Why Quality Control Matters in Heavy Copper PCB Manufacturing
In the world of electronics, Heavy Copper PCB has become a cornerstone for high-power applications. These robust circuit boards, from automotive systems to renewable energy solutions, handle extreme currents and temperatures. However, their reliability hinges on one critical factor: quality control. Even the most advanced designs can fail without stringent quality checks, leading to costly recalls, safety hazards, and damaged reputations. This article dives deep into why quality control is non-negotiable in Heavy Copper PCB manufacturing and how it ensures performance, durability, and trust.
The Role of Precision in Heavy Copper PCB for High-Power Applications
Heavy Copper PCB is designed to carry high currents and dissipate heat efficiently. This makes precision in manufacturing vital. Even a minor defect, like an uneven copper layer or a tiny crack, can lead to catastrophic failures. For instance, a faulty PCB might cause a vehicle’s braking system to malfunction in automotive electronics.
Quality control ensures that every layer of copper is evenly distributed and that the board meets exact specifications. Advanced techniques like Automated Optical Inspection (AOI) and X-ray imaging help detect flaws invisible to the naked eye. By maintaining precision, manufacturers guarantee that Heavy Copper PCB performs reliably under extreme conditions.
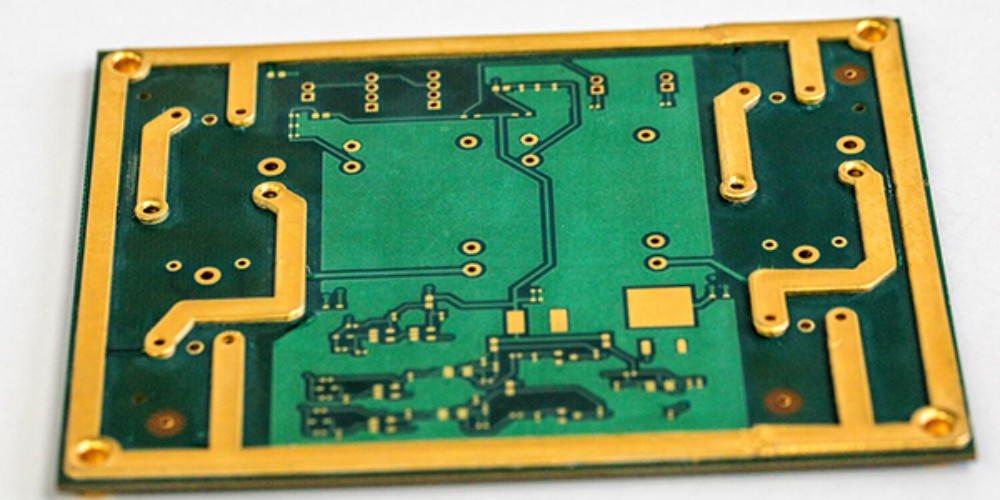
Ensuring Durability of Heavy Copper PCB in Harsh Environments
One of the standout features of Heavy Copper PCBs is their ability to withstand harsh environments. Whether it’s the scorching heat of an industrial furnace or the vibrations of an aircraft, these boards must endure without fail. Quality control plays a pivotal role here.
Tests like thermal cycling, vibration analysis, and humidity resistance checks ensure the PCB can handle real-world stresses. For example, Heavy Copper PCB must survive decades of exposure to weather extremes in renewable energy systems. Without rigorous testing, the risk of premature failure skyrockets, leading to costly replacements and downtime.
Meeting Industry Standards and Certifications
In aerospace, medical devices, and automotive industries, compliance with standards is non-negotiable. Organizations like IPC (Association Connecting Electronics Industries) set strict Heavy Copper PCB manufacturing guidelines. These standards cover everything from material selection to final inspection.
Quality control ensures that every board meets or exceeds these benchmarks. For instance, IPC-6012 Class 3 standards are mandatory for aerospace applications, where failure is not an option. By adhering to these standards, manufacturers build trust with clients and ensure their products are safe and reliable.
