What is the maximum number of layers in a multilayer PCB?
Multilayer PCB has become a fundamental component in the design and manufacture of modern electronics. These boards allow for more compact designs, higher performance, and greater functionality than traditional single or double-layer boards. The ability to stack multiple layers of conductive material and interconnecting circuitry has revolutionized the electronics industry, enabling manufacturers to integrate more components into smaller spaces. In this blog post, we will explore the maximum number of layers a multilayer PCB can have, the benefits of different layer counts, and the impact of choosing higher layer counts for your PCB design.
The Structure and Design of Multilayer PCB
Multilayer PCBs consist of several layers of conductive material separated by insulating layers. These layers are typically made of copper, while the insulating material is often a resin or fiberglass. The design of multilayer PCBs is crucial in ensuring signal integrity and power distribution. The layers are usually interconnected via vias, tiny holes drilled through the PCB that allow electrical signals to pass from one layer to another. These interconnections ensure that the multiple layers of a PCB work together cohesively, supporting the complex functionality of modern electronic devices.
The number of layers in a multilayer PCB can vary depending on the complexity of the design. For example, a 4-layer PCB is standard in consumer electronics, while more advanced systems may require 6, 8, or even 10 layers. However, as the number of layers increases, so does the complexity of the manufacturing process, which can lead to higher costs and longer lead times. Stacking layers is a delicate process that requires precision to ensure all layers are aligned and bonded correctly to maintain the board’s structural integrity. As the layer count rises, the PCB also becomes thicker, which could affect the design of the housing or enclosure, especially in compact devices.
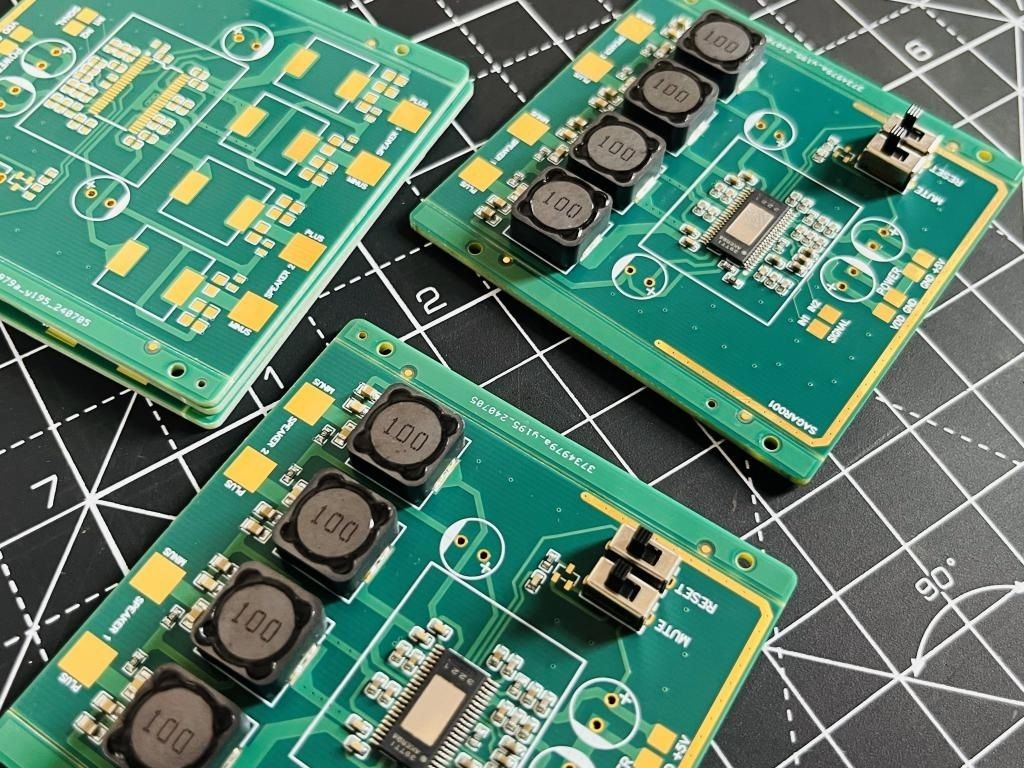
The Manufacturing Process and Layer Limitations
The manufacturing process for multilayer PCBs involves several intricate steps. First, manufacturers etch the copper to form the traces and pads on each layer. After creating the individual layers, manufacturers stack them together and bond them using a high-temperature process. Manufacturers drill vias to make interconnections between the layers. This process aligns all layers precisely, which is critical for maintaining signal integrity. Depending on the number of layers, manufacturers may need to take additional steps to ensure the quality and functionality of the board.
