What is the difference between ceramic PCB and FR4 PCB?
Choosing the right material for printed circuit boards (PCBs) ensures optimal performance, reliability, and cost-effectiveness. Two of the most widely used materials are ceramic PCB and FR4 PCB. While both serve as the backbone of electronic devices, they differ significantly in terms of material properties, applications, and performance. This article explores the key differences between ceramic PCB and FR4 PCB, helping you make an informed decision for your next project.
Material Composition: Ceramic PCB vs. FR4 PCB
The fundamental difference between ceramic PCBs and FR4 PCBs is their material composition. Ceramic PCBs are made from ceramic materials such as aluminum oxide (Al2O3), aluminum nitride (AlN), or beryllium oxide (BeO). These materials offer exceptional thermal conductivity, mechanical strength, and resistance to high temperatures.
On the other hand, FR4 PCBs are constructed from a fiberglass-reinforced epoxy laminate. FR4 is a cost-effective and widely available material but lacks ceramics’ advanced thermal and mechanical properties. While FR4 suits general-purpose applications, ceramic PCBs excel in demanding environments where performance and reliability are paramount.
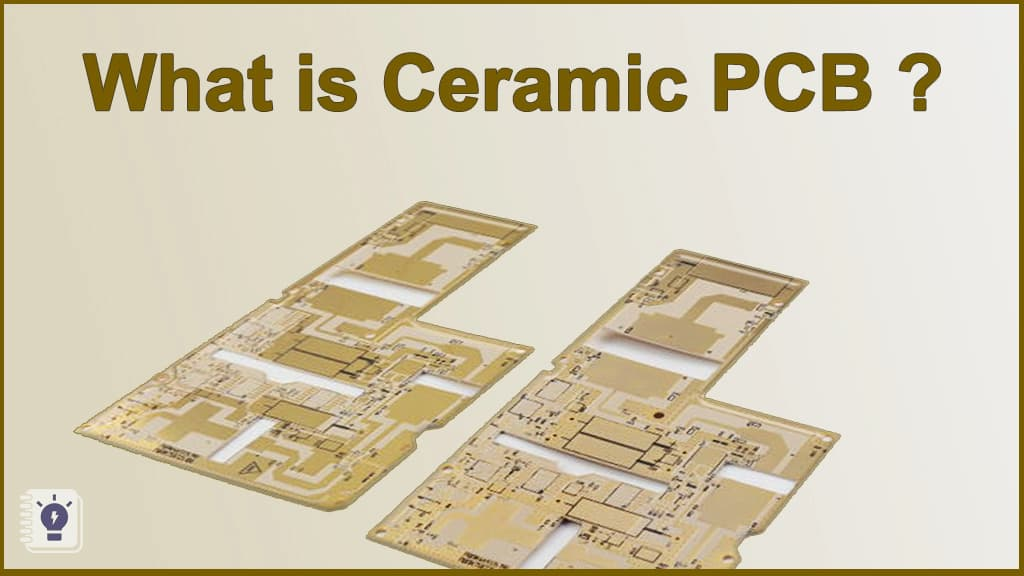
Thermal Management: Why Ceramic PCB Takes the Lead
Thermal management is critical in PCB design, especially for high-power and high-frequency applications. Ceramic PCBs outperform FR4 PCBs due to their superior thermal conductivity. For example, aluminum nitride (AlN) has a thermal conductivity of 170-200 W/mK, compared to just 0.3 W/mK for FR4.
This high thermal conductivity allows ceramic PCBs to dissipate heat efficiently, preventing overheating and ensuring stable performance. In contrast, FR4 PCBs struggle with heat dissipation, making them less suitable for applications like power electronics, LED lighting, and automotive systems. Ceramic PCBs are a clear choice if your project involves high heat generation.
Electrical Performance: A Key Differentiator
Ceramic PCBs and FR4 PCBs also differ significantly in electrical performance. Ceramic PCBs offer low dielectric loss and excellent signal integrity, making them ideal for high-frequency applications such as RF and microwave circuits. Their stable electrical properties ensure minimal signal distortion, even at high frequencies.
FR4 PCBs, while adequate for low-frequency applications, exhibit higher dielectric loss and signal attenuation at higher frequencies. This limits their use in advanced communication systems and high-speed digital circuits. For projects requiring precise electrical performance, ceramic PCBs provide a significant advantage.