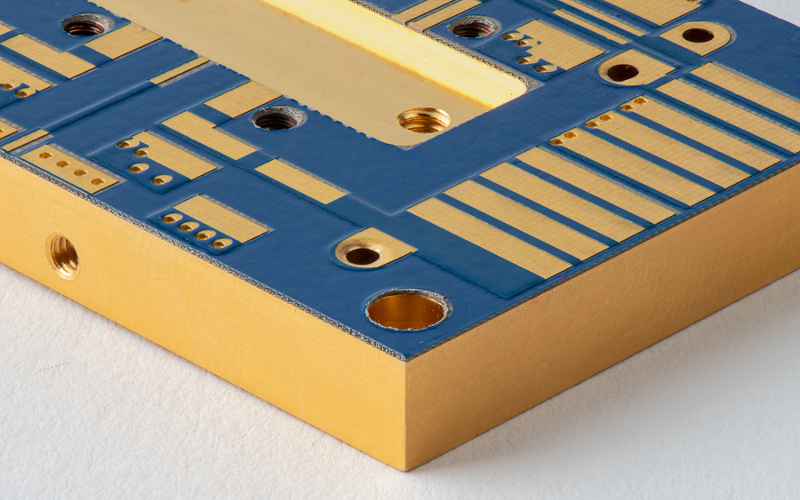
Preventing Costly Failures and Recalls
A single defective Heavy Copper PCB can lead to massive financial losses. Imagine a batch of faulty boards being installed in electric vehicles. The cost of recalling and replacing these units would be astronomical. Worse, it could damage the brand’s reputation irreparably.
Quality control acts as a safety net, catching defects before they leave the factory. Techniques like Electrical Testing (ET) and In-Circuit Testing (ICT) verify that every board functions as intended. Manufacturers save money in the long run by investing in quality control and protecting their clients from costly setbacks.
Enhancing Performance Through Consistency
Consistency is key in Heavy Copper PCB manufacturing. Clients expect every board to perform identically, whether the first or the thousandth unit. Quality control ensures this consistency by monitoring every stage of production.
For example, even slight variations in copper thickness can affect signal integrity in high-frequency applications. By maintaining tight tolerances, manufacturers deliver boards that meet exact performance criteria. This consistency is especially crucial in industries like telecommunications, where reliability is paramount.
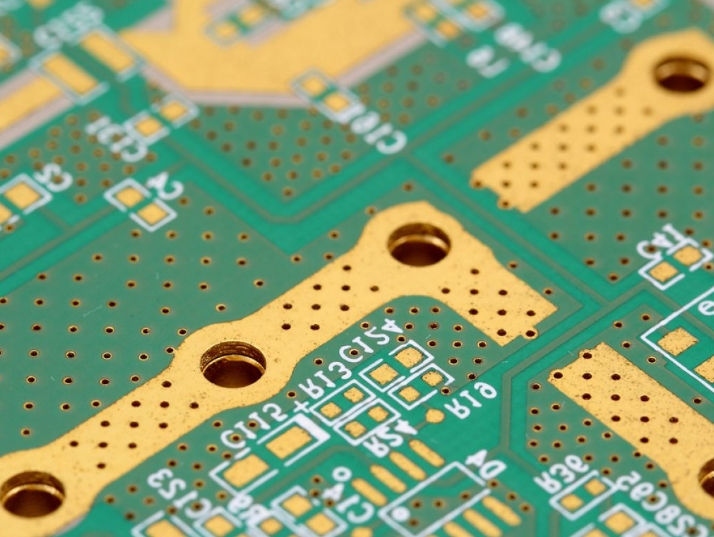
Building Trust with Clients
Trust is the foundation of any successful business relationship. When clients choose a Heavy Copper PCBs supplier, they trust that manufacturer’s ability to deliver quality products. Quality control is the backbone of this trust.
