What materials are used in the construction of SSD PCB?
The success of an SSD goes beyond its data storage technology; it heavily relies on the quality of the materials used in constructing its core component — the SSD PCB. The SSD PCB is the central platform that interconnects all critical components, such as the flash memory chips, controllers, and power circuits. The choice of materials used in the PCB directly affects the SSD’s overall durability, reliability, speed, and heat resistance. This article will explore the different materials used in SSD PCBs, shedding light on their importance and role in achieving optimal performance.
The Role of PCB Substrate Materials in SSD PCB Construction
The substrate material forms the SSD PCB’s backbone, providing structural integrity and insulation for electrical circuits. The most widely used material for PCB substrates is fiberglass-reinforced epoxy resin, commonly known as FR4. This material is favored for its mechanical strength, electrical insulation properties, and cost-effectiveness. FR4 comprises woven fiberglass bonded with epoxy resin, creating a sturdy yet flexible substrate ideal for consumer electronics, including SSDs.
FR4 is an ideal choice for SSD PCBs because of its excellent dielectric properties, which help to prevent electrical interference between the PCB’s copper layers. This ensures signals pass through the PCB without degradation, enabling high-speed data transfer. Additionally, FR4 can withstand the high-frequency operations typical in SSDs, ensuring the device operates smoothly even under heavy workloads. However, manufacturers may use more advanced substrate materials like polyimide or ceramic for high-performance or specialized SSDs. These materials offer enhanced thermal stability and flexibility, making them ideal for applications requiring extreme conditions or specialized form factors.
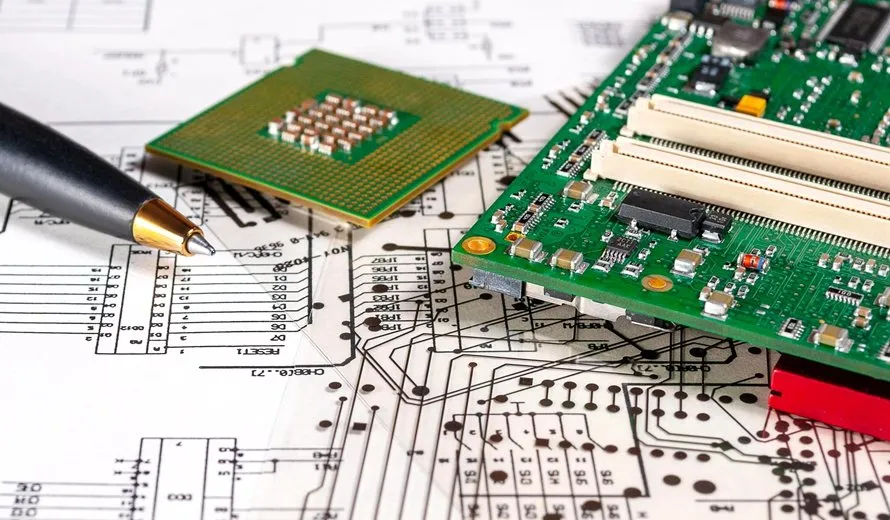
Copper Cladding: The Heart of Electrical Conductivity in SSD PCB
Copper cladding is one of the most crucial elements in constructing SSD PCBs. Coats the substrate, creating the conductive traces that allow electrical signals to travel between different components on the PCB. The copper layers are carefully etched into specific patterns, forming complex circuits connecting the SSD’s memory chips, controller, and other system parts. Copper is preferred for its high electrical conductivity, which is essential for quickly and efficiently transferring data.
The quality of the copper cladding plays a significant role in the overall performance of the SSD. Higher-quality copper ensures low resistance and minimal signal loss, enabling faster read and write speeds. Additionally, copper’s ability to dissipate heat is critical in preventing the PCB from overheating. As SSDs operate at high speeds, heat generation is inevitable, and copper’s thermal conductivity helps distribute heat efficiently across the board. The thickness of the copper layer is also an important consideration, with standard copper thickness ranging from 0.5 oz to 3 oz per square foot, depending on the application’s requirements. Thicker copper layers provide better heat dissipation and improve signal integrity, making them ideal for high-performance SSDs.
Solder Mask: Protecting the PCB and Enhancing Durability
The solder mask is another essential material used to construct SSD PCBs. After the copper traces are etched onto the PCB, a solder mask is applied to protect the copper and prevent accidental short circuits during the soldering process. This layer also provides insulation, ensuring electrical currents do not leak between traces. The solder mask is typically made of epoxy or liquid photo-imageable (LPI) coatings, which are durable, heat-resistant, and provide a protective barrier against environmental contaminants like moisture, dust, and chemicals.