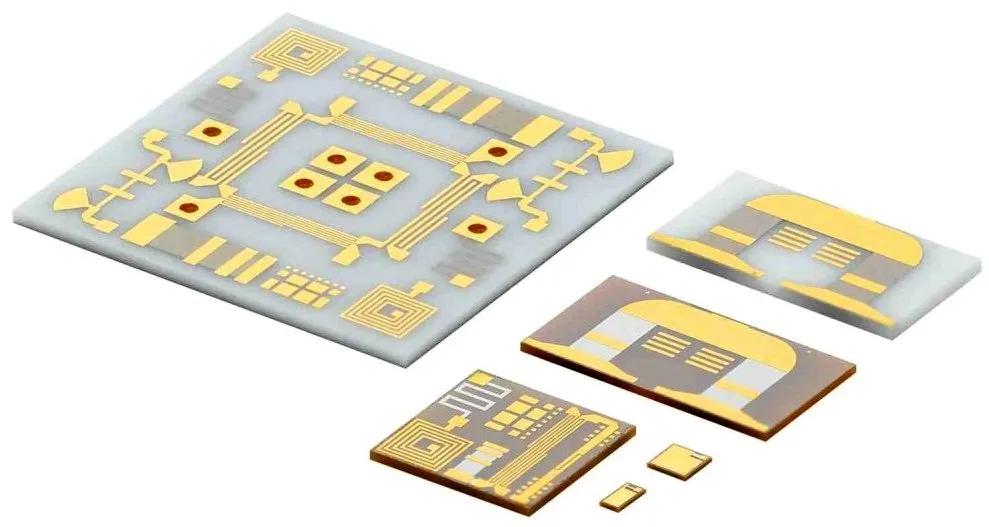
Mechanical Strength and Durability
Mechanical strength and durability are crucial for PCBs used in harsh environments. Ceramic PCBs are known for their exceptional mechanical properties, including high hardness, wear resistance, and resistance to thermal shock. These characteristics make them suitable for aerospace, military, and industrial applications.
While durable for general use, FR4 PCBs cannot match the mechanical robustness of ceramic PCBs. They are more prone to warping, cracking, and delamination under extreme conditions. Ceramic PCBs offer superior reliability if your project involves exposure to high-stress or harsh environments.
Cost Considerations: Balancing Performance and Budget
Cost is often a deciding factor when choosing between ceramic PCBs and FR4 PCBs. Ceramic PCBs are more expensive due to their advanced materials and manufacturing processes. However, their superior performance and durability can justify the higher cost for specialized applications.
FR4 PCBs, on the other hand, are cost-effective and widely available. They are ideal for budget-conscious projects or applications where high performance is not a priority. When deciding between the two, consider your project’s specific requirements and weigh the benefits of ceramic PCBs against their higher cost.
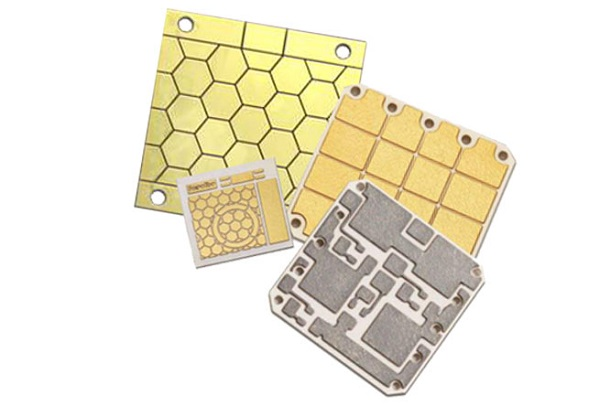
Applications: Where Each PCB Shines
The choice between ceramic PCBs and FR4 PCBs often depends on the application. Ceramic PCBs are preferred for high-performance applications such as power electronics, RF and microwave circuits, LED lighting, and automotive systems. Their ability to handle high temperatures and provide excellent thermal management makes them indispensable in these fields.
FR4 PCBs are commonly used in consumer electronics, telecommunications, and general-purpose circuits. Their affordability and versatility make them a popular choice for less demanding applications. Understanding the strengths of each material will help you select the correct PCB for your project.
