What Make Ceramic PCB Ideal for Aerospace and Automotive Industries?
In today’s competitive and rapidly evolving aerospace and automotive sectors, the demand for high-performance components has never been greater. Innovation in these fields is often driven by advancements in materials science, especially in areas requiring reliability, efficiency, and performance under extreme conditions. Among the many materials available, ceramic PCBs stand out as an exceptional choice for aerospace and automotive applications. A ceramic PCB has become a preferred option in these industries because of its superior thermal conductivity, mechanical strength, and resilience. This article will explore the key qualities that make ceramic PCBs ideal for aerospace and automotive systems, focusing on how they contribute to performance, cost-effectiveness, and sustainability.
Thermal Management: Crucial for Aerospace and Automotive Systems
Effective thermal management is one of the most significant challenges in the aerospace and automotive industries. The electronic systems in these sectors operate under extreme temperature conditions, and failing to control heat can lead to system malfunctions or even catastrophic failures. Ceramic PCBs excel in this regard due to their high thermal conductivity, which allows for efficient heat dissipation. Aerospace applications, such as avionics and radar systems, require components that can function in freezing or extreme heat conditions. With materials like aluminum nitride (AlN) and aluminum oxide (Al2O3), Ceramic PCBs provide an effective solution by conducting heat away from sensitive components, preventing overheating.
Similarly, in automotive applications, where components like powertrains and control units generate significant heat, ceramic PCBs help maintain optimal operating temperatures. This enhanced thermal performance ensures systems can run continuously without failure, even under high-stress conditions. The superior heat resistance of ceramic PCBs contributes to better reliability and longevity for high-performance systems in both sectors, making them indispensable for critical applications where heat management is essential.
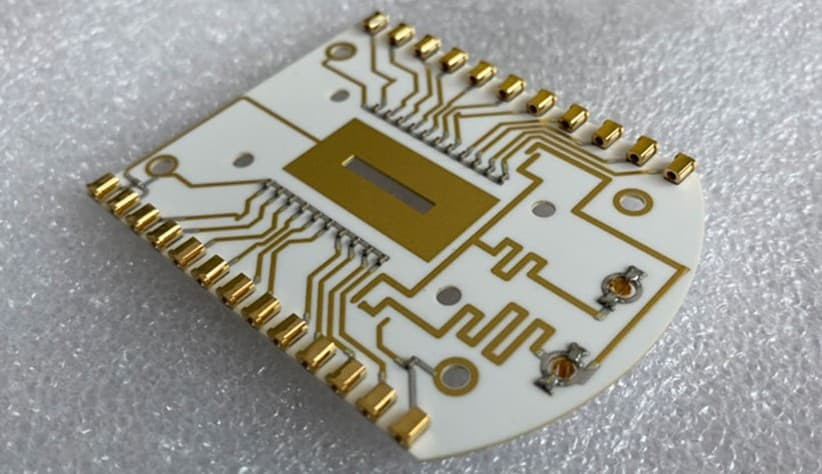
Durability and Mechanical Strength: Resisting Harsh Conditions
Aerospace and automotive systems face mechanical stress through vibrations, impacts, and extreme environmental conditions. For aerospace applications, aircraft experience a wide range of stresses during flight, from turbulent weather conditions to the forces experienced during take-off and landing. Automotive systems also encounter vibrations and physical impacts due to road conditions, which can significantly stress electronic components. Ceramic PCBs provide unmatched mechanical strength and durability, making them ideal for high-stress environments.
The rigid structure of ceramic materials makes them resistant to bending, cracking, and warping, ensuring that the PCB maintains its integrity even under heavy mechanical stress. In addition, ceramic PCBs offer excellent resistance to thermal cycling, meaning that they can withstand rapid and frequent temperature changes without degrading. This resistance to mechanical and thermal stresses ensures that systems equipped with ceramic PCBs perform reliably over the long term, even in the harshest conditions. Ceramic PCBs guarantee longevity and durability in avionics, control systems, or engine management units.
Compactness and Miniaturization: Key Benefits of Ceramic PCB Design
The aerospace and automotive industries are trending toward miniaturizing electronic components. Compact designs reduce weight—critical for aerospace systems—and improve energy efficiency and vehicle performance in automotive applications. Ceramic PCBs play a crucial role in enabling this miniaturization. The high thermal conductivity and electrical insulation properties of ceramic materials allow for smaller, more efficient component layouts without compromising performance.
Ceramic PCBs support the integration of more components into a smaller area, which is essential for developing advanced systems such as radar, GPS, and control units. This capacity for miniaturization helps aerospace manufacturers reduce the weight of critical systems, improving fuel efficiency and overall operational costs. Similarly, automotive manufacturers benefit from the ability to design more compact systems that fit within the constraints of vehicle interiors and under-the-hood spaces while maintaining high functionality and reliability.