One of the solder mask’s key roles is safeguarding the PCB’s integrity throughout its lifespan. By preventing corrosion and protecting the copper traces from physical damage, the solder mask ensures that the SSD maintains its reliability and performance over time. The solder mask also serves an aesthetic purpose, with many SSD manufacturers using colored solder masks to create visually appealing designs for their products. Green is the most common color, but manufacturers can choose various colors depending on branding or design preferences. The durability of the solder mask is vital for ensuring that the SSD PCB can withstand various external stresses, making it a crucial material in enhancing the drive’s longevity.
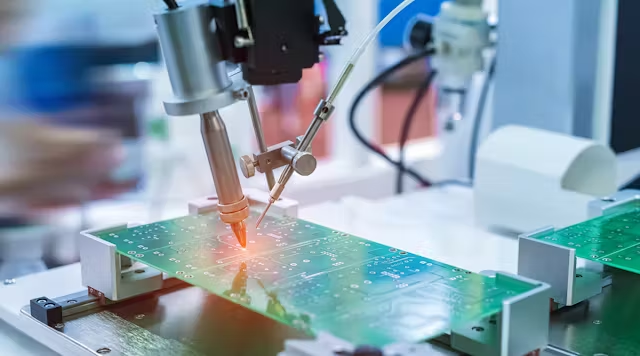
Via Fillers and Plating: Ensuring Signal Integrity and Manufacturing Efficiency
Vias are small conductive holes that allow electrical connections between different layers of the PCB. In SSD PCBs, vias are essential for routing electrical signals from one layer to another, enabling more compact designs and efficient data flow. After the vias are drilled, they are filled and plated with materials like copper to ensure robust electrical conductivity and prevent corrosion or signal degradation. Via plating is a key factor in maintaining signal integrity, as any imperfections in the plating can lead to unreliable data transmission.
Copper via plating ensures seamless electrical signal flow through the PCB, enabling faster and more accurate data transfers. High-performance SSDs may use gold-plated vias for better conductivity and enhanced protection against wear and corrosion. Moreover, using high-quality fillers and plating materials improves manufacturing efficiency by reducing defects during production. This leads to fewer production delays and greater consistency in the final product. Properly filling and plating vias is crucial for SSD reliability, as poor construction can lead to failure or reduced performance.
Component Materials: Flash Memory Chips, Controllers, and Capacitors on PCB
While the PCB is built using various materials, it also serves as the platform for placing key components such as flash memory chips, controllers, and capacitors. These components are crucial to SSD performance and must be carefully arranged on the PCB to maximize efficiency. Flash memory chips, made from NAND flash memory, store the data on the SSD. NAND flash is preferred for its high speed and non-volatile nature, retaining data even when powered off.
Controllers are another vital component of SSDs. These semiconductor chips manage the data flow between the memory chips and the computer, controlling read and write operations and ensuring the drive operates smoothly. Capacitors are also placed on the PCB to stabilize the power supply and prevent voltage fluctuations that could interfere with the SSD’s operation. These components are made from silicon and tantalum, which are known for their excellent conductivity and high voltage resistance. These components’ precise placement and connection on the PCB are crucial for ensuring that the SSD functions appropriately. Any design or material selection flaw could lead to suboptimal performance or device failure.
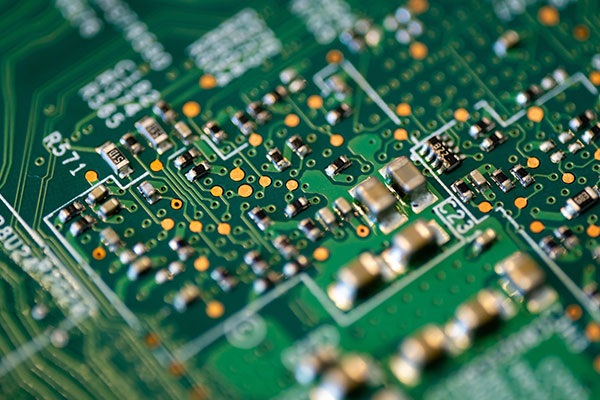
Thermal Management Materials: Ensuring Efficient Heat Dissipation in PCB
SSDs perform high-speed data processing, generating heat, which can potentially harm the components on the PCB if not correctly managed. Therefore, efficient heat dissipation is a critical consideration in SSD PCB design. Manufacturers use various thermal management materials such as copper, aluminum, and thermal vias to address this. Copper is often used for its high thermal conductivity, allowing heat to be efficiently spread across the PCB. Thermal vias, small copper-plated holes, are incorporated to improve heat transfer between PCB layers, enhancing cooling.