By providing detailed inspection reports and certifications, manufacturers demonstrate their commitment to excellence. Clients can rest assured that their orders will meet the highest standards. This trust not only secures repeat business but also fosters long-term partnerships.
Supporting Innovation and Customization
As technology evolves, so do the demands on Heavy Copper PCBs. Clients increasingly seek customized solutions for unique applications. Quality control ensures that these innovative designs are executed flawlessly.
For instance, a client might need a PCB with ultra-thick copper layers for a high-current application. Quality control verifies that the design meets the client’s specifications and performs as expected. This flexibility allows manufacturers to push the boundaries of what’s possible with Heavy Copper PCB.
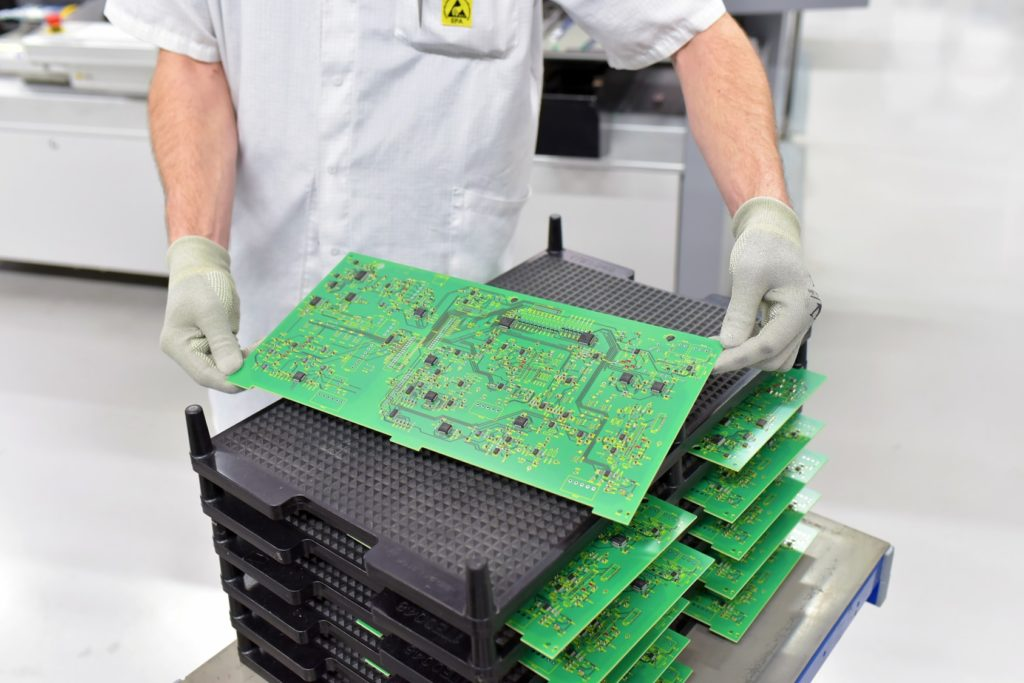
The Future of Quality Control in PCB Manufacturing
The future of Heavy Copper PCB manufacturing lies in more intelligent, more efficient quality control methods. Technologies like Artificial Intelligence (AI) and Machine Learning (ML) are revolutionizing how defects are detected and prevented.
For example, AI-powered inspection systems can analyze thousands of boards in seconds, identifying patterns that human inspectors might miss. These advancements not only improve accuracy but also reduce production time and costs. Quality control will remain at the heart of Heavy Copper PCB manufacturing as the industry evolves, ensuring reliability and innovation.
The Importance of Quality Control in Heavy Copper PCB Production
Quality control is not just a step in manufacturing—it’s the foundation of excellence in Heavy Copper PCB production. From ensuring precision and durability to building trust and supporting innovation, it plays a critical role in every aspect of the industry. Manufacturers deliver products that meet the highest performance and reliability standards by prioritizing quality control. In a world where electronics are becoming increasingly complex and demanding, quality control is the key to success.