4 is the most widely used material for multilayer PCBs because it offers an excellent balance of performance, cost, and availability. It consists of woven fiberglass cloth and a flame-retardant epoxy adhesive. It also has good thermal stability, and it can withstand high temperatures during the soldering process and in the operating environment. Depending on the application, we choose copper foil of different thicknesses. Standard copper foil (1 oz/ft2) is suitable for most uses, while thick copper foil is used for high current uses to ensure sufficient current carrying capacity.
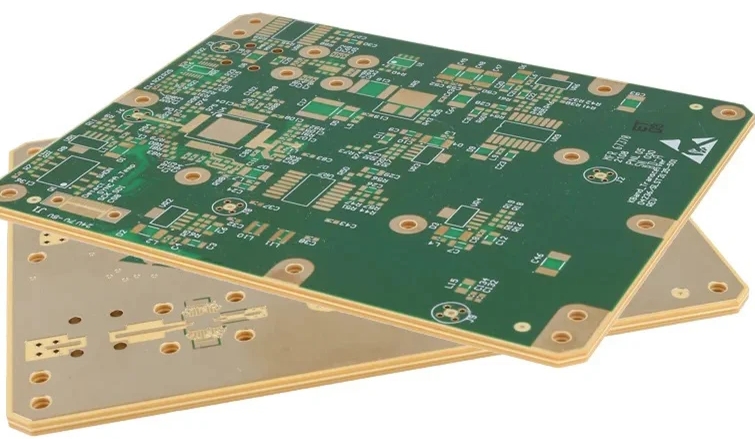
Design Considerations for Multi-layer PCB
The design level also affects the reliability of multi-layer PCB. Proper layout, layer stackup, and trace routing are critical to minimize signal interference and ensure efficient heat dissipation. In the automotive industry, where space layout is limited, our designers optimize PCB layouts to fit into tight spaces while maintaining reliability. Thermal management is particularly important because overheating can degrade the performance of electronic components. Effective thermal management is critical for automotive PCBs to prevent overheating and ensure reliability. Materials with high thermal conductivity, such as aluminum or copper cores, can be integrated into the PCB stack up to improve heat dissipation. The thermal performance and reliability of multilayer PCBs are also enhanced by using techniques such as through-hole stitching, thermal vias, and heat sinks.
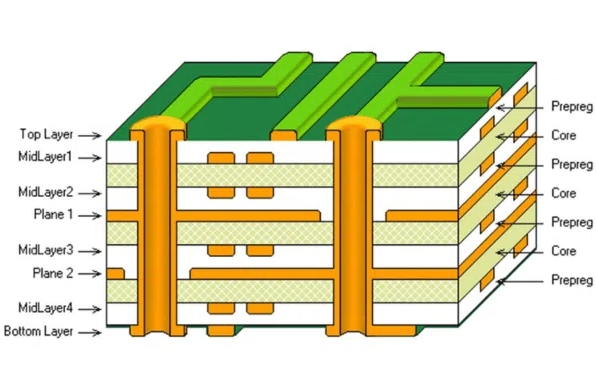
Impact of Manufacturing Process on Reliability
The manufacturing process of multi-layer PCBs involves several key steps, including lamination, drilling, plating, and solder mask application. Precision and quality control at each stage ensure the reliability of the final product. In the automotive industry, we adhere to more stringent quality standards, such as ISO/TS 16949, which focuses on continuous improvement and defect prevention. Drilling and creating vias to connect different layers is a critical step, and laser or mechanical drilling techniques must ensure that the holes are clean and precise and do not damage surrounding materials.
Chemical copper plating and electroplating processes deposit a thin layer of copper inside the drilled holes and on the surface of the PCB, providing a conductive path between layers. In addition, etching processes remove excess copper, leaving only the desired circuit pattern. The accuracy of this step can avoid over-etching or under-etching, which can affect circuit performance and reliability.
Testing and Validation
Testing and validation are an integral part of the multi-layer PCB manufacturing process to ensure that they meet the stringent reliability standards of the automotive industry.
Electrical Testing
Electrical testing verifies the integrity of circuit connections and insulation between conductive elements. ATE checks PCBs for continuity, shorts, opens, and impedance matching. High potential (hipot) testing evaluates insulation resistance between conductors and ensures compliance with safety standards.
Thermal Cycling and Environmental Testing
Thermal cycling subjects multi-layer PCBs to alternating extreme temperatures to simulate real-world conditions encountered in automotive environments. This test evaluates the PCB’s ability to withstand thermal expansion and contraction without compromising electrical performance or mechanical integrity. Environmental testing evaluates the PCB’s ability to resist moisture, corrosion, and chemical degradation.
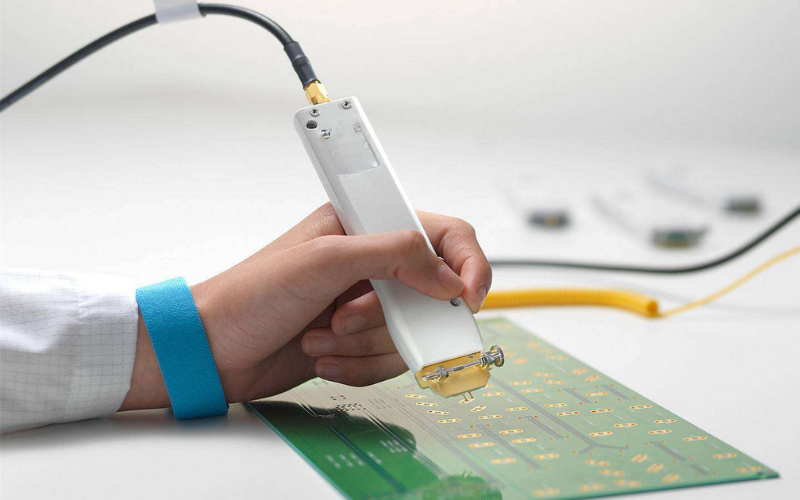
Vibration and Mechanical Shock Testing
In the automotive industry, multi-layer PCBs must also withstand continuous vibration and mechanical shock from road conditions and vehicle movement. Vibration testing evaluates multi-layer PCBs’ mechanical strength and ability to withstand continuous vibration without component fall-off or solder joint failure. Mechanical shock testing simulates sudden shock or vibration to ensure that multi-layer PCBs remain intact and function appropriately under sudden vehicle maneuvers or road disturbances.
Ongoing Monitoring and Maintenance
This includes regular inspections, performance evaluations, and implementation of corrective actions when necessary. Technologies such as automated test systems and in-line monitoring during manufacturing can identify potential defects such as solder joint cracks, delamination, or component drift. Early detection allows for timely corrective actions to minimize risks that could affect vehicle safety. Scheduled maintenance protocols involve regular inspections and repairs of automotive electronics. This proactive approach includes cleaning PCB components to remove dust and debris that could cause overheating or electrical shorts, ensuring they remain intact and effectively protected from environmental factors such as moisture and vibration.
Ensuring the Reliability of Multi-layer PCB for Automotive
The reliability standards for multilayer PCBs in the automotive industry are comprehensive and stringent. From material selection and design considerations to manufacturing processes and testing, every aspect plays a role in ensuring the durability and functionality of multilayer PCBs. By adhering to these stringent standards, we can provide automotive customers with multilayer PCBs with consistent performance, safety, and reliability.