In high-performance SSDs, additional thermal management materials, such as heat sinks or thermally conductive pads, may help dissipate excess heat. Materials like aluminum, graphite, or ceramics efficiently cool the PCB, preventing overheating during intense data processing tasks. Proper thermal management is vital for SSD longevity and performance, especially in high-demand environments like data centers or gaming PCs. Overheating can lead to system instability, slower performance, and component failure. By incorporating thermal management materials, manufacturers can ensure that the SSD maintains optimal operating conditions even during high-intensity use.
Environmental Considerations: Sustainable Materials for PCB
The materials used to construct SSD PCBs are also evolving with growing environmental concerns. Manufacturers are increasingly exploring eco-friendly alternatives to traditional materials, seeking ways to reduce the environmental impact of electronic waste. For example, some SSD manufacturers consider halogen-free flame retardants in the PCB substrate to reduce harmful chemicals. Additionally, efforts are being made to find recyclable or biodegradable alternatives to the metals and resins typically used in PCBs.
The shift towards sustainability in SSD manufacturing is driven by reducing environmental harm and consumer demand for eco-friendly products. Many consumers are now prioritizing sustainable electronics, and manufacturers are responding by adopting greener production practices. For instance, using lead-free solder and recyclable materials can reduce the carbon footprint of the entire product lifecycle. Adopting these materials ensures SSD manufacturers comply with electronic waste regulations, enhancing the product’s environmental sustainability.
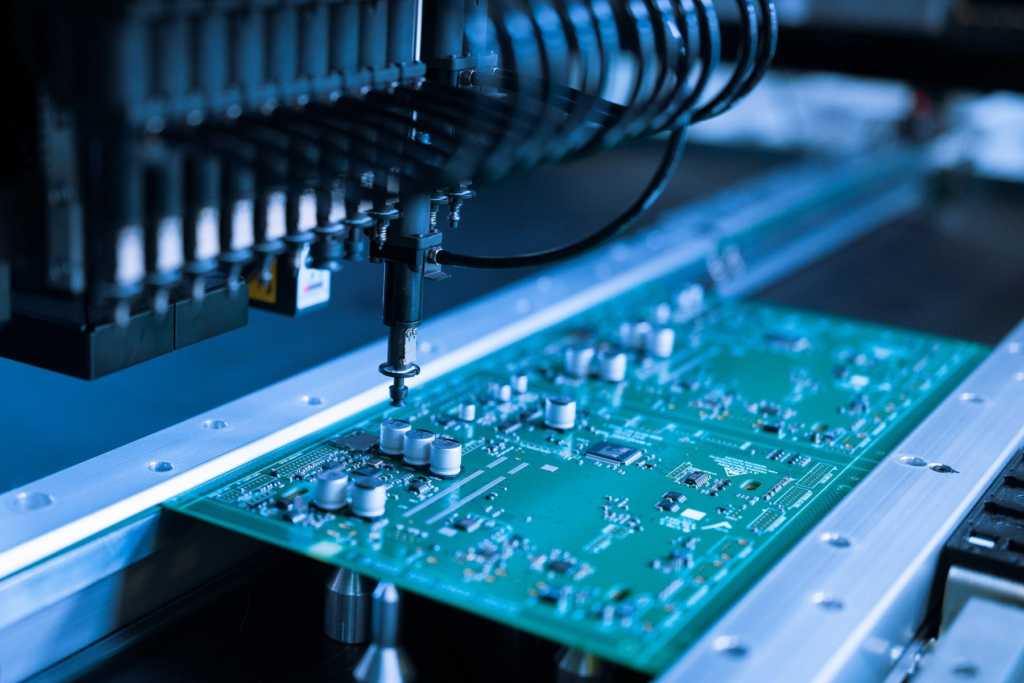
The Future of SSD PCB Materials
The materials used in SSD PCB construction are crucial in determining the drive’s performance, durability, and reliability. From the choice of substrate materials and copper cladding to the inclusion of thermal management and sustainable alternatives, each material serves a specific purpose in enhancing the functionality of the SSD. As technology continues to evolve, the materials used in SSD PCBs will also advance, leading to faster, more efficient, and eco-friendly storage solutions. By understanding these materials, consumers and manufacturers can make informed choices that lead to high-quality, long-lasting SSDs.