Environmental Impact: A Growing Concern
Sustainability is becoming increasingly important in PCB design. Ceramic PCBs are more environmentally friendly than FR4 PCBs due to their durability and recyclability. Their long lifespan reduces the need for frequent replacements, minimizing electronic waste.
While recyclable, FR4 PCBs are less durable and may require more frequent replacements. Additionally, the epoxy resin used in FR4 can release harmful chemicals during manufacturing and disposal. For eco-conscious projects, ceramic PCBs offer a greener alternative.
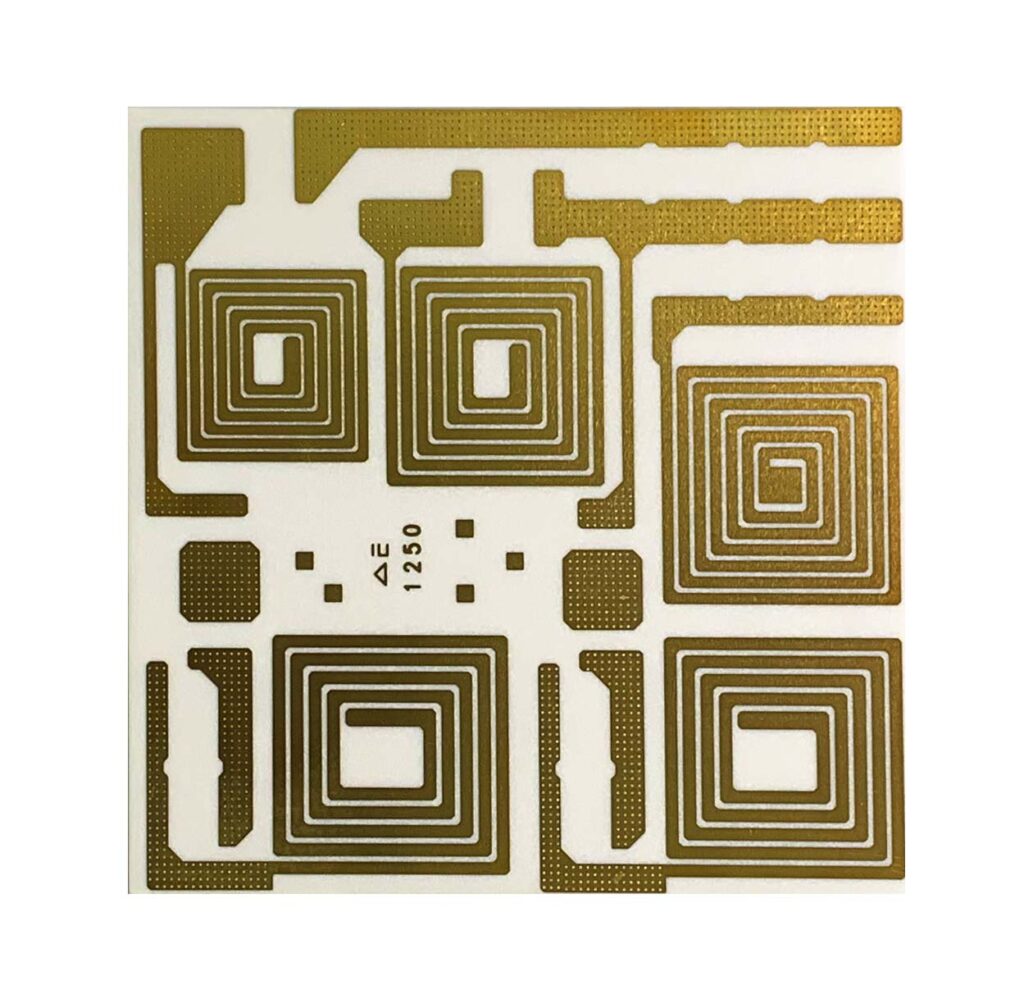
Why Ceramic PCB is the Future of High-Performance Electronics
The demand for high-performance, reliable, and sustainable PCBs grows as technology advances. Ceramic PCBs meet these demands with exceptional thermal, electrical, and mechanical properties. While FR4 PCBs remain a cost-effective option for general-purpose applications, ceramic PCBs are chosen for specialized, high-performance projects.
Ready to elevate your project with ceramic PCBs? Contact us today to learn more about our high-performance solutions!