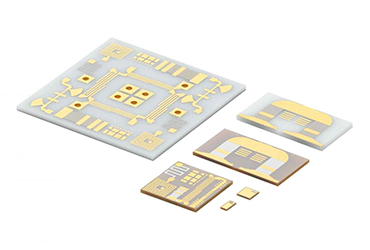
Resistance to Environmental Factors: Ensuring Longevity
Aerospace and automotive industries require components that resist harsh environmental factors like moisture, radiation, and corrosion. Aerospace systems are particularly vulnerable to space, altitude, and weather extremes, where exposure to high radiation levels, moisture, and fluctuating temperatures occurs daily. In automotive systems, components must endure exposure to road salt, dust, moisture, and extreme temperatures, which can cause degradation over time. Ceramic PCBs are highly resistant to these factors, making them ideal for use in both sectors.
Ceramic PCBs’ resistance to moisture and corrosion ensures that they maintain their performance in challenging environments. Furthermore, their longevity reduces the need for frequent replacements, saving manufacturers both time and cost. Ceramic PCBs’ ability to resist environmental wear and tear is critical in aerospace, where system failure can have catastrophic consequences. In automotive applications, their durability ensures the reliability of sensors, control units, and other essential electronic systems.
High-Frequency Performance: Supporting Advanced Systems
High-frequency performance is crucial for aerospace and automotive applications’ communication, control, and navigation systems. Whether it’s radar in aircraft, GPS in vehicles, or communication systems used in both fields, the need for efficient, high-frequency signal transmission is constant. Ceramic PCBs are particularly effective in these applications due to their low dielectric loss and high signal integrity. These properties make ceramic PCBs capable of maintaining clear and accurate signals even at high frequencies, ensuring that systems perform as expected under demanding conditions.
In aerospace, transmitting signals without degradation is essential for radar systems, satellite communication, and avionics. Similarly, in automotive systems, high-frequency performance is necessary for technologies such as autonomous driving, vehicle-to-vehicle (V2V) communication, and advanced navigation systems. Ceramic PCBs help ensure that these critical systems remain operational, with high signal clarity and minimal interference, contributing to the overall reliability of aerospace and automotive technology.
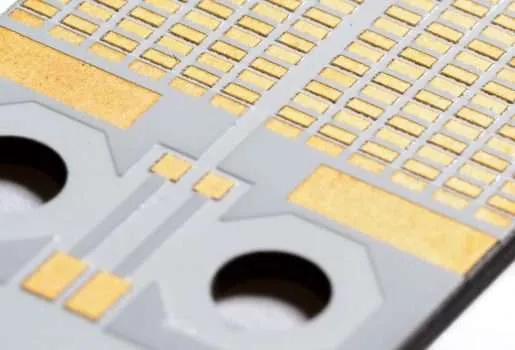
Cost-Effectiveness: Ceramic PCB Balance Performance with Budget
While ceramic PCBs may have a higher initial cost than other materials, their long-term performance, durability, and reliability make them a cost-effective solution for both the aerospace and automotive industries. The longevity and reduced maintenance costs associated with ceramic PCBs make them a wise investment for manufacturers looking to minimize lifecycle expenses. Ceramic PCBs help ensure that products remain reliable and functional throughout their life cycle by reducing the risk of system failure, maintenance, and downtime.
In automotive applications, cost-effectiveness is a crucial factor as manufacturers look to reduce production costs while still delivering high-performance vehicles. Ceramic PCBs help achieve this balance by providing a durable, high-performance solution that doesn’t require expensive cooling systems or frequent replacements. Aerospace manufacturers, too, benefit from the long lifespan of ceramic PCBs, as fewer replacements mean lower operational costs for both commercial and military aircraft. The cost savings over time make ceramic PCBs a practical and cost-effective choice.
Sustainability: Aligning with Environmental Goals
With growing concerns about sustainability and environmental impact, the aerospace and automotive industries are increasingly seeking ways to reduce their carbon footprints. Ceramic PCBs offer several environmental benefits, contributing to these sectors’ sustainability efforts. Compared to traditional PCB materials, the manufacturing process of ceramic PCBs generates less waste and uses fewer hazardous materials, making them a more eco-friendly option.
Moreover, ceramic PCBs’ durability reduces the frequency of replacements, which in turn reduces electronic waste. This contributes to a more sustainable lifecycle for aerospace and automotive components, aligning with global sustainability initiatives. In the automotive sector, ceramic PCBs enhance the energy efficiency of electric vehicles, while in aerospace, they help reduce the environmental impact of aviation by improving the efficiency of systems like navigation and communication.
The Future of Ceramic PCB in Aerospace and Automotive Industries
Ceramic PCBs have proven vital for the aerospace and automotive industries, offering unmatched benefits in terms of thermal management, durability, miniaturization, environmental resistance, and high-frequency performance. Their ability to withstand extreme conditions, maintain signal integrity, and support compact designs makes them a preferred choice for the next generation of aerospace and automotive technologies.