While there is no absolute upper limit to the number of layers a multilayer PCB can have, practical limitations exist. As the number of layers increases, the thickness of the PCB also increases, making it harder to manage heat dissipation and signal integrity. The more layers there are, the more likely there will be challenges related to the uniformity of the layers, potential signal degradation, or mechanical stress. Additionally, the complexity and cost of the manufacturing process rise with each additional layer, making high-layer-count boards expensive to produce.
Common Layer Counts for Multilayer PCB
The most common layer configurations for multilayer PCBs are typically based on the requirements of the device or application. Designers commonly use a 4-layer PCB in consumer electronics because it balances performance and cost well. People often find these in devices like smartphones, laptops, and tablets. The 4-layer configuration allows for better signal integrity and power distribution than simpler single or double-layer designs, especially when dealing with high-speed signals and complex component arrangements.
For more advanced applications, such as telecommunications, automotive electronics, or medical devices, 6 to 10 layers are commonly used. These applications require higher performance, more components, and sometimes better isolation between different circuit parts. By adding more layers, designers can create more compact and functional designs while maintaining high-performance levels. In some instances, designers may need to add more layers to meet the requirements of complex systems, though these boards are typically more specialized and expensive.
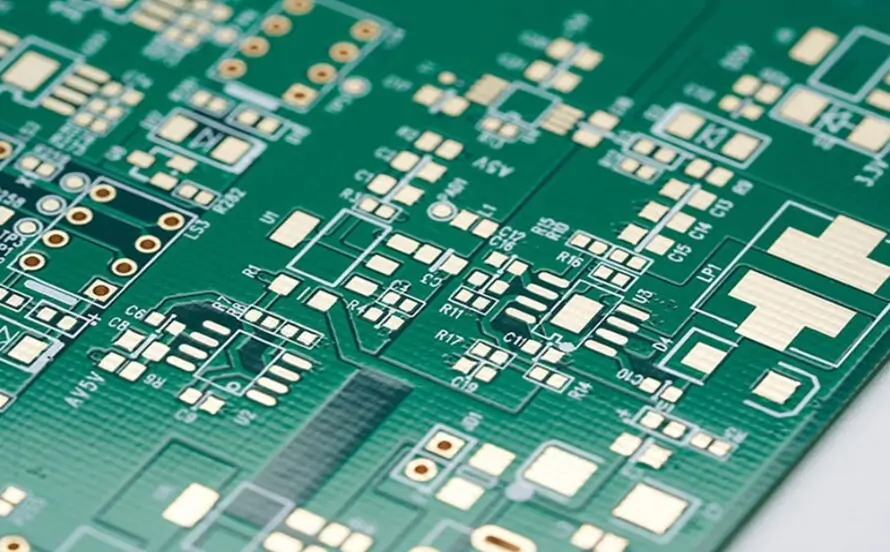
Factors That Influence the Number of Layers
The decision on how many layers several factors influence a PCB’s needs. One of the most important considerations is the complexity of the circuit itself. High-frequency circuits, for example, benefit from additional layers that help maintain signal integrity. A higher number of layers provides better power distribution and allows for better separation of signal and power planes, which can improve performance and reduce electromagnetic interference (EMI). Additionally, the size of the device and the need for compact designs often necessitate more layers to fit all the components and connections into a small space.
Other factors include space constraints, the need for shielding, and cost considerations. In highly compact devices, where space is at a premium, it is often necessary to use multilayer PCBs to pack more components into a smaller footprint. On the other hand, using fewer layers may be sufficient for low-cost consumer electronics to achieve the necessary performance without driving up costs. When designing a multilayer PCB, manufacturers must carefully consider these factors to ensure the final design meets performance and cost goals.
Maximum number of layers on a PCB
Theoretically, there is no fixed upper limit to the number of layers that can be added to a PCB. However, practical considerations like heat dissipation, signal integrity, and manufacturing complexity restrict multilayer PCBs to 30 to 40 layers. It is possible to produce boards with even more layers in extremely high-performance applications, though these are rare and typically custom-designed for specific applications.
Specialized industries such as aerospace, military, and high-performance computing typically use high-layer-count PCBs. For example, satellite systems, radar equipment, and military electronics often require PCBs with 30 or more layers. These systems demand high reliability, compact designs, and advanced features requiring a higher layer count. However, these high-layer-count PCBs come at a premium price and require advanced manufacturing techniques.
The Benefits of Multilayer PCB
The primary advantage of multilayer PCBs is their ability to support more complex circuits in a smaller form factor. Manufacturers can increase the components’ density by adding more layers, allowing for smaller and more powerful devices. Multilayer PCBs also offer improved electrical performance, reduced electromagnetic interference (EMI), and better heat dissipation, making them ideal for high-speed or high-frequency applications.
In high-frequency circuits, multilayer PCBs help reduce signal degradation and noise. Additional layers allow for better separation of power and signal traces, which improves performance by reducing crosstalk and interference. Multilayer designs also help with heat distribution, as the layers can be designed to dissipate heat more effectively than a more straightforward design. This makes multilayer PCBs an ideal choice for applications that require reliable and high-performance operation over long periods.
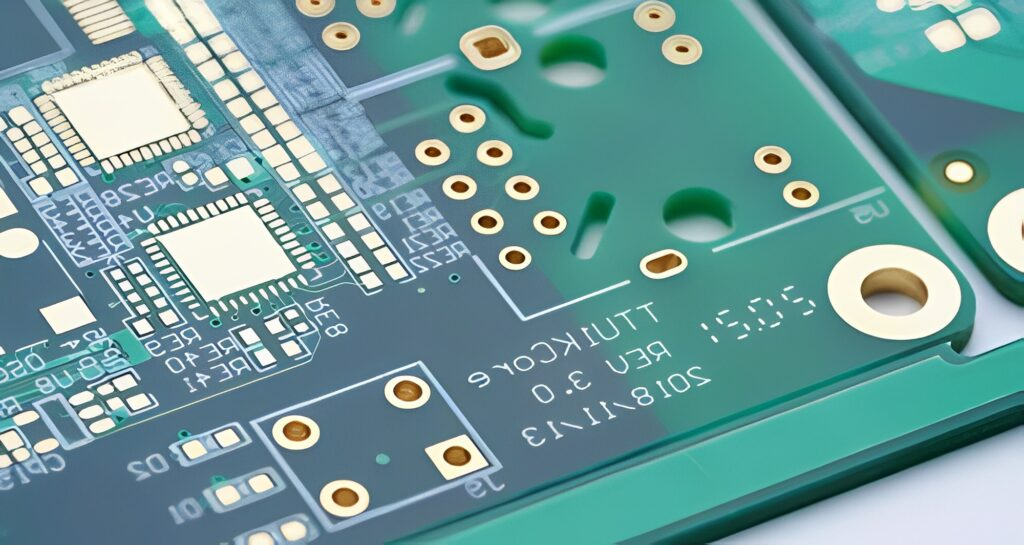
Cost and Lead Time Considerations
The number of layers in a PCB directly impacts its cost and lead time. As the number of layers increases, so do the costs of materials, labor, and production time. More layers mean more complexity in the design and manufacturing process, which can result in higher engineering and production costs. The lead time for manufacturing multilayer PCBs with higher layer counts is typically longer due to the increased complexity and the precision required to ensure all layers are correctly aligned and bonded.
When designing a PCB, weighing the cost and lead time against the benefits of using more layers is essential. In some applications, the performance advantages of additional layers may justify the higher price. However, in other cases, a simpler PCB with fewer layers may be sufficient to meet the application’s needs. Understanding the trade-offs can help businesses choose the right PCB design for their projects while staying within budget and time constraints.
Selecting the Right Number of Layers for Your PCB
The maximum number of layers for a multilayer PCB depends on various factors, including the complexity of the design, performance requirements, and manufacturing capabilities. While high-layer-count PCBs can offer significant performance benefits, such as better signal integrity and component density, they also cost more and have longer lead times. As technology advances, the demand for multilayer PCBs will continue to grow. New manufacturing techniques, better materials, and more efficient production processes may enable higher-layer-count PCBs. However, the fundamental principle of balancing cost, performance, and complexity will always be at the core of PCB design.